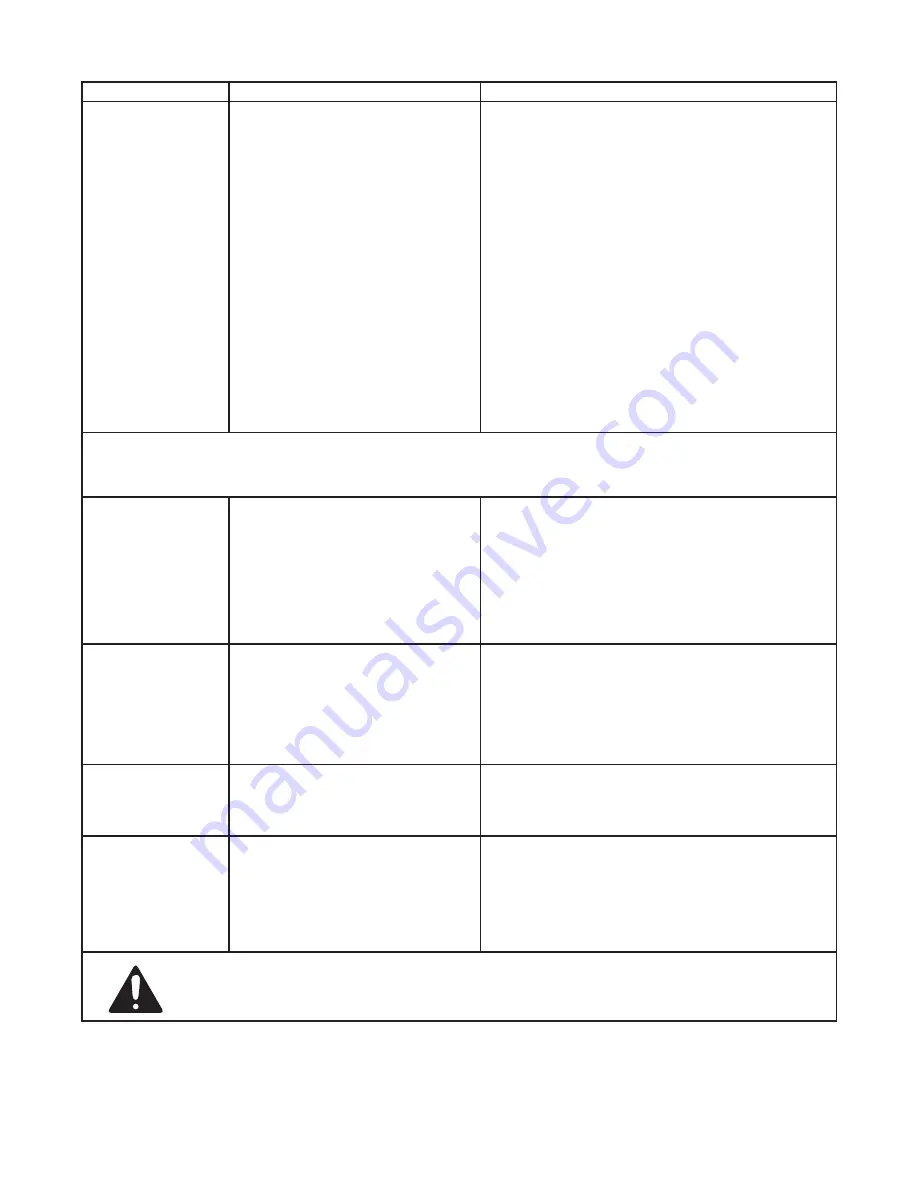
Page 30
For technical questions, please call 1-800-444-3353.
SKU 93212
Problem
Possible causes
Likely solutions
Overheating.
Motor overloaded.
1.
Forcing machine to work too fast.
2.
Accessory dull or damaged.
3.
Incorrect RPM or feed rate.
4.
Gear setup is too tight, gears
5.
bind.
Blocked motor housing vents.
6.
Motor being strained by long or
7.
small diameter extension cord.
Reduce load on motor. Loosen drive Belt (see
1.
Maintenance section of this manual).
Allow machine to work at its own rate.
2.
Keep cutting accessories sharp. Replace as
3.
needed.
Check that RPM feed rate chart for appropriate
4.
rates for operation.
Adjust gears so there is a small amount of play
5.
and the gears move freely and smoothly when
the Chuck is rotated by hand.
Wear ANSI-approved safety goggles and NIOSH-
6.
approved dust mask/respirator while blowing dust
out of motor using compressed air.
Eliminate use of extension cord. If an extension
7.
cord is needed, use one with the proper diameter
for its length and load. See
Extension Cords
in
GROUNDING
section.
tool Performance
Whole unit vibrates
excessively while in
use.
Workpiece unbalanced.
1.
Loose or damaged belt(s).
2.
Drive Pulleys not aligned.
3.
Worn or broken gear.
4.
Chuck loose or unbalanced.
5.
Spindle bearings worn.
6.
Re-center workpiece.
1.
Tighten or replace the belt.
2.
Align Drive Pulleys (27, 148).
3.
Inspect gears and replace if needed.
4.
Tighten Nuts (6) or have a qualified technician
5.
rebalance Chuck.
Have a qualified technician replace bearings.
6.
Uneven surface
finish.
Incorrect RPM or feed rate for
1.
job.
Dull or incorrect tool for job.
2.
Gibs need adjustment.
3.
Tool positioned too high.
4.
Adjust RPM and/or feed rate.
1.
Sharpen and/or change tool.
2.
Tighten Gibs (99 and/or 106) (See Gib
3.
Adjustment in Maintenance Section).
Lower position of tool.
4.
Unable to remove
tapered tool from
Tailstock.
Quill not fully seated in Tailstock
or taper was inserted without first
removing debris.
Turn quill handwheel until taper is forced out of quill.
In the future make sure that the quill is fully seated
in the tailstock and that the tool is wiped free of
debris before installing.
Cross Slide,
Compound Slide
and/or carriage
feed do not move
smoothly.
Gibs need adjusting.
1.
Handwheel or crank handles are
2.
too loose.
Leadscrew worn or needs
3.
adjustment.
Loosen or tighten the Gib screws (99 and/or 106)
1.
(See Gib Adjustment in Maintenance Section).
Tighten Handwheel and/or crank handle.
2.
Tighten Leadscrew fasteners or have lead screw
3.
replaced by a qualified technician.
Follow all safety precautions whenever diagnosing or servicing the tool.
disconnect power supply before service.
reV 10b