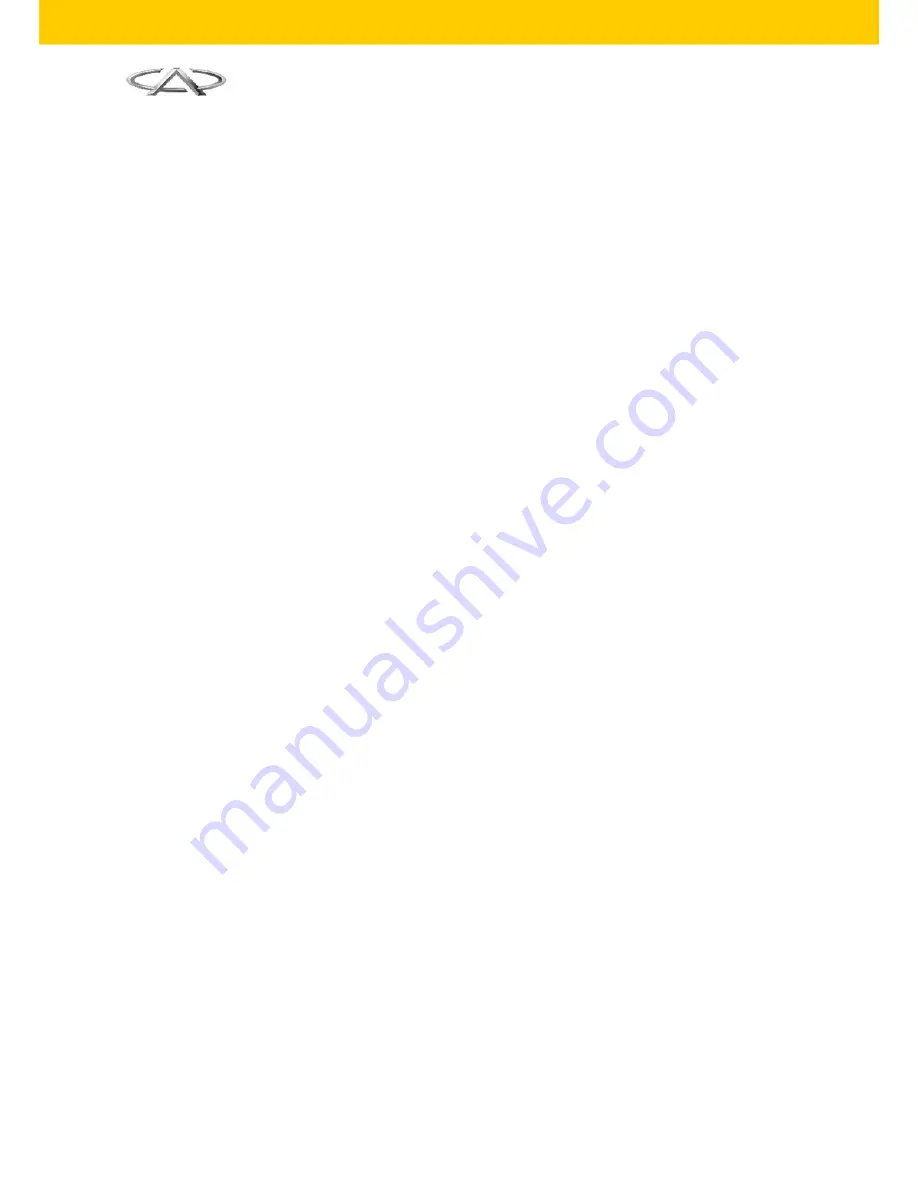
Chery S18D Service Manual
(4) Select proper processing and shaping methods so that the patch matches well with the part to be
removed.
(5) Apply the patch to the intended position and press it tightly, draw a line along the edge of the part
to be removed and cut it out, using methods like gas cutting or excising according to the actual
situation, and then align the patch with the excised area.
(6) Weld the seam by gas welding or carbon oxide protection welding. Spot-weld it at a pace of 30-
50mm to fix it and then weld it again in a certain order after beating it smooth. For seams requiring
welding of higher strength, double-sided welding is preferred.
(7) Smooth the welded seam by beating it with flat hammer, release the welding pressures, and then
shape it and polish the seam with a grinding machine.
4.4. Restoration of Wrinkled Parts
Depending on the damage extent of the plate work pieces, the wrinkles are divided into “live wrinkles”
and “dead wrinkles”. The “live wrinkles” are slight ones and can be directly removed by beating the
convex part with a hammer. The “dead wrinkles” refer to seriously damaged parts. Since the wrinkles
are folded and pressed against each other, so if you hammer the most convex part, the wrinkles would
get even more seriously and harder to release, hence the name “dead wrinkles”. The principle of
correcting the wrinkles is to spread “dead wrinkles” first so that they become “live wrinkles”, and then
“live wrinkles” are converted into convex-concave shape, and finally restore the damaged parts just as
you deal with convex-concave damages. The repairing procedures are as follows:
(1) First use support-draw method to apply a correcting force in the direction opposite to that of the
impact at the wrinkled part of the plate work, and then spread and ease the wrinkles.
(2) Remove the wrinkled plate work and lay it on a platform and then, beginning with the inner side of
the wrinkled area, pry up the wrinkles with a proper prying tool and heat the “dead wrinkles” one by
one with a welding torch at the same time. Finally all “dead wrinkles” are pried up and eased and
converted into” live wrinkle”.
(3) Beat and smooth the “live wrinkles” from the inner side outward. The hammered spots should be
near the most convex part of the “live wrinkles”. At the same time make sure the platform can
support every beaten spot. When the wrinkles in one side of the plate are almost smoothed, turn it
over to beat the other side till all wrinkles are completely spread out.
(4) Measure with a templet, and at the same time heat and beat the convex-concave part to restore it
to its original shape.
(5) When the vehicle body is assembled, test with a templet again and make finer correction to
achieve the final requirements.
(6) The seriously damaged wrinkles that can not be restored can be excised and repaired.
4.5. Welding of Four Doors and Two Covers
When welding the door panel, choose proper welding methods: gas welding (oxygen and acetylene
welding), CO
2
shielded welding, manual arc welding, resistance spot welding, braze welding and so on.
Besides, in order not to reduce the original strength and durability of the vehicle body, try to adopt the
welding methods used in manufacturing the door panels, and the dimensions and types of all weld
joints should be similar to those used by the original manufacturer.
As for appearance and quality, no burnt-through spots, half points, cracks, a lot of burrs or other defects
should exist at the welded parts. The welded surface should be smooth and nice-looking, no obvious
twist or deformation is allowed, and the indentation depth should be less than 1/5 of the plate thickness.
Flat spade and iron hammer can be used to carry out non-destructive tests of the welded spots’
strength. Insert the flat spade between two welded spots to see if they are easy to separate, and then
beat the welded part with an iron hammer to restore it. No welding spatter is allowed at the welded
seam, and the overlapped seam should be nice-looking with no defects like air holes or cracks. Defects
like undercut, welding beading and burning through are also not allowed.
62