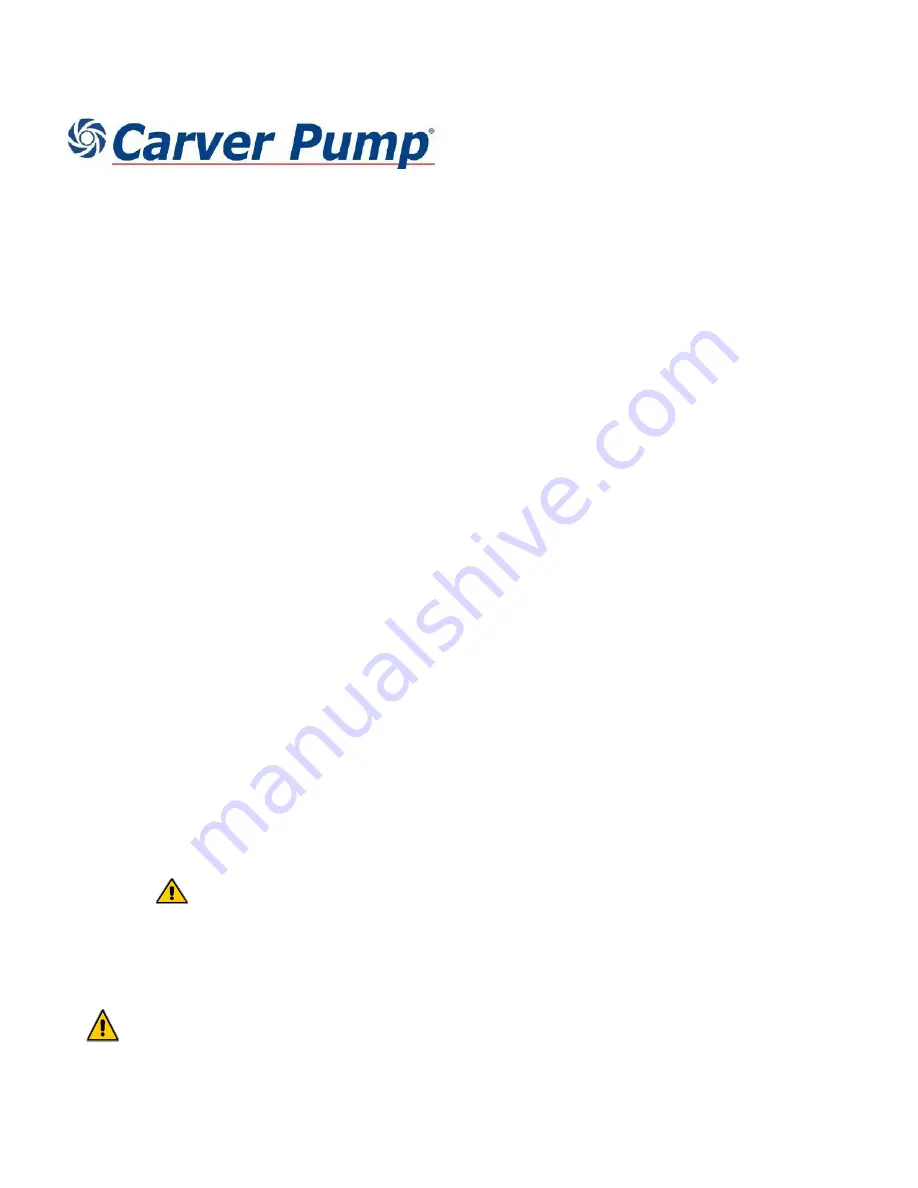
G2S
Line-Shaft Sump Pump
INSTALLATION, OPERATION AND
MAINTENANCE INSTRUCTIONS
This manual shall always be kept close to the unit’s lo
cation of operation or directly on the pump set.
Part Number: _______________________________________
Serial Numbers: _____________________________________
These operating instructions contain fundamental information and precautionary notes.
Please read the manual thoroughly prior to installation of unit, electrical connection and
commissioning. It is imperative to comply with all other operating instructions referring to
components of individual units.
I-481
DEC 2016
ATEX REV.0
Inch Units
Содержание G2S
Страница 2: ...This page left intentionally blank ...
Страница 6: ...This page left intentionally blank ...
Страница 25: ...G2S I 481 Line Shaft Sump Pump December 2016 19 Figure 3 G2S Sectional Drawing ...
Страница 29: ...G2S I 481 Line Shaft Sump Pump December 2016 This page left intentionally blank ...
Страница 30: ...I 481 DEC 2016 ...