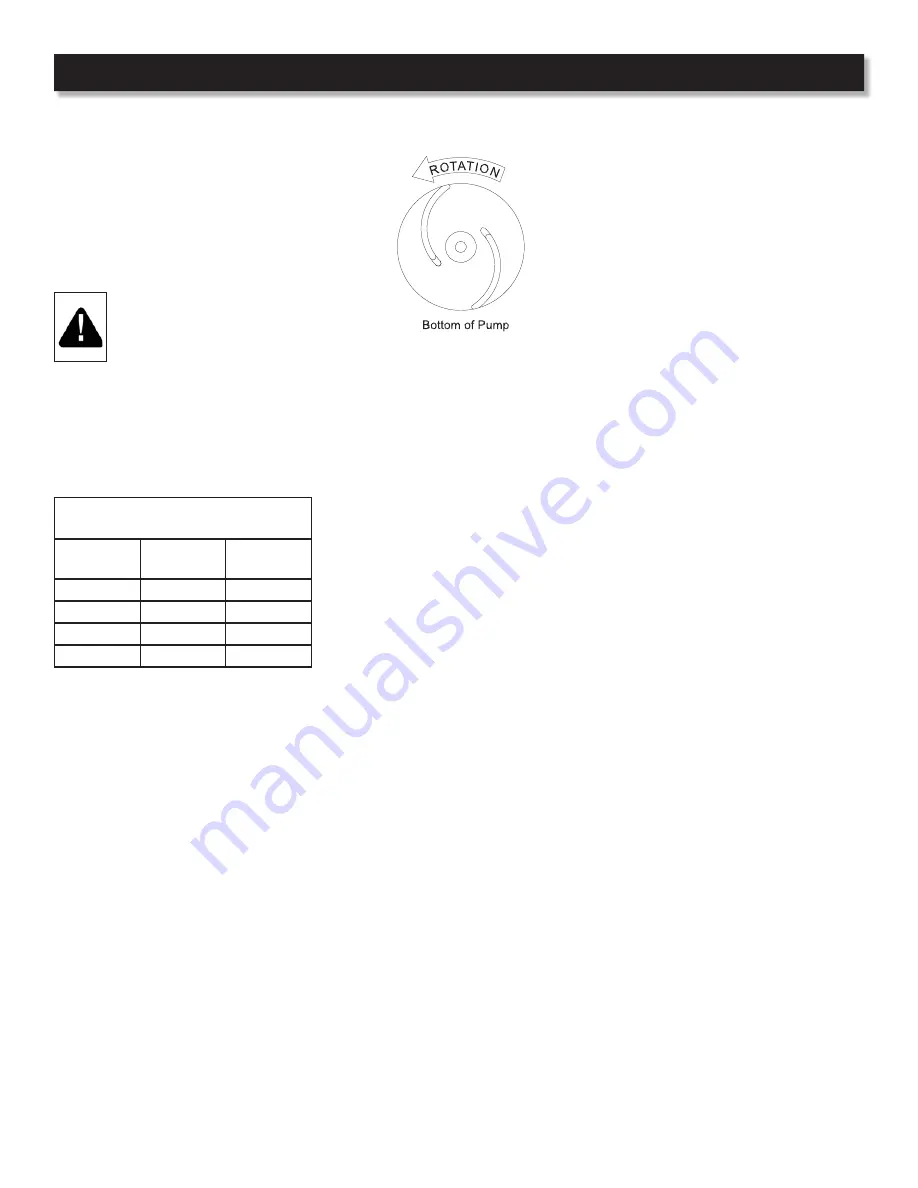
7
C h a m p i o n P u m p C o m p a n y
, Inc • P.O. Box 528 • Ashland, OH 44805
Phone 419-281-4500 • toll free 800-659-4491 • fax 419-616-1100
IMPORTANT ! -
The overload will then
automatically reset and start the pump
up after the motor cools to a safe
temperature. In the event of an overload,
the source of this condition should be
determined and corrected immediately.
WARNING! - DO NOT LET
THE PUMP CYCLE OR RUN IF
AN OVERLOAD CONDITION
OCCURS !
If current through the temperature sensor
exceeds the values listed, an intermediate
control circuit relay must be used to
reduce the current or the sensor will not
work properly.
TEMPERATURE SENSOR ELECTRICAL
RATINGS
Volts
Continuous
Amperes
Inrush
Amperes
110-120
3.00
30.0
220-240
1.50
15.0
440-480
0.75
7.5
600
0.60
6.0
Wire Size:
If longer power cable is required consult
a qualifi ed electrician for proper wire
size.
Pre-Operation
1.
Check Voltage and Phase -
Compare
the voltage and phase information
stamped on the pump name plate.
2.
Check Pump Rotation
- Improper
motor rotation can result in poor
pump performance and can damage
the motor and/or pump. Check
rotation on three phase units by
momentarily applying power and
observe
the
“kickback”.
Kickback should always be in a
counter-clockwise direction as
viewed
from
motor end
or
opposite
to impeller rotation. Impeller rotation
is counter-clockwise as viewed from
bottom of pump.
3.
Name Plate
- Record the information
from the pump name plate to
drawing in front of manual for future
reference.
4.
Insulation Test
- An insulation
(megger) test should be performed
on the motor. Before the pump is put
into service. The resistance values
(ohms) as well as the voltage (volts)
and current (amps) should be
recorded.
5.
Pump-Down Test
- Be sure pump
has been properly wired, lowered into
the basin, sump or lift station, check
the system by filling with liquid and
allowing the pump to operate through
its pumping cycle. The time needed to
empty the system, or pump-down
time along with the volume of water,
should be recorded.
Maintenance
No lubrication or maintenance is required.
Perform the following checks when pump
is removed from operation or when pump
performance deteriorates:
a). Inspect motor chamber for oil level
and
contamination.
b). Inspect impeller and body for
excessive build-up or clogging.
c). Inspect motor, bearings and shaft seal
for wear or leakage.
Servicing
NOTE: Item numbers in ( ) refer to Figures
6 through 9.
Cooling Oil -
Anytime the pump is
removed from operation, the cooling oil
in the motor housing should be checked
visually for oil level and contamination.
To check oil, set unit upright. Remove
pipe plug (20) from housing (4). With a
flashlight, visually inspect the oil in the
housing (4) to make sure it is clean and
clear, light amber in color and free from
suspended particles. Milky white oil
indicates the presence of water. Oil level
should be just above the motor when
pump is in vertical position.
Oil Testing
• Drain oil into a clean, dry container by
placing pump on it’s side, remove pipe
plug (20), from housing (4).
• Check oil for contamination using an
oil tester with a range to 30 Kilovolts
breakdown.
• If oil is found to be clean and
uncontaminated (measuring above
15 KV. breakdown), refill the housing.
• If oil is found to be dirty or
contaminated (or measures below
15 KV. breakdown), the pump must
be carefully inspected for leaks at the
shaft seal, cable assembly, square ring
and pipe plug, before refilling with oil. To
locate the leak, perform a pressure test.
After leak is repaired, dispose of old oil
properly, and refill with new oil.
Installation & Service