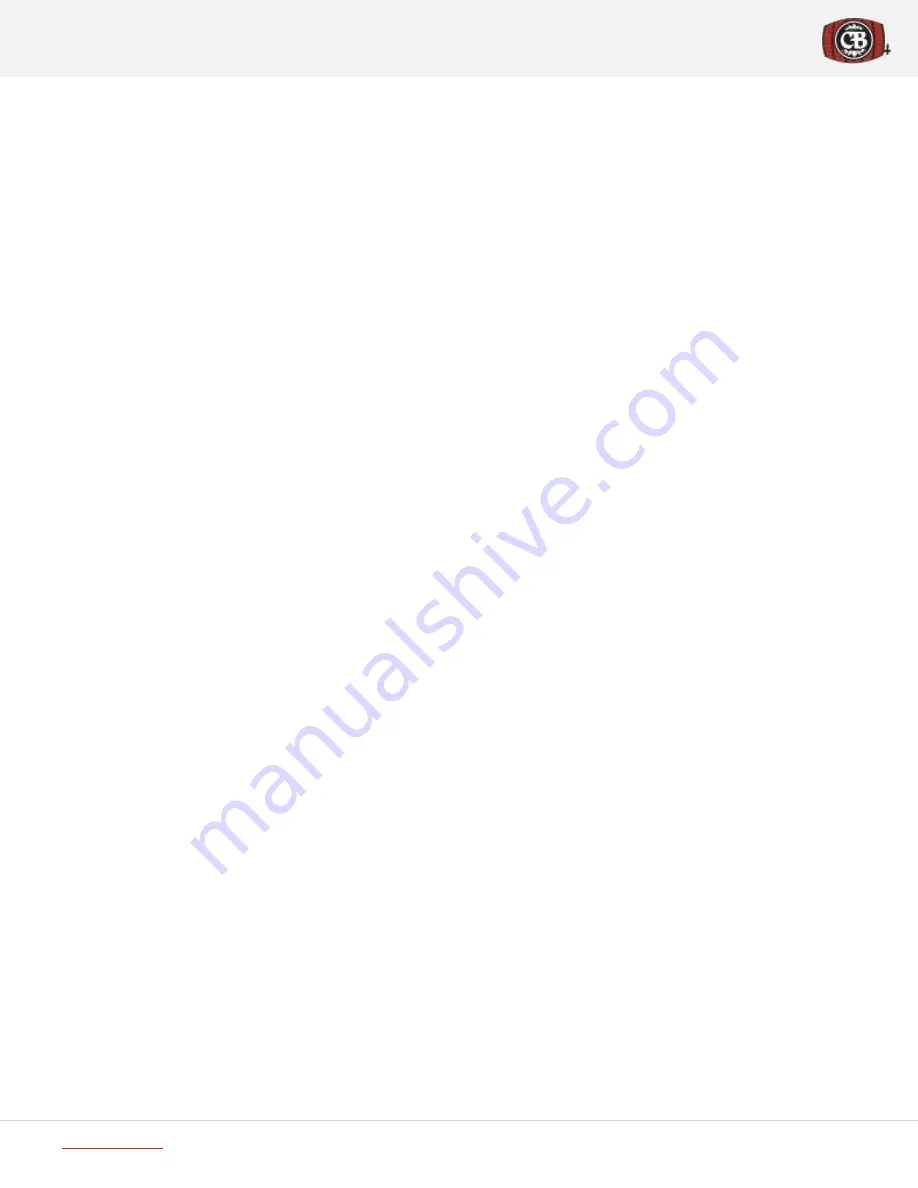
+1-800-661-8443
Third Edition, Nov 2016
ACS V4.2
Page
|
47
Section F. Can Seamer
Grasp the can in one hand and the base plate table in the other and try to turn these in opposite directions.
If you can turn them and feel the can slipping on the base plate, there is probably too little pressure.
Try raising the platform another quarter turn and try again.
Once properly adjusted be sure to retighten the set bolt.
F.1.3.2
Can Table Pressure - Test for Too High
Place an empty can on the platform, lid in place.
Raise the platform.
Press against the can wall with your finger.
A small amount of pressure should cause the can to indent and remain indented after you move your finger.
If you lower the can and the dent pops out, you have a good can table pressure. If the dent remains in the can
when the table is lowered, you have too much can pressure and should adjust the can table down a quarter turn
and repeat.
F.1.4
Speed of Cylinder Motion
In addition to the above adjustments, the speed at which each of the seaming wheels moves into place during the
approximately 2 second long seaming cycle can also affect the final seam specifications. This speed is controlled by the
flow controls on air valves which control the flow of air to the air cylinders that move the seaming wheels and the can
platform. Refer to Section D.8.2.1 Air Cylinder Speed Adjustment on Page 31 for details on how to adjust the air cylinders.
F.2
Seamer Troubleshooting
Testing the First Operation Seam Roll Thickness
A test seam must be done with water or beer filled can in manual mode.
Place can on table and push “Test Die 1”.
Check the thickness of this seam as shown (Figure 36 Proper Seam Micrometer usage on Page 41).
o
Note
For most accurate measurements, the use of a can seam micrometer is recommended.
If the seam thickness is too high, the seam roll must be moved closer to the chuck (F.1.1 Seaming Wheel Proximity
Adjustment on Page 45). If too tight (small) it must be moved away from the chuck.
Verify also that the first operation seam height (Figure 36 on Page 41) is within 0.003”-0.005”of the first op seam
thickness. If it is too short, the seam roll height must be raised.
F.3
Bearing Replacement
Changing bearings on the Cask Canning System is relatively simple; however, it can be frustrating if these simple steps
below in Figure 43 are not followed in order of operation.