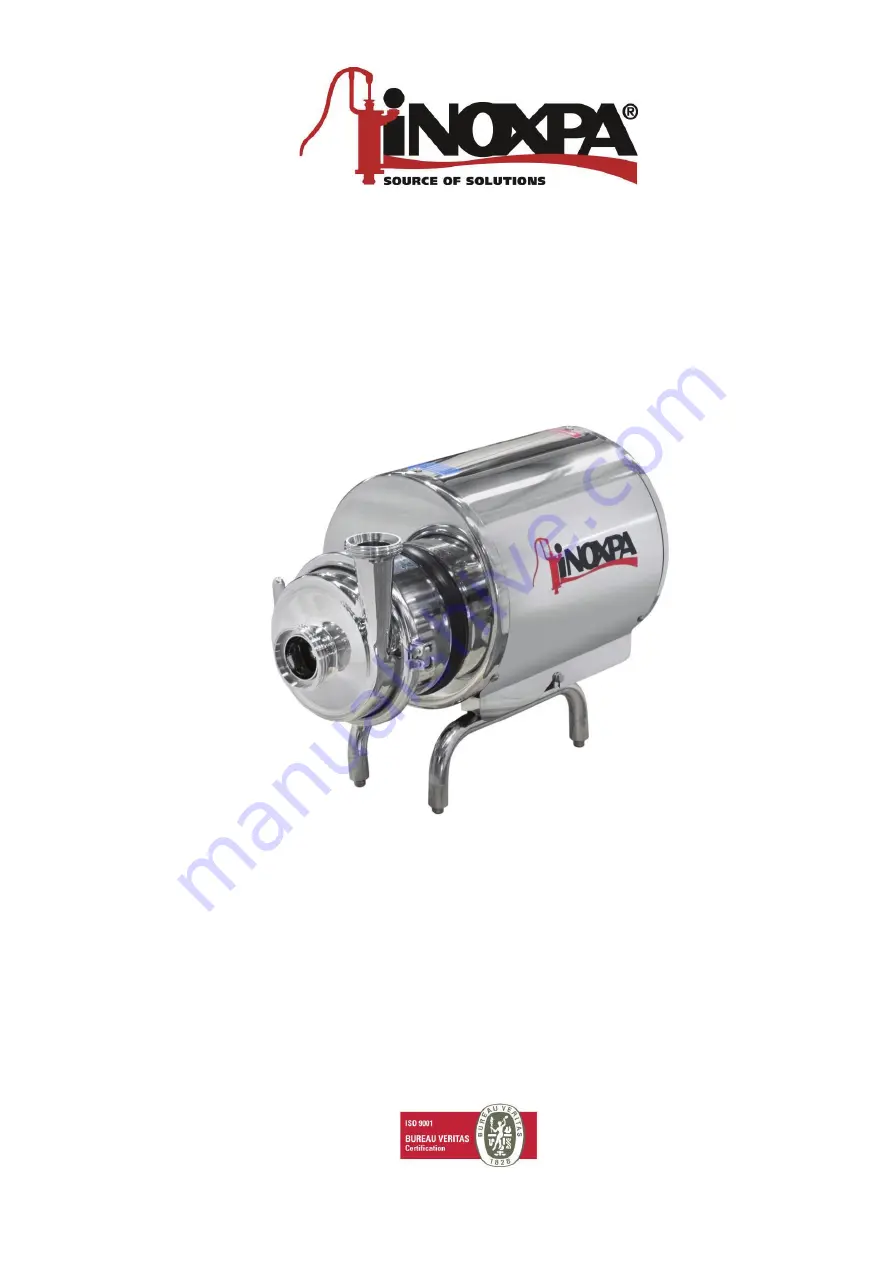
INSTALLATION, SERVICE AND
MAINTENANCE INSTRUCTIONS
HYGINOX SE
INOXPA, S.A.
c/Telers, 54 Aptdo. 174
E-17820 Banyoles
Girona (Spain)
Tel. : (34) 972 - 57 52 00
Fax. : (34) 972 - 57 55 02
email: [email protected]
www.inoxpa.com
01.011.30.05EN
(0) 2015/01
01
.01
1
.3
2
.0
0
0
1