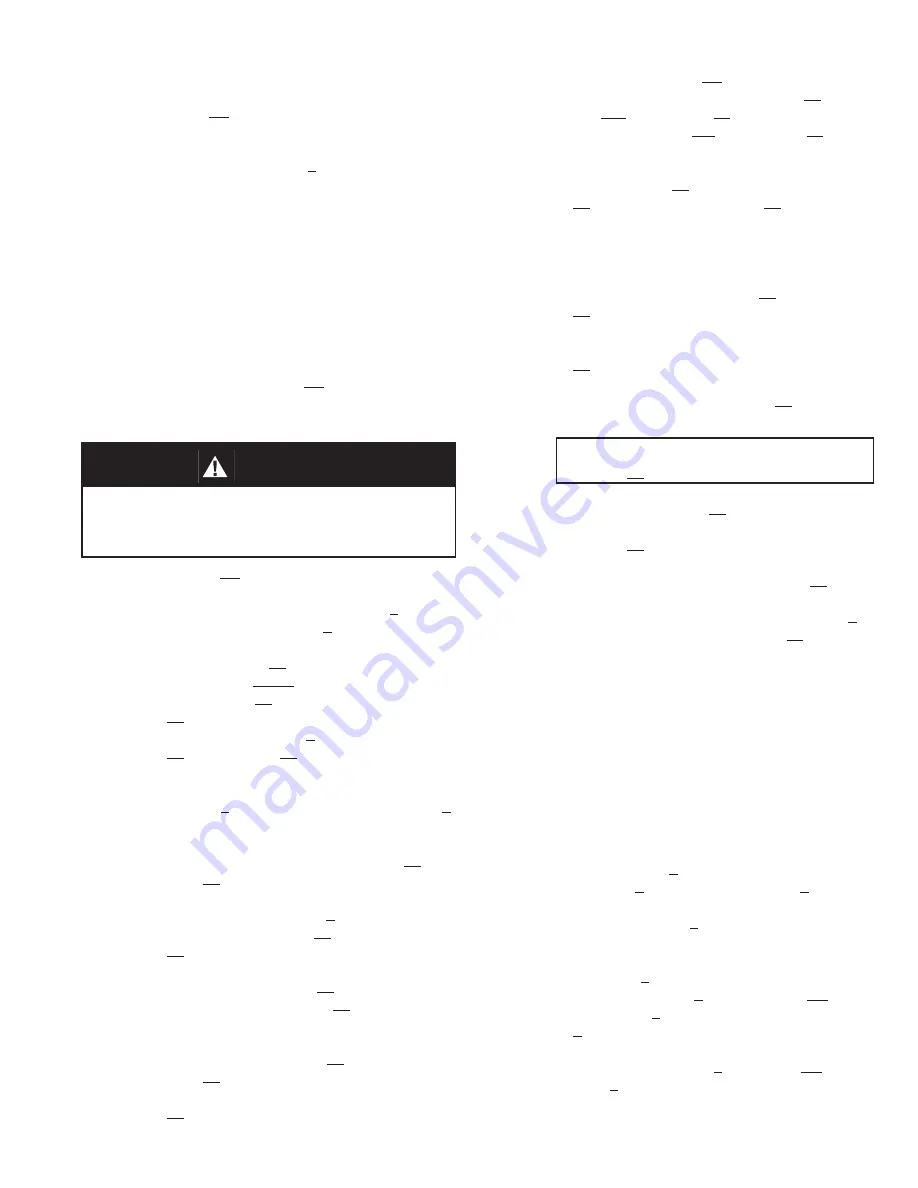
IOM-POSR-1
5
4. Place pipe wrench on interconnecting pipe
nipple (19) and rotate CCW (viewed from pilot
valve (PV) end) to removal. Remove main
valve (MV) from vise and set aside.
5. Place pilot valve body (1) in vise. Remove pipe
nipple (19) by rotating CCW (viewed from end
of nipple) by pipe wrench.
6. Inspect the inside of the inter-connecting pipe
nipple (19) for corrosion, scaling, debris, or
filming. Prob lems here will be an in di ca tion
of improper condensate cor ro sion control
which can affect the overall operation of the
POSR-1. Install an upstream strainer if scale
or debris ap pears at this point.
7. Remove pilot valve (PV) from vise and set
aside.
NOTE:
Pilot valves (PV) supplied with a 5–15
psig (0.34–1.03 Barg) range spring (15) have
only one di a phragm (12) sup plied; all other
spring ranges use two diaphragms (12).
7. Using a putty knife or similar tool, remove
diaphragm(s) (12) and di a phragm gasket
(13). In spect diaphragm(s) (12) for cracks
or de for ma tion. Radial creases and cracks
in di cate over pres sure. Cracks circumferentially
in di cate high cycles, and may be due to nor mal
cy cling, or pulsing or chattering if pre ma ture.
Discard both diaphragm(s) (12) and gas ket
(13).
8. Using a 7/8" deep well socket, remove bel lows
(11) by rotating CCW (viewed from above).
Count and record the number of revolutions
required to remove the bellows (11) in the box
below:
Number of revolutions required to remove
bellows
(11):________________.
Inspect the bellows (11) for a crack or joint
failure where leakage is occurring. Replace
bellows (11) if leaking.
9. Remove protruding stem extension (10).
10. Using a flat, sharp-edged tool, clean body (1)
flange where diaphragm gasket (13) seals.
11. Using a wire gauge tool, clean the 0.068"
(1.73 mm) diameter bleed orifice located in
the body cavity (smaller of two holes) of any
film or other buildup material that might be
restricting flow.
NOTE:
Any significant blockage of the
bleed orifice will downgrade a POSR-1's
per for mance. If a buildup is form ing, attempt to
determine the cause and remove the source.
12. Remove body (1) from vise and reorient with
body cap (9) on top; resecure body (1) in vise.
13. Remove body cap (9) by rotating CCW (viewed
from above) with hex-end wrench. Hammer-
rapping the wrench may be necessary, as the
body cap (9) has a metal-to-metal shoulder
joint with the body (1).
NOTE:
Plug (4.2) and
plug spring (7) may come out with body cap
(9) removal.
14. Remove plug spring (7) and plug (4.2) from
body (1) recess.
WARNING
SPRING UNDER COMPRESSION. Pri or to re mov ing body
flange bolts, relieve spring com pres sion by back ing out
the adjusting screw. Failure to do so may result in flying
parts that could cause personal injury.
C. Pilot Valve (PV):
1. Securely install the pilot valve body (1) in a vise
with the spring chamber (2) directed upwards.
2. Loosen locknut (20) by rotating CCW (viewed
from above) ONLY two revolutions. Relax
range spring (15) by turning adjusting screw
(19) CCW (viewed from above) until removed
from spring chamber (2). Set ad just ing screw
(19) with locknut (20) aside.
3. Draw or embed a match mark between body
casting (1) and spring chamber casting (2)
along flanged area.
4. Remove all diaphragm flange nuts (18) and
bolts (17).
5. Remove spring chamber (2) by lifting up wards.
Re move range spring (15) and spring button
(16).
6. Remove pressure plate(14). In spect to en sure
that the pressure plate (14) has not been
deformed by over pres sure by placing a
thin, straight bar or ruler across the side that
touch es the diaphragm (12). If the pressure
plate (14) does not touch the bar at its center
(i.e. a depression in center), the pres sure plate
(14) is deformed and must be replaced.