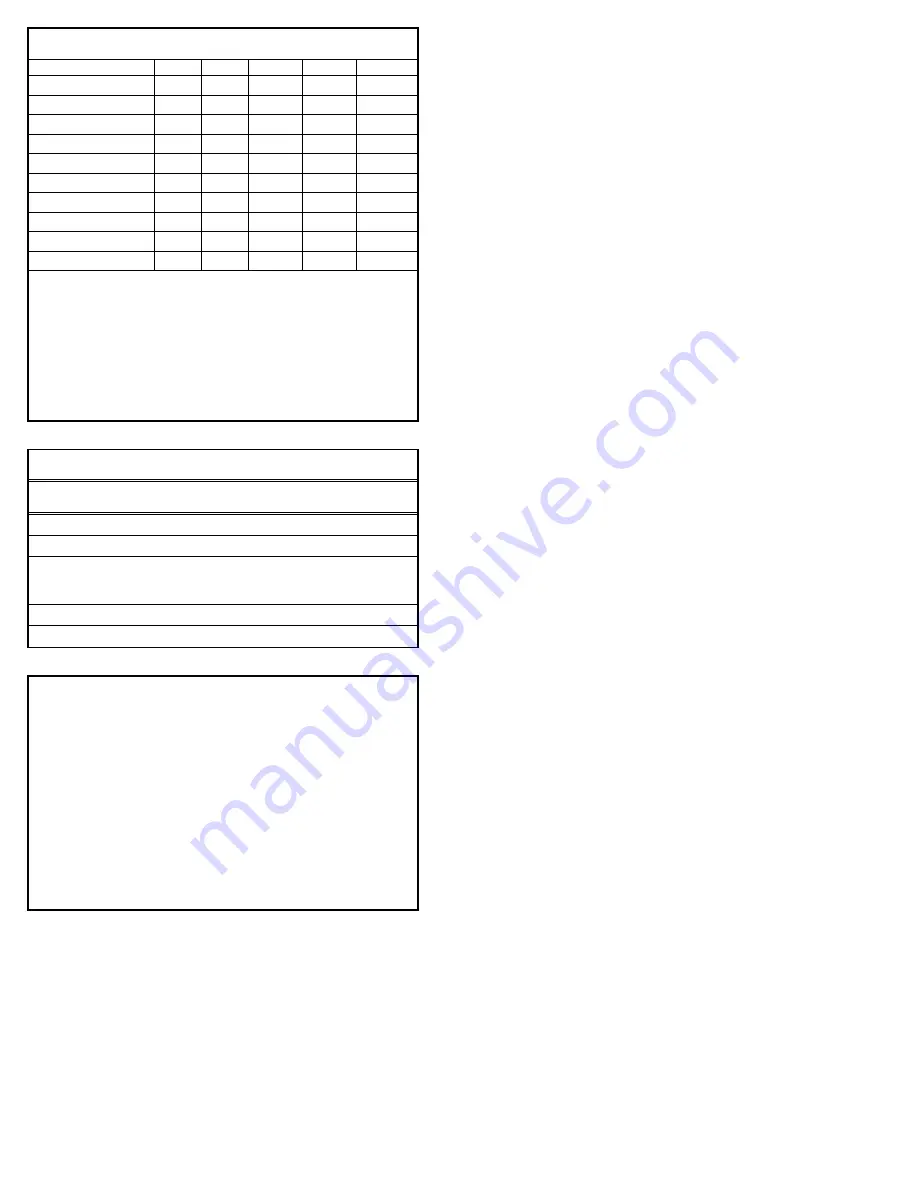
PREVENTATIVE MAINTENANCE CHECK-LIST
Check
Daily
Weekly
50 hrs.
500 hrs.*
1000 hrs.**
Clean Filters
x
Oil Level/Quality
x
Oil Leaks
x
Water Leaks
x
Plumbing
x
Initial Oil Change
x
Oil Change
x
Seal Change
x
Valve Change
x
Accessories
x
INLET CONDITION CHECK-LIST
Review Before Start-Up
Inadequate inlet conditions can cause serious malfunctions in the best
designed pump. Surprisingly, the simplest of things can cause the
most severe problems or go unnoticed to the unfamiliar or untrained
eye. REVIEW THIS CHECK-LIST BEFORE OPERATION OF ANY
SYSTEM. Remember, no two systems are alike, so there can be no
ONE best way to set-up a system. All factors must be carefully con-
sidered.
INLET SUPPLY should exceed the maximum flow being delivered by the
pump to assure proper performance.
❏
Open inlet shut-off valve and turn on water supply to avoid starving the
pump. DO NOT RUN PUMP DRY.
❏
Temperatures above 130°F are permissible. Add 1/2 PSI inlet pressure per
each degree F over 130°F. Elastomer or RPM changes may be required.
See Tech Bulletin 002 or call CAT PUMPS for recommendations.
❏
Avoid closed loop systems especially with high temperature or ultra-high
pressure. Conditions vary with regulating/unloader valve.
❏
Higher temperature liquids tend to vaporize and require positive heads.
❏
When using an inlet supply reservoir, size it to provide adequate
liquid to accommodate the maximum output of the pump, generally a
minimum of 6-10 times the GPM (however, a combination of system
factors can change this requirement); provide adequate baffling in the
tank to eliminate air bubbles and turbulence; install diffusers on all
return lines to the tank.
INLET LINE SIZE should be adequate to avoid starving the pump.
❏
Line size must be a minimum of one size larger than the pump inlet
fitting. Avoid tees, 90 degree elbows or valves in the inlet line of the
pump to reduce the risk of flow restriction and cavitation.
❏
The line MUST be a FLEXIBLE hose, NOT a rigid pipe, and reinforced
on SUCTION systems to avoid collapsing.
❏
The simpler the inlet plumbing the less the potential for problems. Keep
the length to a minimum, the number of elbows and joints to a minimum
(ideally no elbows) and the inlet accessories to a minimum.
❏
Use pipe sealant to assure air-tight, positive sealing pipe joints.
INLET PRESSURE should fall within the specifications of the pump.
❏
Acceleration loss of liquids may be increased by high RPM, high
temperatures, low vapor pressures or high viscosity and may require a
pressurized inlet to maintain adequate inlet supply.
❏
Optimum pump performance is obtained with +20 PSI (1.4 BAR) inlet
pressure. With adequate inlet plumbing, most pumps will perform with
flooded suction. Maximum inlet pressure is 60 PSI (4 BAR).
❏
After prolonged storage, pump should be rotated by hand and purged
of air to facilitate priming. Disconnect the discharge port and allow liquid
to pass through pump and measure flow.
INLET ACCESSORIES are designed to protect against over pressuriza-
tion, control inlet flow, contamination or temperature and provide ease of
servicing.
❏
A shut-off valve is recommended to facilitate maintenance.
❏
A stand pipe can be used in some applications to help maintain a
positive head at the pump inlet line.
❏
Inspect and clean inlet filters on a regular schedule to avoid flow restriction.
❏
A pressure transducer is necessary to accurately read inlet pressure.
Short term, intermittent cavitation will not register on a standard
gauge.
❏
All accessories should be sized to avoid restricting the inlet flow.
❏
All accessories should be compatible with the solution being pumped to
prevent premature failure or malfunction.
BY-PASS TO INLET Care should be exercised when deciding the method
of by-pass from control valves.
❏
The 2DX, 3DX, 3DNX and 3SPX pumps come with a Integral Unloader
with built-in by-pass to route by-pass liquid back to the pump inlet. The
3SP pumps come with a Regulating Unloader and reinforced, flexible
hose rated up to 300 PSI. No additional by-pass hose is required. The
1DX.MIST and 2DX.MIST pumps come with a Integral Regulator.
TORQUE CHART
Torque
Pump Item
Thread
Tool Size [P/N]
in. lbs. ft. lbs. Nm
Plunger Retainer
M6
M10 Hex [25082]
55
4.6
6.2
Manifold Head Screws
M6
M5 Allen
55
4.6
6.2
Valve Plugs
1DX.MIST, 2DX, 2DX.MIST, M20
M19 Hex
520
43
58
3DX, 3DNX, 3SP, 3SPX
M22
M24 Hex [44046]
870
72.5 98
Bearing Cover Screws
M6
M10 Hex [25082]
50
4.0
5.4
Bubble Oil Gauge
M28
Oil Gauge Tool [44050]
45
3.6
5
TECHNICAL BULLETIN REFERENCE CHART
No. Subject
Models
002 Inlet Pressure VS Liquid Temperature
All Models
024 Lubrication of Lo-Pressure Seals
All Models
036 Cylinder and Plunger Reference Chart
All Models
043 LPS and HPS Servicing
All Plunger Models
055 Removing Pumps from Gas Engine or Electric Motor
1DX, 2SF, 2SFX, 2X, 2DX, 3DX,
3DNX, 3SP, 3SPX, 4SF, 4HP, 5DX,
6DX, 66DX
074 Torque Chart
Piston and Plunger Pumps
083 Winterizing a Pump
All Models
086 Ceramic Plunger
2DX
094 Modular Unloader Valve and Seat
2DX and 3DX
* If other than CAT PUMPS special custom blend, multi-viscosity ISO68 hydraulic
oil is used, change cycle should be every 300 hours.
** Each system’s maintenance cycle will be exclusive. If system performance
decreases, check immediately. If no wear at 1000 hours, check again at
1500 hours and each 500 hours until wear is observed. Valves typically
require changing every other seal change.
Duty cycle, temperature, quality of pumped liquid and inlet feed conditions all
effect the life of pump wear parts and service cycle.
** Remember to service the regulator/unloader at each seal servicing and check
all system accessories and connections before resuming operation.