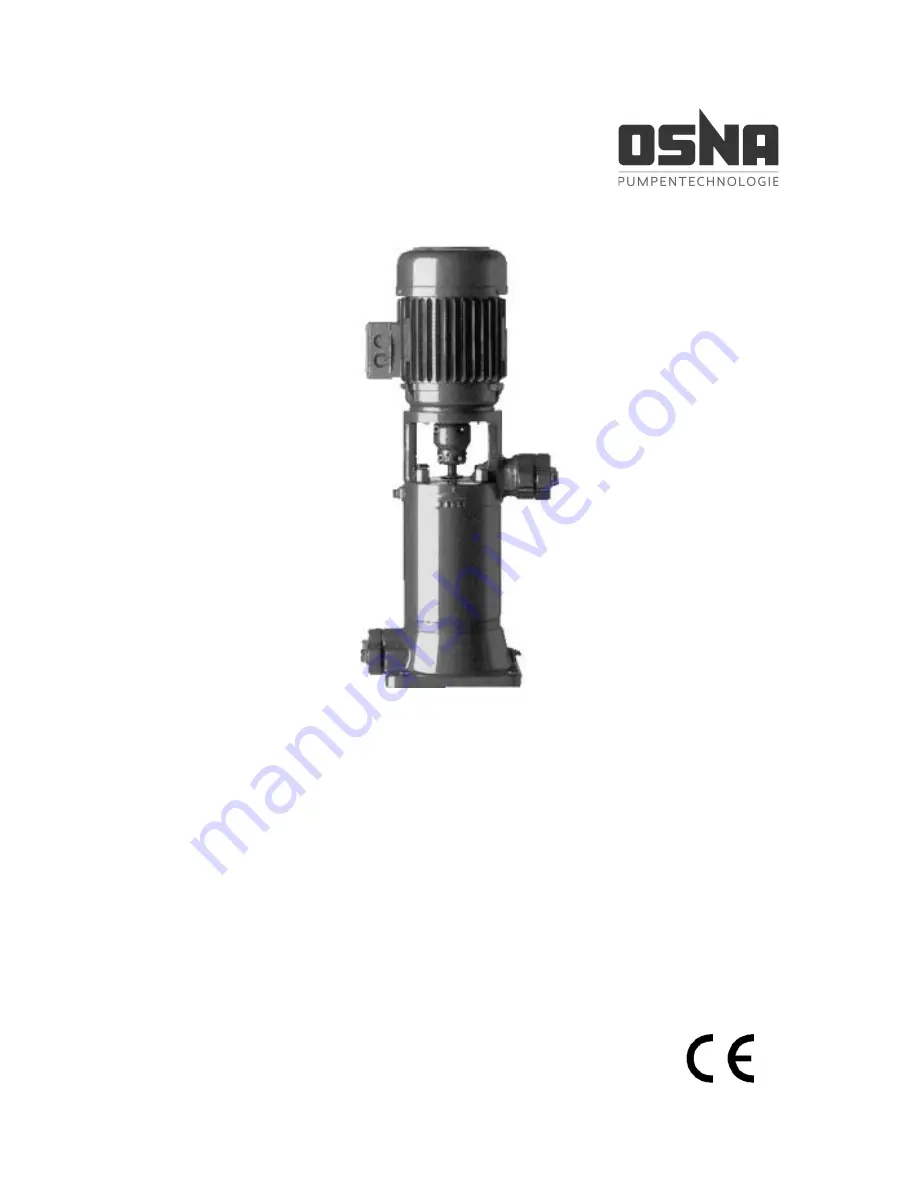
Ver.17-01
Original Operating Manual
CVP High-Pressure Centrifugal Pump
OSNA-Pumpen GmbH
Brückenstrasse 3
49090 Osnabrück, Germany
Phone: +49 541 1211 - 0
Fax:
+49 541 1211 - 220
Internet: http://www.osna.de
E-mail: [email protected]
Summary of Contents for CVP 423
Page 2: ......