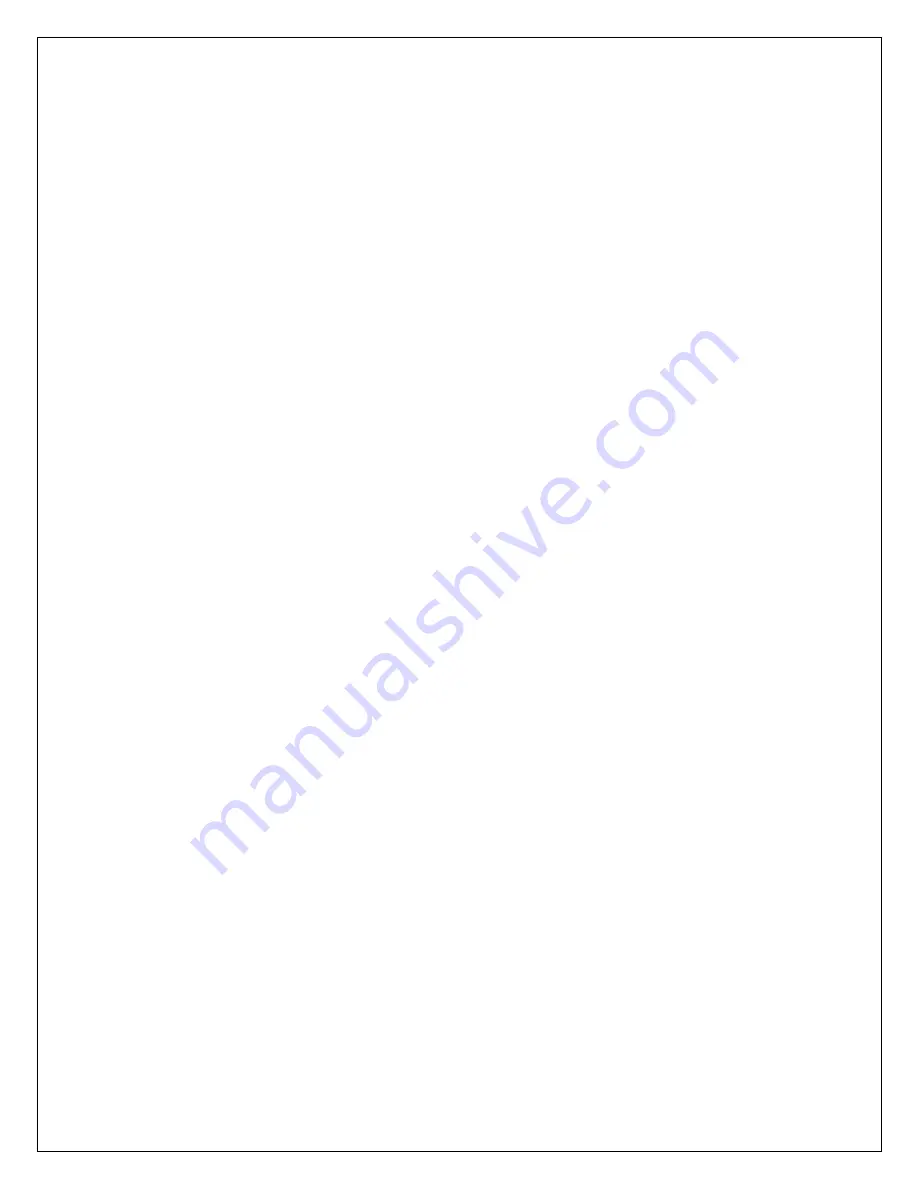
- 13 -
Service Guide
CAUTION:
•
ALWAYS USE THE SUPERHEAT AND SUBCOOLING, PRESSURE
READINGS TO CHARGE REFRIGERANT PROPERLY, THE LISTED
CHARGES ARE FOR REFERENCE ONLY.
•
CHARGE 15% MORE REFRIGERANT IN THE SUMMER IF THE UNIT IS
EQUIPPED A LOW AMBIENT CONDITION KIT
NOTES:
•
THE VALVE CONNECTION SIZES OF CONDENSING UNIT AND THE LINE
CONNECTION SIZES OF EVAPORATOR UNIT ARE NOT NECESSARY
THE SAME AS THE ABOVE SPECIFIED LINE SIZES.
•
IF THE CONDENSING UNIT IS INSTALLED ABOVE THE EVAPORATOR
UNIT, USE THE SUCTION LINE ONE LISTED SIZE SMALLER.
•
EXPANSION AND SOLENOID VALVES ARE INSTALLED ON LIQUID LINE.
1. Refrigeration Piping, Evacuating, Charging and Starting
•
The installation order starts from condensing unit (including the receiver,
discharge valve), liquid line filter-drier, moisture-liquid indicator/sight glass,
liquid line, to evaporator unit (including liquid line connection, solenoid
valve, expansion valve, and suction line connection), returning to insulated
suction line, suction valve and then condensing unit.
•
Use inverted siphons to prevent liquid from flooding back to the
compressor and aid oil returning to the compressor.
•
Charge the system after pipe brazing, leak testing and evacuating. Liquid
must always be charged into the hide side.
•
It may use fan speed control to adjust the air flow to achieve the specified
CFM. Turn control knob clockwise to the lowest speed position, locate and
adjust the minimum speed setting (on the side or front) with screw driver.
Rotate the setting clockwise to decrease minimum speed or counter-
clockwise to increase minimum speed). The minimum speed should be
adjusted until it supplies the required CFM. The fan will run from this
preset minimum speed to full speed with the control knob at lowest and
highest speed position.
•
The subcooling at the condensing unit shall be around 10
°
F. The charge
may be complete when there are no more bubbles forming in the sight
glass.
•
Head pressure: 125-150 psig at 70 -90
°
F ambient temperatures.
•
The evaporator’s constant pressure expansion valve is set around 35-
40
°
F at factory. This pressure setting gives a dew point to maintain the
humidity for storing wine.
•
Suction pressure: Adjust the AXV to 30-35 psig.
•
The temperature split between return air and supply air shall be 8-10
°
F at
55
°
F wine room temperature.
Содержание 1/2 Ton-DS
Страница 21: ...20 Fig 16 CellarTec 1 3 Ton DS Electrical Wiring Diagram...
Страница 22: ...21 Fig 17 CellarTec 1 2 Ton DS Electrical Wiring Diagram...
Страница 23: ...22 Fig 18 CellarTec 3 4 Ton DS Wiring Diagram...
Страница 24: ...23 Fig 19 Low Ambient Temperature CellarTec 1 3 Ton DS Electrical Wiring Diagram...
Страница 25: ...24 Fig 20 Low Ambient Temperature CellarTec 1 2 Ton DS Electrical Wiring Diagram...
Страница 26: ...25 Fig 21 Low Ambient Temperature CellarTec 3 4 Ton DS Wiring Diagram...