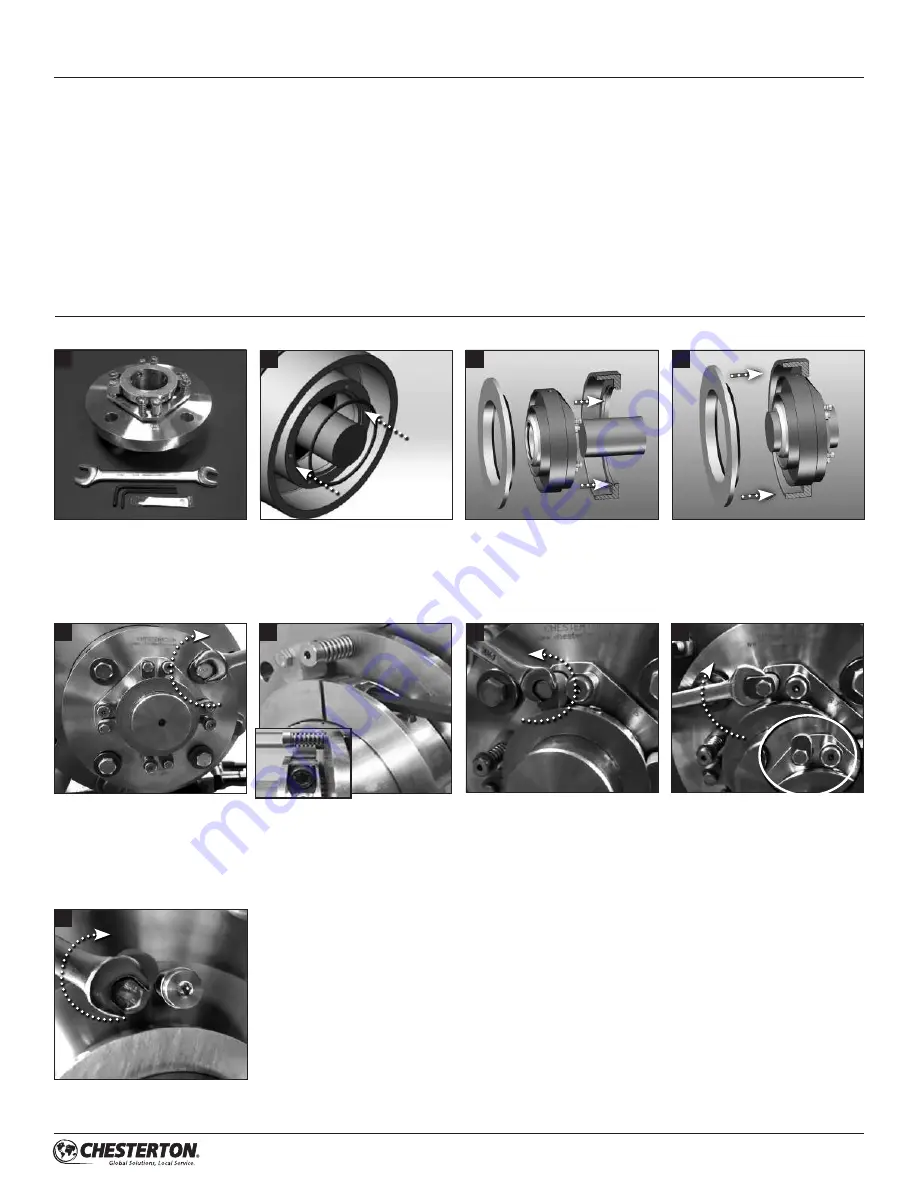
7
4.0 PREPARATION FOR INSTALLATION cont.
4.2 Mechanical Seal
1.
CAUTION:
The 1/4 dog point set screws go into the small
holes in the sleeve. Do not disengage these screws from the
sleeve when positioning the seal. Make sure all screws are
engaged in the sleeve but do not protrude into the ID bore.
Also, when repositioning or removing the seal, make sure the
centering clips and socket head cap screws are engaged.
2. Centering clips have been preset at the factory. If for
any reason you loosen or remove the centering clip cap
screw, retighten as follows prior to installing the seal on the
equipment: Tighten the cap screw finger tight. Then using
hex wrench, tighten cap screw an additional 1/8 turn. This will
approximate the 3,4 Nm (30 inch-pounds) of torque for sizes
45-60 mm (1.75" to 2 1/2"), and 4,5 Nm (40 inch-pounds) of
torque for 65-120 mm (2 5/8" to 4 3/4") set at the factory. For
sizes 25-43 mm (1" to 1.625") tighten the button head screws
to 2,3 Nm (20 inch-pounds) of torque.
5.0 SEAL INSTALLATION
1
Remove seal from packaging and
place on clean work surface.
IMPORTANT:
Remove eye bolts
(if present) prior to installation.
5
Tighten lock ring bolt as specified in
Table 1
.
Reassemble the equipment. Make
all necessary equipment and
impeller adjustments.
7
Turn the clips 180° from their
original position.
6
Loosen the hex head cap screws
attached to the centering clips.
4
Tighten gland bolts as specified in
Table 1
(page 8).
*Only applicable for bolted gland
configuration 85mm-180mm*
8
Retighten the cap screws (to hold
clips in place).
3a
Apply a thin film of grease (provided
with seal) on the shaft. Slide seal
onto the shaft.
3b
Reinstall Frame plate (customer
supplied).
2
Install Gland O-Ring into equipment
prior to seal installation.