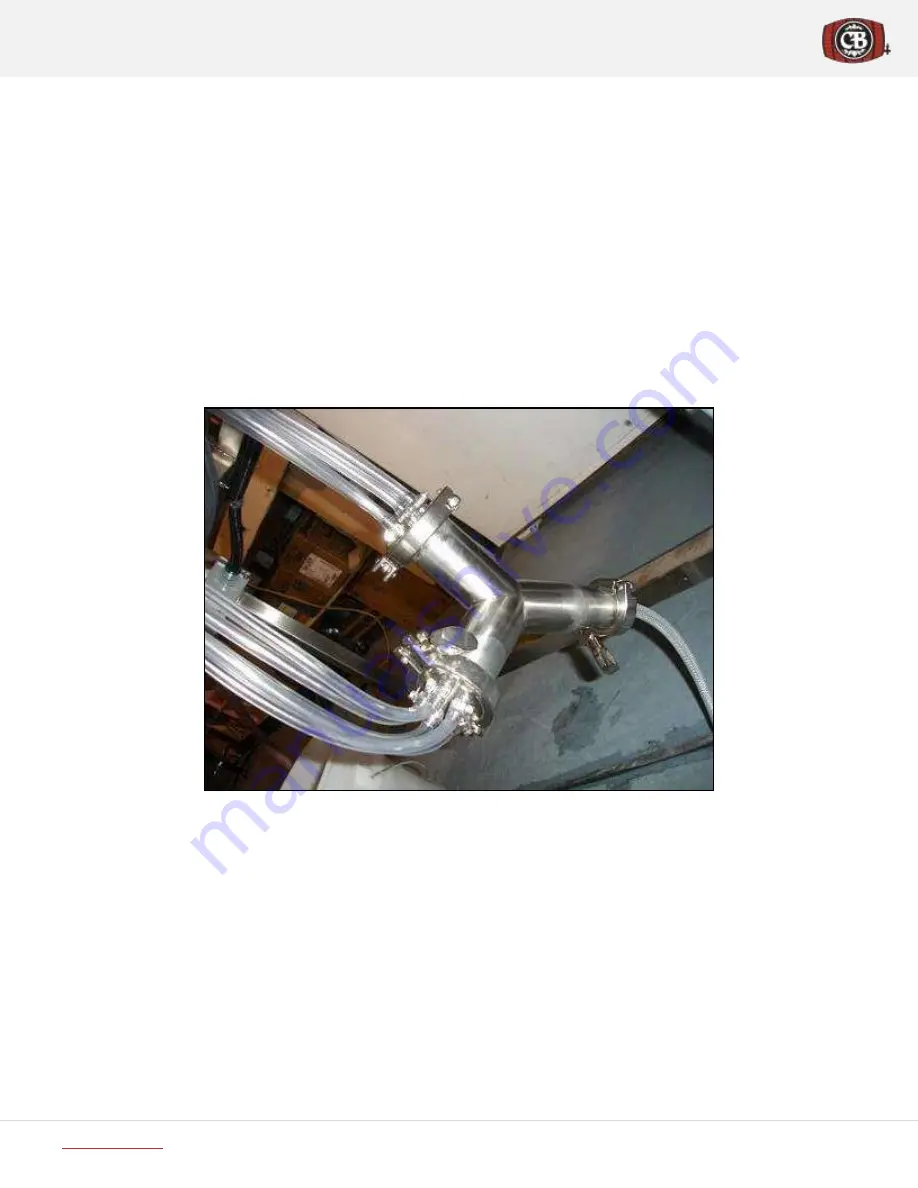
+1-800-661-8443
Third Edition, Nov 2016
ACS V4.2
Page
|
16
Section C. ACS Operations Overview
C.4.2
Beer Manifold
Beer should be carbonated to 2.4 to 2.9 volumes of CO2 (or 4.6 to 5.6 g/L).
Beer Temperature of 0 – 2C or 32 – 35.6F (colder for higher CO2 volumes).
CO2 supply to bright tank should be set at 13 – 15 PSI (depending on CO2 volume, temperature and distance from
dispense tank).
In order to fill a can, the first step required is to have your product connected to the machine. The manifold allows a single
hose line (1.5” tri clamp connection) to be connected from your tank to the machine, and then splits it ten ways to supply
each valve in the fill head. The valves are rated to a maximum pressure of 24 PSI, so it is important not to exceed that line
pressure or fill valves will fail to open. In Figure 14 you can see the two sets of five supply lines that are connected to the
valves in the fill head, as well as the single supply line from the tank.
Best practise is to install a temperature and pressure gauge on the end of the beer manifold to allow monitoring of
temperature and pressure of the beer at the delivery point to the machine.
Figure 14 Beer Manifold
C.4.3
Fill Head Manifold
The gate downstream of the fill head stops the cans creating a backlog all the way to the shaker table (Figure 15). This
backlog is important as the spacing of spouts in the fill head are based on the cans being right up against each other. There
are 10 cans under the fill head. The last 5 are purged with CO2 as the first five (already purged) are filled with beer. After
the fill is complete the head retracts to the up position and the gate opens. The sensor immediately upstream of the gate
counts 5 cans before re-closing the gate and beginning the next fill cycle.