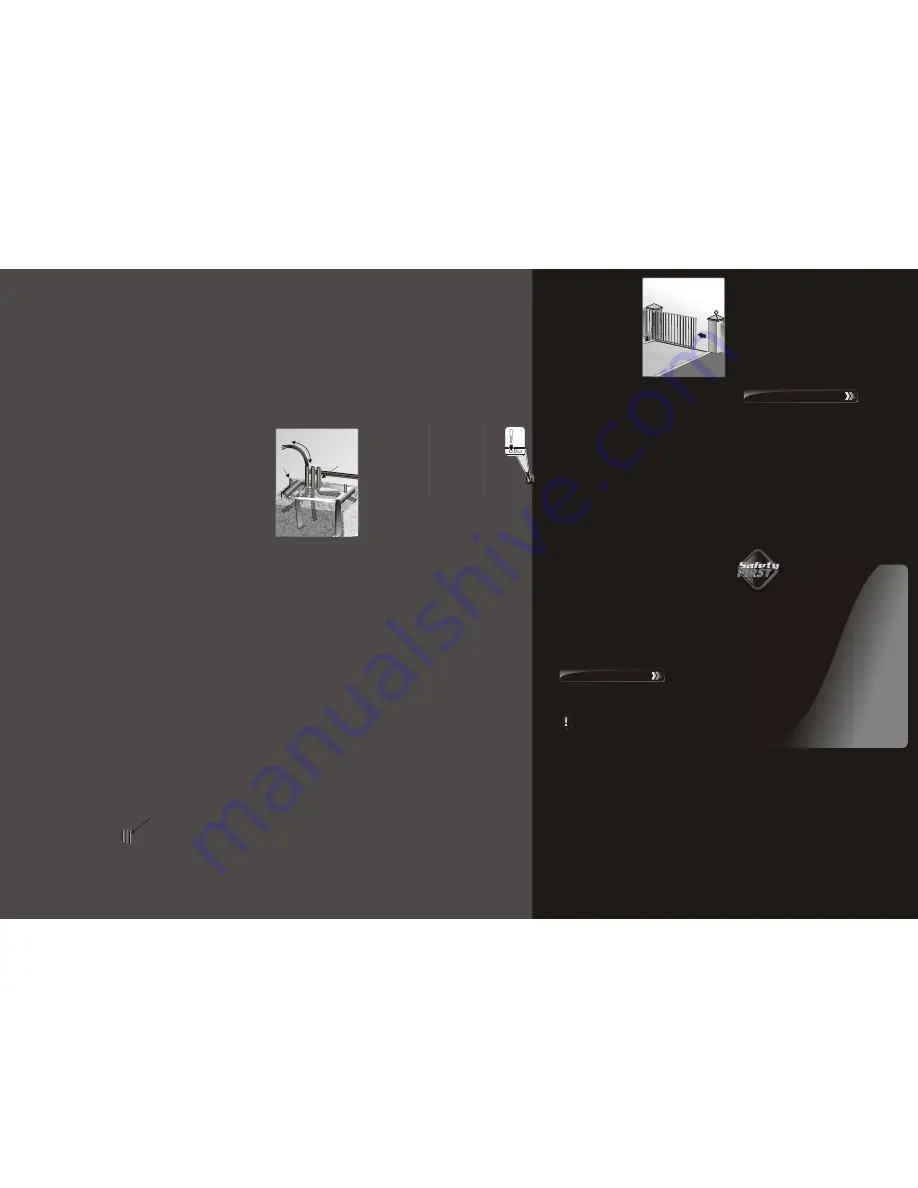
C: Above pinion - Nylon angle rack
Foundation
plate
40 - 50
92
147*
Flat bar welded to
foundation plate and rail
* Includes 3mm clearance required
between rack and pinion
(Recommended to
allow for adjustment)
5
B: Above pinion - Steel rack
5
Foundation
plate
43 - 53
92
156*
(Recommended to
allow for adjustment)
Flat bar welded to
foundation plate and rail
* Includes 3mm clearance required
between rack and pinion
250mm
Cable conduits
Gate rail
200mm
M10
gearbox
mounting
bolts
400mm
Mount the rack
The rack must be securely
mounted to the side of the
gate. It must be parallel
with the gate rail, and
there must be a 2 - 3mm
gap between the teeth of
the pinion and the rack,
along the entire travel of
the gate
Route cables and secure foundation plate
The foundation plate can either be set into a concrete foundation, or
bolted down onto an existing concrete plinth, refer to illustrations
below.
Foundation plate installation
Mounting the
origin marker
1.
Close the gate completely.
2.
Mount the origin marker to
the rack a minimum of
500mm from the origin
sensor.
1.
Route cables as determined
in Section 9: Cabling
requirements.
2.
The cable conduits or
SWA cable glands should
terminate onto the cable
termination flange provided
in the foundation plate, as
depicted in the illustration
3.
Make sure that all cables
protrude at least 500mm
from the cable termination
flange.
3.
Adjust jacking screws to give
4-6 mm chassis foundation
plate clearance.
A 4mm Allen key with
“ball end” is handy
1.
Insert M8 captive nuts for the
jacking screws as shown.
2.
Screw the M8 grub screw
jacking screws into the
captive nuts.
Make sure that the M10
bolts, which secure the
gearbox, are in place
If bolting the foundation
plate, the left-hand
concrete anchor may need
to be broken off in order to
clear incoming conduits
3mm
tooth gap
M8 captive nuts
Jacking
Screw
4-6mm
Ensure that all the standard considerations for a quality
gate installation are adhered to as detailed in
CENTSYS’ detailed installation manuals.
These must include:
11. D10/D10 Turbo operator installation
&
Correct access in and out of the premises
&
Endstops are mandatory and must be capable of stopping the
gate at rated speed
&
Guide-rollers and anti-lift brackets are correctly fitted
&
The gate mass, starting- and rated-pull-force limitations are not
exceeded
&
The
D10/D10 Turbo
is positioned correctly and does not
protrude into the driveway
If bolting onto an existing
concrete plinth, place the
foundation plate down in the
correct position and use the plate
as a template for marking the
rawl bolt holes.
Ensure that the M10
gearbox mounting bolts
are properly tightened
Bolting foundation
plate onto an existing
concrete plinth
250mm
200mm
M10
gearbox
mounting
bolts
400mm
Existing
concrete
plinth
Option 2:
Option 1:
New concrete foundation
When using a concrete foundation
it is recommended that the
foundation plate is welded to the
rail/track of the gate using a short
length of flat bar as shown in the
illustration. This makes it possible
to complete the whole mechanical
and electrical installation without
having to wait for the concrete to
set. After completing the
installation the concrete can be
poured and the operator left in
manual mode until the concrete
has set.
• Ensure that the M10 gearbox mounting bolts are properly
tightened
• Cable conduits must be installed before pouring the concrete
3.
For steel rack mount the
origin marker onto the rack
using the bracket provided.
4.
Weld the bracket to the
rack.
5.
Bolt the origin marker onto
the bracket using the
fasteners provided.
Steel rack
6.
With RAZ rack the origin
marker mounts directly on
top of the rack without a
bracket.
7.
Drill mounting holes
directly into the rack and
bolt into position.
8.
File away the front lip of
the rack if you need to
move the origin marker
closer to the operator as
the gate slides past.
RAZ rack
9.
With nylon angle rack it is
necessary to use the
bracket provided.
10. It is preferable to use self-
tapping fasteners to secure
the bracket into the side of
the nylon rack as shown.
11. Make a small tack weld to
secure the back of the
bracket onto the angle iron
section of the rack.
12. Bolt the origin marker onto
the bracket using the
fasteners provided.
Nylon angle rack
Bolt using
fasteners
provided
Origin marker
bracket
Screw into
side of the
nylon rack
Nylon angle rack
RAZ rack
Bolt using
fasteners
provided
Origin marker
bracket
Weld mounting
bracket provided to
steel rack
Steel rack
Bolt using
fasteners
provided
A: Above pinion - Raz rack
5
Foundation
plate
40 - 50
92
147*
(Recommended to
allow for adjustment)
Flat bar welded to
foundation plate and rail
Greater than 500mm
Gate in
closed
position
Origin
marker
Origin
sensor
Plan view
Mounting the origin
marker (continued)
Apply warning decal/signage
Apply the supplied Warning! decals/signage to the gate
13. Manually slide the gate
OPEN until the origin
marker is in line with the
origin sensor.
It is possible to make the distance between the marker and the
sensor much greater than 500mm. However, if using the
pedestrian opening facility, although the position of the marker
will not affect the width of the pedestrian opening, it is
preferable to have the marker mounted inside of the pedestrian
opening point
14. Ensure distance between
face of marker and front
face of sensor is between
13 and 20mm.
Take care with the
orientation of the arrow on
the origin marker. This
arrow must face the
operator
15. Adjust distance by sliding
the origin marker along the
slotted mounting holes
until the specified distance
is achieved.
For best results keep gap
between marker and
sensor as small as
possible
Isometric view
Greater than 500mm
A10
A10
Origin
sensor
Origin
marker
13-20mm
Gate
Rack
Plan view
1.
To ensure operator does not
protrude into driveway, install
base plate at least flush with
the driveway entrance.
2.
Determine a suitable position
and vertical height for the
operator by considering
Figures A, B and C.
Locate operator position
Steel rack
1.
Fix rack using the steel angle
brackets provided.
2.
Brackets must be spaced no
more than 300mm apart.
3.
When joining different
lengths of steel rack, a
simple way of ensuring
correct pitch spacing, is to
clamp a small off-cut
between the two pieces.
RAZ rack
1.
Use at least three TEK screws per half metre section of rack.
Fit additional fixing screw through the horizontal slots to secure
the rack to the gate directly above the pinion when the gate is
in the closed, pedestrian and open positions
±300mm
±300mm
Gate
closed
Pedestrian
opening
Gate
open
D5
Gate closed
Pedestrian
Gate open
Cable
termination
flange
M10
mounting
bolts
500mm
Once the installation has been successfully completed and tested, it is
important for the installer to explain the operation and safety
requirements of the system.
NEVER ASSUME THE USER KNOWS HOW TO SAFELY OPERATE
AN AUTOMATED GATE!
Even if the user has used one before, it does not mean he knows how
to SAFELY operate it. Make sure that the user fully understands the
following safety requirements before finally handing over the site.
The following needs to be understood by the user:
How to operate the manual release mechanism.
(Show them how by demonstration)
How the obstruction detection and all other safety features work.
(Show them how by demonstration)
All the features and benefits of the operator, i.e. safety beams,
Chronoguard, etc.
All the safety considerations associated with operating an
automated gate. The user should be able to pass this
knowledge on to all other users of the automated system
and must be made aware of this responsibility.
&
&
&
&
&
Do not activate the gate operator unless
you can see it and can determine that its
area of travel is clear of people, pets, or
other obstructions
&
NO ONE MAY CROSS THE PATH OF A
MOVING GATE. Always keep people and objects away
from the gate and its area of travel
&
NEVER LET CHILDREN OPERATE OR PLAY WITH THE
GATE CONTROLS, and do not allow children or pets near
the gate area
&
Be careful with moving parts and avoid close proximity
to areas where fingers or hands could be pinched
&
Secure all easily accessed gate operator controls in
order to prevent unauthorized use of the gate
&
Keep the automated gate system properly maintained,
and ensure that all working areas are free of debris and
other objects that could affect the gate operation and
safety
&
On a monthly basis, check the obstruction detection
system and safety devices for correct operation
&
All repair and service work to this product must be done
by a suitably qualified person
&
This product was designed and built strictly for the use
indicated in this documentation. Any other use, not
expressly indicated here, could compromise the good
condition/operation of the product and/or be a source
of danger!
Centurion Systems (Pty) Ltd does not accept any liability caused by
improper use, of the product, or for use other than that for which the
automated system was designed.
Ensure that the customer is in possession of the User Guide and
that you have completed the installation details in the back of
the User Guide.
CENTSYS operators are designed to be maintenance-free. However,
there are some basic checks that should be carried out regularly,
(every six months). These checks will increase the long term reliability
of the system and prevent erratic operation of your gate.
Isolate mains supply as well as disconnecting the
battery before cleaning or working on the equipment.
General
&
Keep the track clear of stones, dirt and obstructions
&
Ensure that all rollers run freely
&
Put the operator into Manual Mode and check that the gate runs
freely on its rail and does not catch or foul against the walls or
pillars
&
Ensure that the gate wheels and guide-rollers are rotating freely
and are not worn. In high-volume applications it will be necessary
to replace these components regularly
&
Ensure that the rack is properly secured to the gate and that it
does not press down onto the operator pinion at any point along
its travel
&
Keep shrubs and vegetation clear of the motor and rack
&
Check that the key still operates the camlock - spray with
lubrication if necessary
&
Keep the inside of the motor housing clear of insects and dust
Battery
CENTSYS operators, which are fitted with maintenance-free lead acid
batteries, should provide at least three years of normal service life.
For sites utilising an external large capacity (+/-35Ah) low
maintenance battery, ensure that the level of liquid (electrolyte level)
is correct.
In all instances check for corrosion of the battery terminals. Clean and
apply copper based grease as necessary.
12. Basic maintenance
Charger
The
D10
and
D10 Turbo
operators have chargers separate to the
main controller. In the case of product malfunction, the charger fuse
should be checked, but only by a qualified electrician. Always isolate
the mains supply to the operator before attempting to remove and
check the fuse.
Check the “Mains Present” icon on the main diagnostic screen or
switch to the battery charger diagnostic screen and check the charger
voltage – right hand value. This should indicate, 27.6V for the
D10
and
D10 Turbo.
Each charger has a red light (LED) to indicate mains
supply.
Gearbox Oil Level
Check the oil level as described in section 8 of this document or refer
to the online manuals on our website,
(www.centsys.com.au).
Alternatively, please contact your CENTSYS installer for assistance.
13. Installation handover
A10
A10
* Includes 3mm clearance required
between rack and pinion