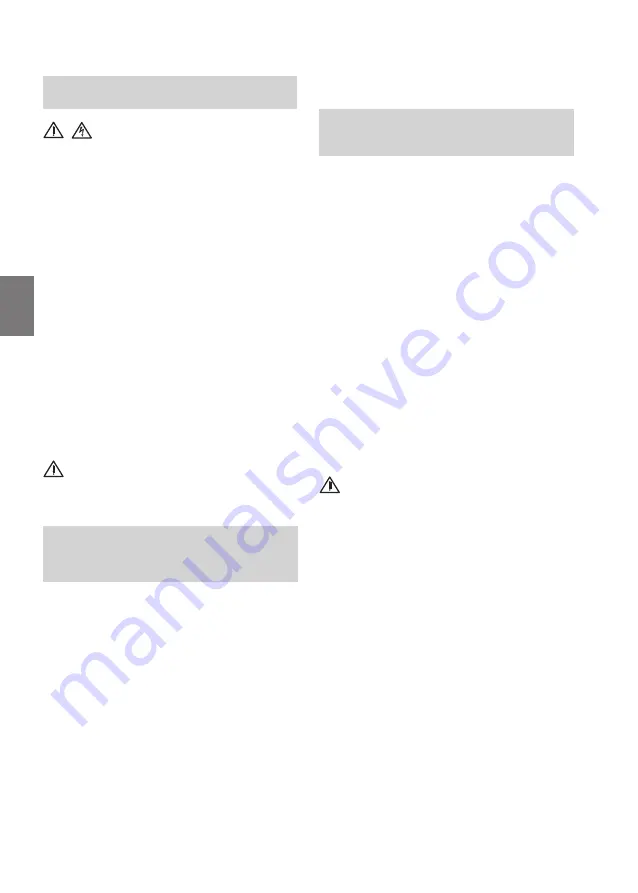
28
E
N
G
L
IS
H
4. Maintenance
Any work on the motor is to be carried
out with the machine stopped and disconnected
from the power supply.
Over time the original characteristics of the motor
with brake can only be ensured by means of an
inspection and maintenance programme prepared
and managed by qualified technicians.
The type of maintenance and frequency of checks
depends on the ambient and working conditions.
Especially wear on the brake disc depends on vari-
ous factors: load inertia, motor rotation speed, and
frequency of engaging.
As a general rule we recommend an initial inspection
after about 500 working hours and not later than one
year after starting up for the first time. Subsequent
inspections must be carried out according to sched-
uled plans.
In order to work accurately, the motor must be dis-
mantled from the machine and placed on a work-
bench with all the tools and equipment required to
hand.
During dismantling and assembly proce-
dures, accident prevention standards and safety
information must be complied with rigorously.
For self-ventilated motors (H Series) (fig. 2A) remove
the fan cover
bq
by unscrewing the fixing screws and
remove the fan
cr
.
For motors fitted with a manual brake release (fig.
2F), pull the hand lever
D
outwards, hold it up and
put a pin throuch the hole.
Unscrew the fixing screws and remove the brake
cover enclosure being careful not to damage the
flameproof joints.
Having completed the inspection or maintenance,
before closing the brake cover enclosure:
• Make sure that the air gap is set correctly (see
paragraph 4.4).
• Reinstate the original layer of grease (e.g.
Molyduval Bariplex grease) on the flameproof
joints.
• Check that the friction surfaces (brake disc, brake
holder shield, and mobile armature) are clean and
free from oil or grease.
The motor is supplied with a ready-to-use calibrated
brake. Customers with special application needs can
ask for a customised calibration setting. The braking
torque is shown on the motor’s nameplate.
The braking torque can be adjusted to suit working
needs. In this case, we suggest avoiding values that
are too high as these could prevent normal opening
of the brake, or values that are too low as these could
cause the brake to slip.
Reducing the braking torque to below the maximum
value, under certain load conditions, will result in a
reduced wear of the brake’s friction material.
For size 71÷160 motors (fig. 2C) the brake torque is
adjusted by turning the nuts
et
to change distance
A
. When these are turned anticlockwise the braking
torque is reduced.
For size 63 motors, it is not possible to adjust the
braking torque. The reference value of the braking
torque is shown in table 4A.
In order to obtain even braking torque set-
tings length
A
must be the same for all the
springs.
The table below shows the braking torque values in
relation to distance
A
.
These torque values are subject to a tolerance of
-20% compared to the values shown in the table.
4.1 Introduction
4.2 Dismantling and re-assembling
the brake cover enclosure
motors 63÷160
4.3 Adjusting the braking torque
motors 63÷160