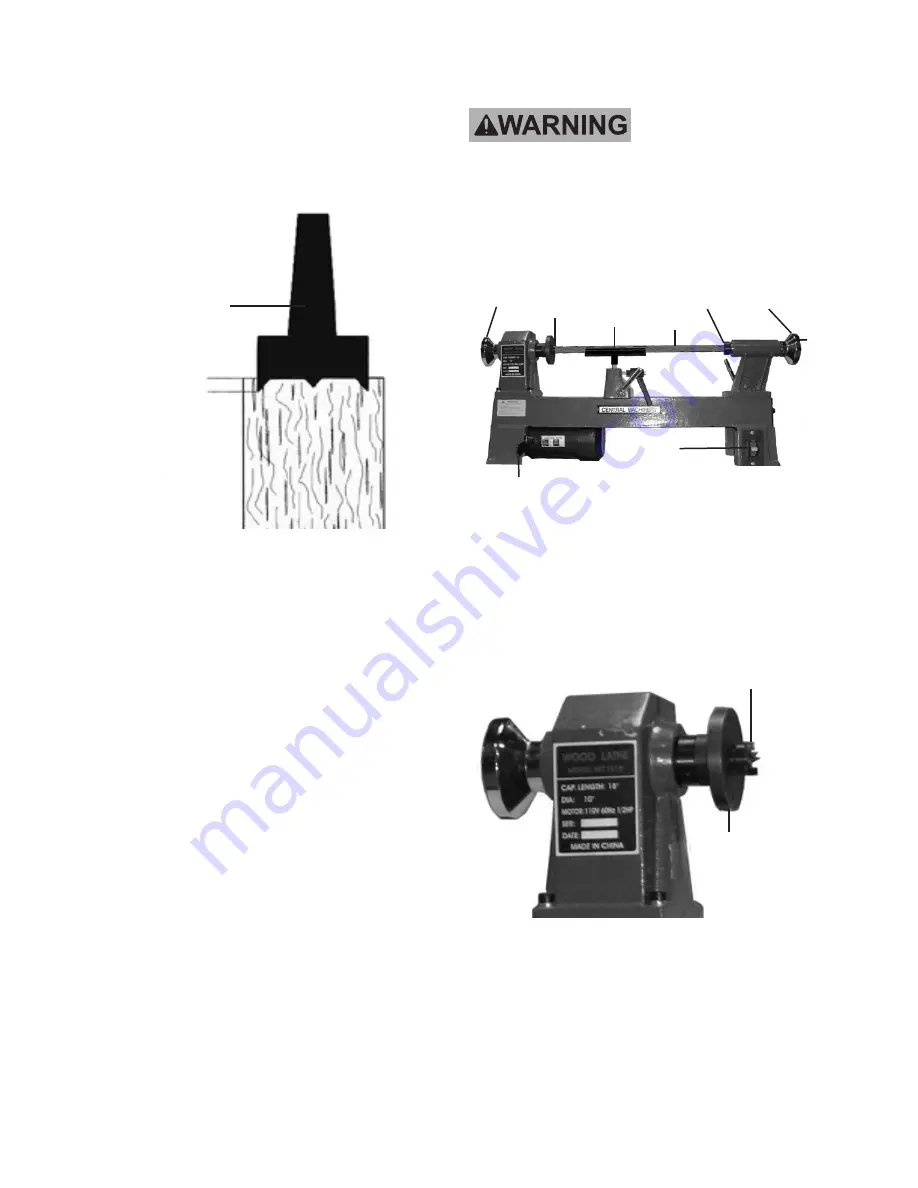
Page 16
SKU 65345
For technical questions, please call 1-800-444-3353.
Use a wood mallet to drive the Head-
6.
stock Spur Center (12) into the center
of the workpiece at least 1/4” deep.
(See Figure Q.)
FIgurE Q
1/4”
WOrKpIEcE
HEADSTOcK
Spur
cENTEr
(12)
7. With the workpiece still attached, in-
sert the Headstock Spur Center (12)
into the Headstock Spindle (14).
(See Figure r.)
With the Cup Center (11) installed in
8.
the Tailstock (5), slide the Tailstock
toward the workpiece until the Cup
Center touches the workpiece center
point. The lock the Tailstock in posi-
tion.
(See Figure r.)
Use the Tailstock Handwheel (4) to
9.
push the Cup Center (11) into the
workpiece at least 1/4”.
(See Figure r.)
Position the Tool Rest (35) approxi-
10.
mately 1/4” away from the workpiece
and approximately 1/8” above the
center line.
(See Figure r.)
Make sure to test the set up by hand
11.
turning the workpiece to ensure there
is enough clearance all the way
around before starting.
Do not press the
workpiece too firmly
with the Tailstock (5) or the bearings will
bind and overheat. Also, do not leave the
workpiece too loose or the workpiece will
spin off the Lathe.
(See Figure r.)
FIgurE r
TAILSTOcK
HANDWHEEL
(5)
cup
cENTEr
(11)
WOrKpIEcE
TOOL
rEST
(35)
HEADSTOcK
Spur
cENTEr
(12)
pOWEr
SWITcH
(46)
BALANcE
WHEEL
(22)
BELT
TENSION
LEVEr
(31)
To set up a faceplate turning op-
12.
eration
, remove the Headstock Spur
Center (12) from the Faceplate (13).
(See Figure S.)
FIgurE S
HEADSTOcK
Spur cENTEr
(12)
FAcEpLATE
(13)
13. Find the center of the workpiece in
the same way as when spindle turn-
ing.
Cut off the corners of the workpiece.
14.