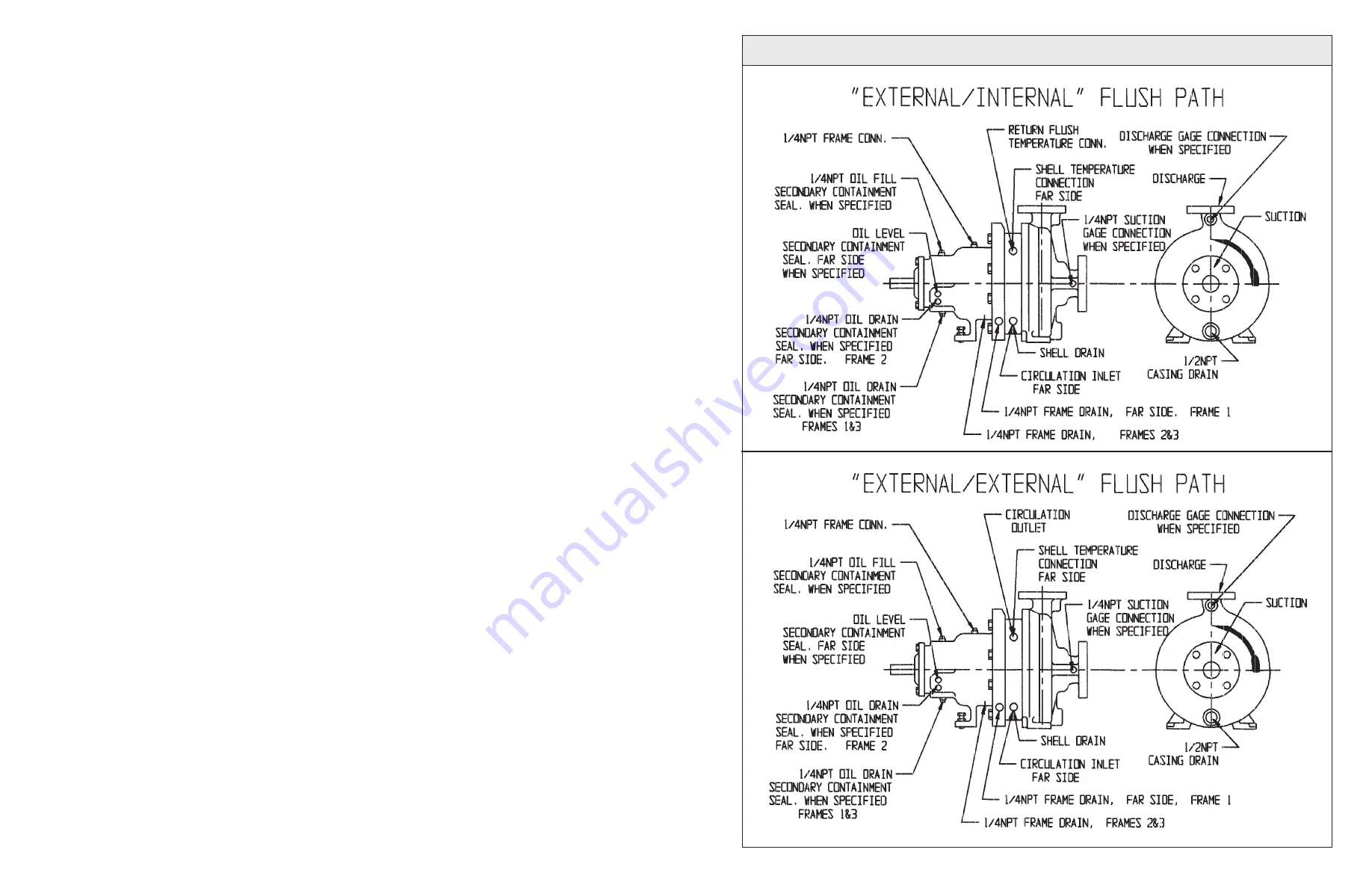
16
13
These points must be checked after
pump installation and before starting up
the pump.
1) Read the instruction manual
thoroughly and understand it.
2) Review the pump order headsheet
for the service rating of the pump
and any special features.
3) Check all piping connections making
certain they are both tight and in the
proper places. Piping includes flush-
ing, cooling or heating piping.
Be sure that the casing drain and
the containment shell drain are not
connected together.
4) Make certain no insulation has been
placed over any air cooling surfaces
of the pump or its auxiliary piping.
5) Make sure the baseplate has been
properly installed.
6) Check the electrical or steam line
connections to the driver.
7) If the pump is equipped with air
cooled (finned) auxiliary piping,
make sure the drive motor is fan
cooled.
8) Break the coupling by removing
the coupling spacer and bump the
motor starting button to check
motor rotation. Operating the
pump in reverse rotation may
cause extensive damage.
If the driver rotation is incorrect,
reconnect the wiring for proper
rotation and re-check.
9) Check the coupling for proper
alignment of the motor and rotor
shafts. Re-align if necessary.
Replace the coupling spacer.
10) If the pump has the optional
“Secondary Containment Seal”
check to see that it is properly
lubricated.
11) Make sure the pump is filled with
liquid and vented to remove any air.
12) Turn on any cooling or heating to the
pump and/or auxiliary equipment.
13) Rotate the pump shaft by hand to
be sure there is no binding or rub-
bing within the pump or driver.
Correct any difficulties at once.
14) Remove all dirt, waste, tools and
construction debris from the area.
15) Make sure the coupling guard is
securely in place.
16) Start the pump and immediately
check for proper flow and pressure.
17) Perform extra venting procedure if
required. See “Starting the Pump”.
PUMP START-UP CHECKLIST
PIPING CONNECTIONS FOR M300 SERIES PUMPS - EXTERNAL