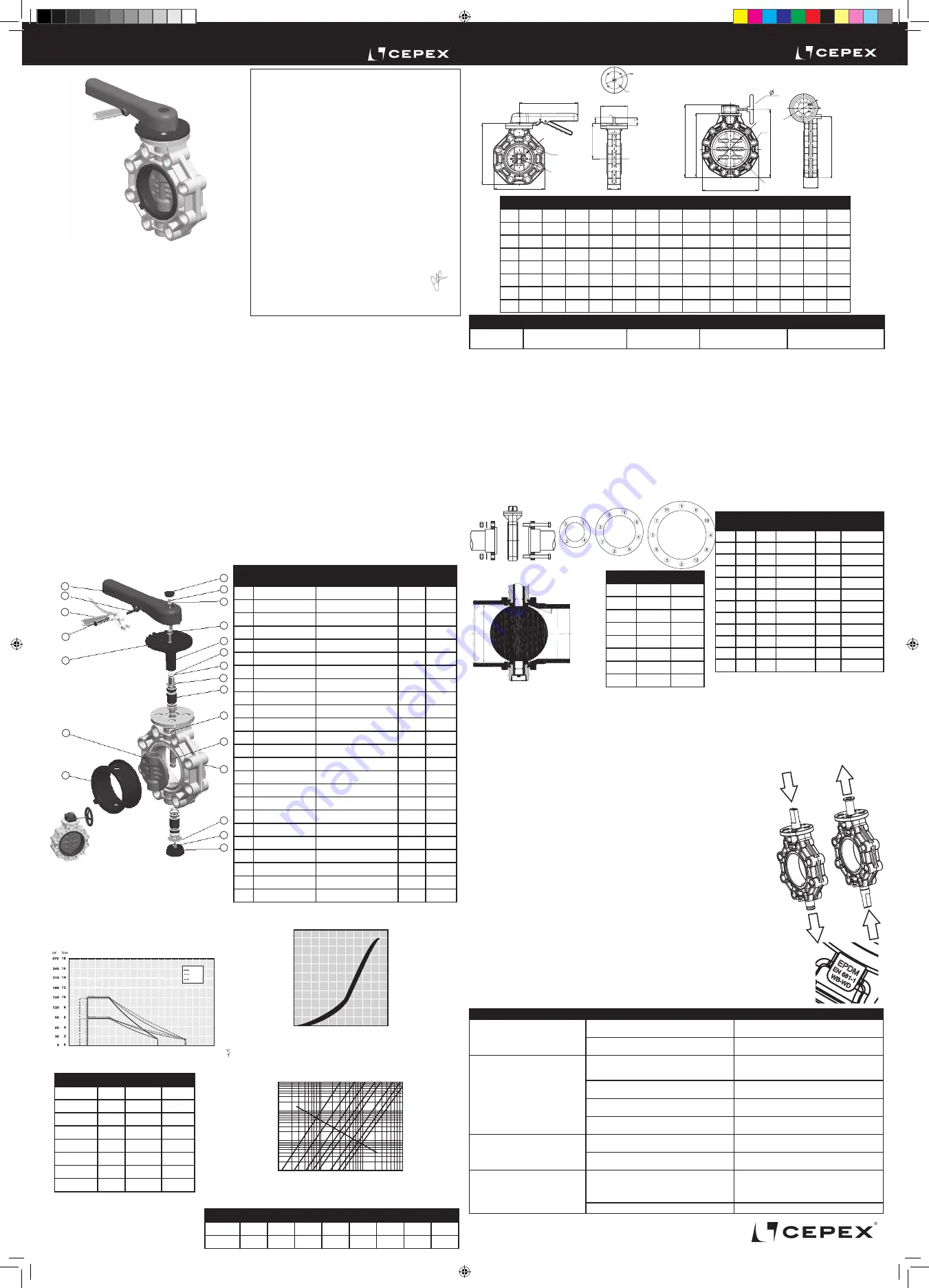
L
A
B
G
S
E
C
H
E
F
K
DN
M
N
1.
DEFINIZIONE
Valvola a farfalla per il sezionamento o la regolazione della mandata nei sistemi di movimentazione dei fluidi. Il fluido può circolare in en-
trambi i sensi. Il modello si basa sulla norma ISO EN 16136 secondo la Direttiva 97/23/CE
La valvola è disponibile con lenti fabbricate in PVC-U, CPVC e in PP e con guarnizioni di EPDM e FPM (FKM). La scelta del materiale della
lente e della guarnizione dipende dal tipo di fluido da trasportare e dalla temperatura di esercizio, come indicato nelle tabelle di resistenza
chimica disponibili sul nostro sito e dal diagramma di pressione / temperatura del presente manuale (G4.1).
2.
AVVERTENZE
•
Leggere le presenti istruzioni prima di manipolare la valvola e seguire le raccomandazioni qui indicate. I danni provocati dalla mancata
osservanza di queste istruzioni non sono coperti da garanzia.
•
Le operazioni di collegamento e manovra dovranno essere svolte da personale qualificato.
•
La massima vita utile della valvola è quella specificata dalla norma EN ISO 16136. Ciò viene verificato nell'impianto di produzione attraver-
so le prove di invecchiamento specificate nella norma.
•
Il raggiungimento della massima vita utile dipende da una corretta installazione e manutenzione della valvola, nonché dall'osservanza
delle condizioni tecniche di pressione e temperatura massima indicate nel presente manuale.
•
Il fluido trasportato deve essere compatibile con i materiali della valvola. Consultare le tabelle di resistenza chimica pubblicate da Cepex
o rivolgersi all'ufficio tecnico.
•
Si sconsiglia l'impiego di utensili per la manovra del comando manuale di apertura e chiusura della valvola. Deve essere effettuata ma-
nualmente.
•
Prima di eseguire qualsiasi operazione di manutenzione sul condotto o sulla valvola, accertarsi che non ci sia pressione nel sistema, libe-
rando la pressione e svuotando i condotti, nel rispetto delle norme di sicurezza specifiche emanate per ogni singolo prodotto.
•
Girare la manopola con la protezione in posizione potrebbe provocare danni alla valvola.
•
Evitare gli urti durante il trasporto, che potrebbero danneggiare il corpo e il meccanismo. Conservare la valvola nel suo imballaggio origi-
nale, al riparo dall'umidità e dall'esposizione diretta alla luce del sole.
•
Prima di installare la valvola, verificare che non abbia subito danni e che contenga tutti gli elementi necessari per l'installazione.
•
Verificare l'ingrassaggio della guarnizione dopo lunghi periodi di inattività e seguire le istruzioni di manutenzione di questo manuale. Il
lubrificante deve essere compatibile con i materiali della valvola.
•
Evitare il colpo d'ariete provocato da una manovra brusca della valvola, che può causare danni all'impianto.
•
Se si utilizza la valvola come fine linea, tenere conto dei rischi generati dal fluido in base alle normative di sicurezza del prodotto e con-
trollare la pressione e la temperatura.
N
DESCRIZIONE
MATERIALE
DN65-
DN200
DN250-
DN300
1
Corpo
PP-GR
1
1
2
Guarnizione
EPDM / FPM
1
1
3
Lente
PVC-U / PP / CPVC
1
1
4
Boccola
PP-GR
2
2
5
Boccola ausiliaria
PP-GR
1
1
6
Asse
AISI-630
1
1
7
Tappo
PP
1
1
8
Anello DIN-471
AISI-304
1
1
9
O-ring
EPDM / FPM
4
8
10
Rondella DIN-6798
AISI-304
1
1
11
O-ring
EPDM / FPM
2
4
12
Vite DIN-912
AISI-304
1
1
13
Manopola
PP-GR
1
-
14
Rondella
AISI-304
1
-
15
Grilletto
POM
1
-
16
Fermo
AISI-304
1
-
17
Divisore
PP-GR
1
-
18
Protezione
POM
1
-
19
Tappo manopola
PP
1
-
20
Vite DIN-912
AISI-304
2
2
21
Dado DIN-934
AISI-304
2
2
22
Vite DIN-912
AISI-304
1
-
23
Riduttore manuale
Scatola di alluminio
-
1
24
Vite DIN-912
AISI-304
-
4
3.
COMPONENTI
Diagramma delle perdite di carica
(G 4.3)
4.
SPECIFICHE TECNICHE
DN65-DN200 (2½”-8”): PN10 (150 psi) a 20 ºC di temperatura del
fluido.
DN250-DN300 (10”-12”): PN6 (90 psi) a 20 ºC di temperatura del
fluido.
La pressione di servizio della valvola diminuisce quando au-
menta la temperatura del fluido, in base ai due grafici riportati.
Coppia massima all'uscita del riduttore manuale = 500 N·m
(Riduzione = 37:1).
Diagramma di Pressione / Temperatura.
(G 4.1)
D
DN
Kv (l/min)
Cv (GPM)
63-75 (2 1/2”)
DN65
1800
126
90 (3”)
DN80
4020
282
110 (4”)
DN100
8280
580
125-140 (5”)
DN125
11760
826
160 (6”)
DN150
16200
1134
200-225 (8”)
DN200
33000
2311
250 (10”)
DN250
5200
3655
315 (12”)
DN300
78571
5502
Tabella delle perdite di carica
(T4.1)
5.
DIMENSIONI.
6.
INSTALLAZIONE E MESSA IN FUNZIONE
Prima di iniziare l'installazione della valvola, verificare che si dispone di tutti gli elementi necessari per il montaggio e che i materiali, il tipo
di collegamento e la pressione nominale siano adeguati all'impianto. In caso di unione tramite incollatura o saldatura, assicurarsi anche che
i materiali da unire siano uguali e che la colla o gli utensili di saldatura siano appropriati.
Per il fissaggio della valvola, seguire le norme di buona pratica di installazione esposte sul sito di Cepex, con particolare attenzione alla
dilatazione termica e all'allineamento dei tubi.
Quando è ora di riempire le tubazioni con il fluido da trasportare, verificare che venga spurgata tutta l'aria dall'impianto e che la pressione
iniziale non superi la PN della valvola o dell'elemento a minore pressione nominale dell'impianto.
Montaggio della valvola mediante flange normalizzate ISO-DIN, ANSI, JIS e BS/E.
Nell'accoppiamento non sono necessarie le guarnizioni
piane per i manicott
i, poiché sono già incorporate nella valvola. Rispettare l'ordine di serraggio (Fig. 5) delle viti nelle flange e la coppia
massima di serraggio. È imprescindibile installare tutte le viti per assicurare il corretto funzionamento della valvola.
I manicotti di PP / PE di saldatura testa a testa devono essere smussati in base allo schema (fig. 6) e alla tabella T6.2 per garantire una corretta
chiusura e apertura della lente.
Installare la valvola dopo che i manicotti di raccordo sono incollati e asciutti, per evitare problemi con l'adesivo (penetrazione dell'adesivo
nella valvola).
Le flange devono essere ben centrate nella valvola (fare attenzione soprattutto alle misure DN100-DN125 e DN200). Il disallineamento del
gruppo potrebbe provocare problemi nel funzionamento della valvola.
T 5.1
(mm)
7.
ISTRUZIONI DI ESERCIZIO E MANUTENZIONE
Si consiglia di controllare periodicamente lo stato della guarnizione, giacché avviene un'usura meccanica dovuta alle pressioni, alla
manipolazione e al contatto con il fluido. Si consiglia di lubrificare la guarnizione nella zona di contatto con la lente (con grasso compatibile
ai materiali della guarnizione e della lente). Si raccomanda inoltre di controllare periodicamente il serraggio dei dadi di fissaggio delle bride,
sulla base della coppia raccomandata in precedenza in questo manuale (T6.1).
Durante i lunghi periodi di inattività, e ogni volta che l'impianto lo permette, mantenere la valvola leggermente aperta.
Il riduttore manuale è esente da manutenzione e lubrificato a vita.
Per azionare la valvola, sbloccare la manopola (13) estraendo il fermo (16) e premendo la leva (15) verso l'alto, liberando i denti dal divisore
(17) e girando la manopola nel verso desiderato.
Per bloccare la valvola, collocare il fermo (16) e, se lo si desidera, inserire il lucchetto di sicurezza.
7.2 Montaggio e smontaggio della manopola
Montaggio della manopola:
• Montare la manopola nel perno mentre il grilletto viene mantenuto premuto. Orientarla in modo che,
mentre la valvola è chiusa, l'indicatore della manopola indichi 90º nel divisore (17)
Montare la rondella (14), la vite (22) e il tappo (19).
Smontaggio della manopola:
• Estrarre il tappo (19) dalla manopola, la vite (22) e la rondella (14).
• Premere il grilletto (15) al massimo verso l'alto in modo da liberare con i denti i denti del divisore (17)
ed estrarre la manopola dell'asse (6).
9.
GUIDA AI PROBLEMI PIÙ COMUNI
T 9.1
Temperatura
DN
65
(2
)
½”
0,1
0,001
m
3
/s
bar
0,01
0,001
1
0,01
0,1
1
2,12
ft
3
/min
21,19
211,90
2.119
1,5
0,15
0,015
15
psi
Pressure loss /
P
er
te de charge / Pérdida de carga
DN
80
(3”)
DN
100
(4”)
DN
125
(5”)
DN
150
(6”)
DN
200
(8”)
DN
250
(10”)
V=2m/s
DN
300
(12”)
Flow / Débit / Caudal
DN
A
B
C
E
F
G
H
K
L
M
N
E’
S
FORI
65
201
156
120
40
18
112
48
125-145
220
70
9
35
10
4
80
232
190
136
40
19
112
52
150-170
245
70
9
35
12
8
100
255
212
148
40
19
112
59
180-192
245
70
9
35
16
8
125
284
238
164
40
22
112
66
190-215
320
70
9
35
20
8
150
314
265
180
40
24
112
72
240
320
70
9
35
20
8
200
378
320
217
50
23
136
73
270-298
391
102
11
47
26
8
250
450
453
310
525
29
488
114
329-355
-
-
-
57
18
12
300
545
477
310
616
29
578
114
384-427
-
-
-
57
18
12
C
G
B
DN
A
E
K
F
A
E
H
D
DN
pol-
lice
Viti (A2)
Coppia
(N·m)
Coppia
(pollice·libbra)
63
65
-
4xM16x120
25
221
75
65
2 1/2” 4xM16x140
25
221
90
80
3”
8xM16x150
25
221
110
100
4”
8xM16x160
30
265
125
125
-
8xM16x170
35
310
140
125
5”
8xM16x170
35
310
160
150
6”
8xM20x200
40
354
200
200
-
8xM20x210
50
442
225
200
8”
8xM20x230
50
442
250
250
-
12xM20x270
80
708
280
250
10”
12xM20x270
80
708
315
300
12”
12xM20x310
80
708
Viti e coppia di serraggio delle viti
7.1 Istruzioni per la sostituzione della guarnizione della lente
N
el caso in cui si renda necessario sostituire la guarnizione della valvola, procedere nel seguente modo:
•
Accertarsi che non ci sia pressione nel sistema, liberando la pressione e svuotando i condotti nel
rispetto delle norme specifiche di sicurezza emanate per ogni singolo prodotto. Controllare anche la
temperatura del fluido e seguire le norme di sicurezza.
• Smontare la valvola dall'impianto.
• Estrarre la manopola secondo quanto riportato nel 7.2, le viti (20), i dadi (21) e il divisore (17).
• Togliere l'anello elastico (8). Rimuovere il tappo (7) e togliere la vite (12).
• Percuotere sopra il perno (6) con una mazza di nylon fino all'uscita della boccola (4) dalla zona inferiore (Fig.7).
• Con la boccola rimossa, togliere il perno (6) girarlo e reintrodurlo (Fig.8) dal basso.
• Percuotere di nuovo fino all'uscita delle boccole (4 e 5) da sopra. Rimuovere di nuovo il perno.
• Estrarre la lente premendo in direzione del fluido.
• Estrarre la guarnizione. Montare la nuova guarnizione; deve entrare deformata e va collocata in
modo da centrarla con il perno, utilizzando il bordino di indicazione del materiale (fig. 9).
ATTENZIONE: controllare lo stato degli O-ring (9 e 11) prima di montare la nuova guarnizione.
DN
D min.
x
65
50.5
30º
80
70
30º
100
91.5
30º
125
113
30º
150
141
30º
200
191.5
20º
250
226
20º
300
296.5
20º
(T3.1)
T 6.1
T 6.2
PROBLEMA
CAUSA
SOLUZIONE
La lente non si apre o chiude
completamente.
I manicotti non sono stati smussati correttamente.
Smontare la valvola e smussare i manicotti in base a
T6.2. Verificare lo stato della lente.
Elementi estranei nel compartimento (adesivo, ecc.).
Smontare la valvola e controllare eventuali ostruzioni
nella zona di contatto della lente con la guarnizione.
Eccessiva coppia di apertura o chiusura.
La valvola è rimasta inattiva troppo tempo.
Messa in servizio con una chiave ausiliare (non la
manopola).
Smontare la valvola e lubrificare la guarnizione.
Deterioramento della guarnizione per eccesso di
temperatura o per aggressione chimica.
Verificare la compatibilità chimica del fluido con la lente
e la temperatura di esercizio. Sostituire la guarnizione.
Coppia di giunzione eccessiva.
Effettuare la giunzione secondo quanto riportato nel
paragrafo 6.
Disallineamento tra manicotti e valvola.
Smontare la valvola e rimontare con allineamento
concentrico (rispettare l'ordine e la coppia di serraggio).
La valvola non presenta una perfetta
tenuta stagna nei manicotti di raccordo.
Disallineamento tra manicotti e valvola.
Smontare la valvola e rimontare con allineamento
concentrico (rispettare l'ordine e la coppia di serraggio).
Mancanza di serraggio delle viti flangiate.
Effettuare la giunzione secondo quanto riportato nel
paragrafo 6.
La valvola non presenta una perfetta
tenuta stagna nella guarnizione.
Elementi chimici inadatti.
Temperatura al di fuori dei limiti consentiti.
Eccesso di pressione.
Trasporto di elementi abrasivi.
Verificare il rispetto delle caratteristiche tecniche di
questo documento.
Guarnizione danneggiata.
Sostituire la guarnizione.
Coppia di manovra della valvola
.
Valori della coppia di manovra a PN e 20 ºC nelle
condizioni di uscita dalla fabbrica. Le condizioni di
installazione (serraggio delle flange) e di servizio
(pressione e temperatura) possono cambiare que-
sti valori. Nel caso in cui sia necessaria l'automazio-
ne della manovra, consultare il fabbricante.
(T4.3)
Tabella della coppia di manovra
Fig. 1
Fig. 2
Fig. 3
Fig. 4
Fig. 5
Fig. 6
Fig. 7
Fig. 8
ITALIANO
VALVOLA A FARFALLA INDUSTRIALE
ITALIANO
VALVOLA A FARFALLA INDUSTRIALE
VALVOLA A FARFALLA INDUSTRIALE
PVC-U (EPDM/FPM)
CPVC (EPDM/FPM)
PPH (EPDM/FPM)
DN65-200
DN250-300
Disegno della valvola Dimensioni giunzione
Connessioni per valvole
Altre connessioni
Accoppiamento attuatore (a scelta)
ISO 16136: 2005
EN 558-1, ANSI B16.5 Classe 150,
JIS B2220, BS/E
EN 1090-1
ISO15494, ISO15493, ISO10931
EN/ISO 5211
Misure del
tubo e de-
gli smussi
Pr
essione
PVC-U
0
10
20
30
40
50
60
70
80
90
100
32
50
68
86
104
122
140
158
176
194
212
PVC-C
PP-H
ã
DN63-DN200
DN250-DN315
DN65
DN80
DN100
DN125
DN150
DN200
DN250
DN300
N·m
25
28
35
85
110
110
180
250
libbra·pollice
221
248
310
752
974
974
1593
2213
Manicotti PP/PE
10 20 30 40 50 60 70 80 90 100
Kv
100
90
80
70
60
50
40
30
20
10
0
%
% opening / % d’ouverture / % de apertura /
% di apertura / % Öffnung / % de abertura
Kv / Coefficiente di flusso.
(G 4.2)
Dmin
Dmin
Fig. 9
Dichiarazione CE di conformità /
EC Declaration of Conformity
Il fabbricante /
the manufacturer
: CEPEX S.A.U.
Avinguda Ramon Ciurans 40 ( Parcel.la 6) - P. I. Congost
08530 LA GARRIGA
Dichiara che le nuove valvole /
declares that our valves
:
Tipo /
Type
: Valvole a farfalla /
Butterfly valves
Modelli /
Models
:
UP.84.SS.FGEP, UP.84.SS.VI, UP.84.SS.FGEP.RM, UP.84.SS.VI.RM, CP.84.SS.FGEP, CP.84.
SS.VI, CP.84.SS.FGEP.RM, CP.84.SS.VI.RM, PPH.84.SS.FGEP, PPH.84.SS.VI, PPH.84.
SS.FGEP.RM, PPH.84.SS.VI.RM.
Soddisfano i requisiti stabiliti nell'Unione Europea per gli APPARECCHI A PRES-
SIONE secondo la direttiva PED 97/23/CE, categoria II modulo A1, conforme-
mente alle norme armonizzate:
- EN ISO 16136 VALVOLE INDUSTRIALI: Valvole a farfalla di materiali termoplastici.
Meets the requirements established by the European Union for PRESSURE EQUIP-
MENT according to Directive 97/23/EC (PED), category II module A1, in accordance
with the harmonized standards:
- EN ISO 16135 INDUSTRIAL VALVES: Butterfly valves of thermoplastic materials.
La marcatura CE sulla valvola indica la conformità alla normativa. Secondo la
direttiva 97/23/CE solo le valvole di diametri superiori a DN25 possono recare la
marcatura CE.
The CE marking on the valve refers to this conformity. According to Directive 97/23/EC
only valves larger than DN25 can be marked with CE.
Direttore di Qualità /
Quality Director
:
Yasmin Fernández
La Garriga, Marzo 2014
Supervisione della valutazione finale: TÜV Nord (CE 0045).
Monitoring of final assessment: TÜV Nord (CE 0045).
x
13
16
15
18
17
3
2
19
22
14
20
5
8
11
9
4
21
6
1
10
12
7
Manual VP Industrial 2014_IT_PT.indd 1
15/10/2014 10:19:27