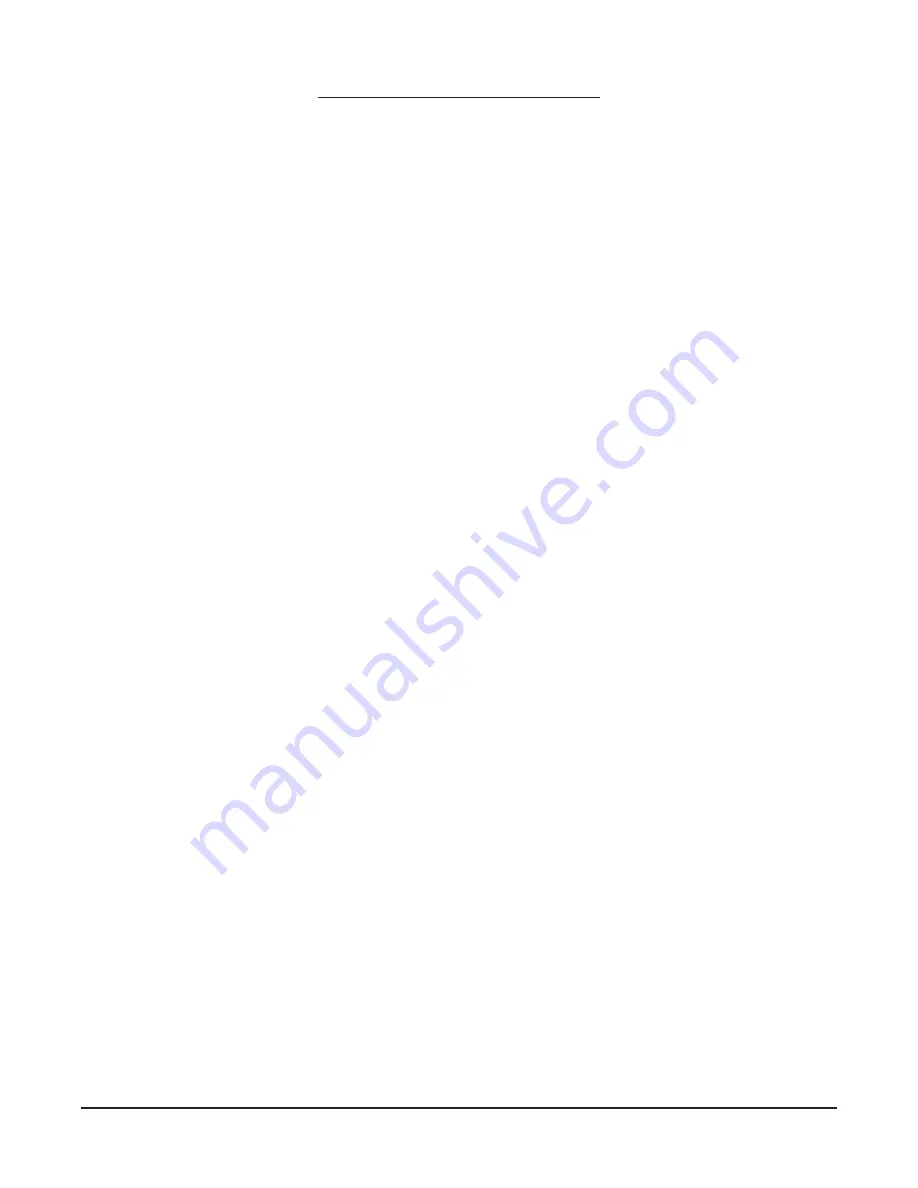
SAFETY WARNING & CAUTIONS
READ ALL INSTRUCTIONS BEFORE USING THIS TOOL!
1. KEEP WORK AREA CLEAN. Cluttered areas invite injuries.
2. OBSERVE WORK AREA CONDITIONS. Do not use tools in damp, wet, or poorly lit locations.
Don’t expose to rain. Keep work area well lit. Do not use electrically powered equipment in the presence
of flammable gases or liquids.
3. KEEP CHILDREN AWAY. Children must never be allowed in the work area. Do not let them handle
machines, tools, or equipment.
4. STORE IDLE EQUIPMENT. When not in use, tools must be locked up in a dry location to inhibit
rust. Always lock up tools and keep out of reach of children.
5. DO NOT FORCE THE TOOL. It will do the job better and more safely at the rate for which it was
intended. Do not use inappropriate attachments in an attempt to exceed the tool’s capacities.
6. USE THE RIGHT TOOL FOR THE JOB. Do not use a tool for a purpose for which it was not
intended.
7. DRESS PROPERLY. Do not wear loose clothing or jewelry, as they can be caught in moving parts. Non-
skid footwear is recommended. Wear restrictive hair covering to contain long hair. Always wear appropriate
work clothing.
8. USE EYE, EAR AND BREATHING PROTECTION. Always wear ANSI approved impact safety
goggles if you are producing metal filings or wood chips. Wear an ANSI approved dust mask or
respirator when working around metal, wood, and chemical dusts and mists. Use ANSI approved ear
protection when working in a loud or noisy environment.
9. DO NOT ABUSE THE POWER CORD. Protect the power cord from damage, either from impacts,
pulling or corrosive materials. Do not yank machine’s cord to disconnect it from the receptacle.
10. DO NOT OVERREACH. Keep proper footing and balance at all times. Do not reach over or across
running machines.
11. MAINTAIN TOOLS WITH CARE. Keep tools sharp and clean for better and safer performance.
Follow instructions for lubricating and changing accessories. Inspect power cord periodically and, if
damaged, have it repaired by an authorized technician. Inspect all hydraulic seals for leaks prior to use.
Control handle and power switch must be kept clean, dry, and free from oil and grease at all times.
12. REMOVE ADJUSTING KEYS AND WRENCHES. Be sure that keys and adjusting wrenches are
removed from the tool or machine work surface before operation.
13. AVOID UNINTENTIONAL STARTING. Be sure that you are prepared to begin work before turning the
start switch on.
Page 3 SKU # 42827