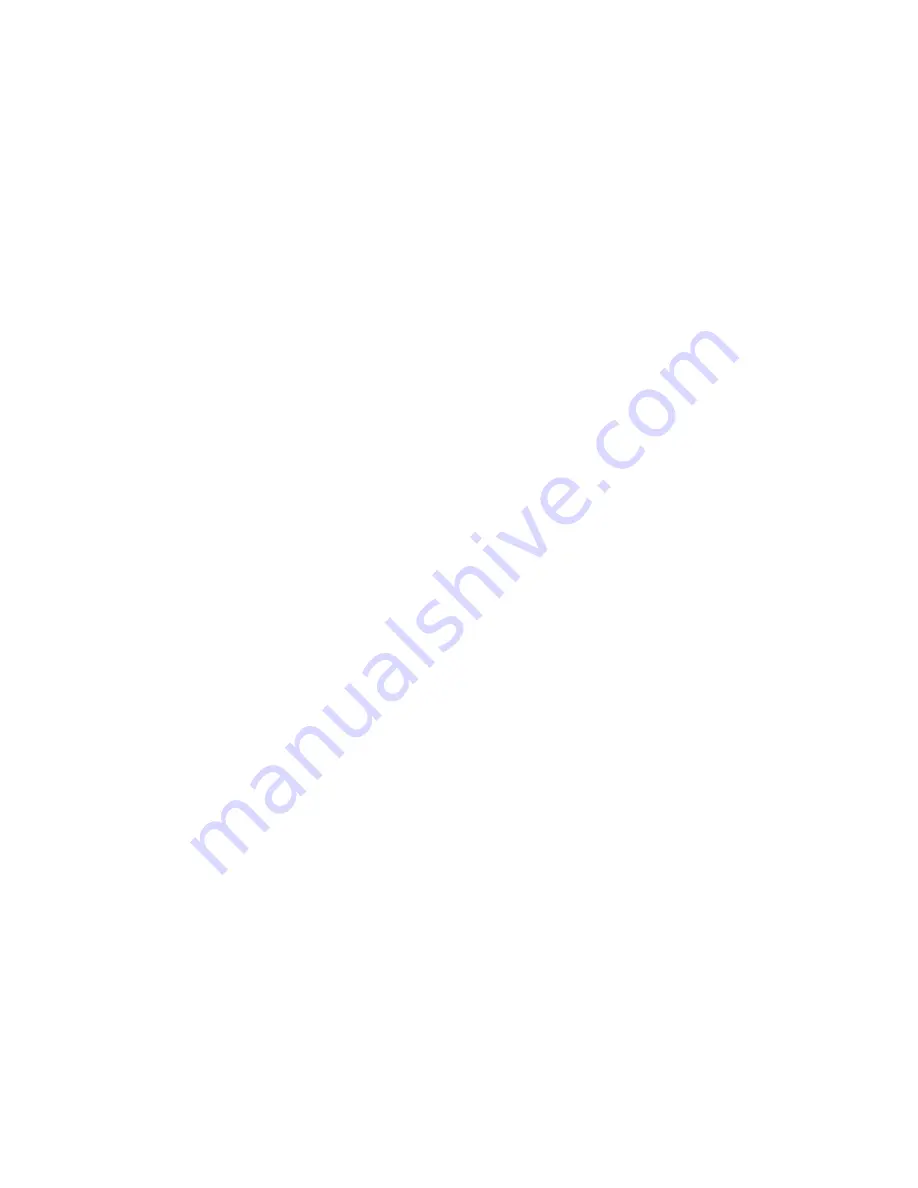
20
FIRE INPUT (FSD) — This is a normally closed input con-
nected to the controller. When this input is opened, all control
outputs are immediately turned off, including the fan.
DUCT HIGH STATIC INPUT (DHS) — This differential air
pressure switch provides backup protection for the ductwork. It
is factory installed in the unit and wired to the unit controller.
This switch has a manually adjustable set point with a range of
1 to 5 in. wg. Upon switch closure, the controller immediately
turns all outputs off, including fan, and then indicates an alarm
both by turning on its alarm output, the BACview alarm lamp
and via communications (if used).
DIRTY FILTERS SWITCH (FLTS) — This is a factory-in-
stalled option on the 50XJ unit. This input is used to connect a
pressure switch that measures the air pressure difference across
the filters. When the delta increases beyond the preset setting, a
dirty filter alarm is activated, indicating that the filters need
cleaning or replacement.
The switch is normally open, with manually adjustable set-
ting at the switch between 0.5 and 1.5 in. wg. Upon closure,
controller holds the alarm for 1 minute to assure that the condi-
tion is stable and then it activates the alarm. Beyond the alarm,
the dirty filter condition does not affect controller operation, so
the unit should operate normally.
COMPRESSOR OVERLOAD (COL)/SAFETIES — Each
compressor is provided with either an internal line-break over-
current protector or an external overload protection module.
Each compressor control circuit also contains a compressor lock-
out board (CLO), high-pressure switch (HPS), low-pressure
switch (LPS), and evaporator freeze switch (FRZ). Except for
the internal line-break protection, these devices are wired in se-
ries to the contactor for each compressor. A pilot relay is wired in
parallel with the compressor contactor to determine when the
compressor contactor is energized/de-energized.
The compressor lockout board (CLO) is located in the unit
control box, wired in the control line for the compressor contac-
tor, and incorporates a current loop which monitors one leg of the
compressor power leads. This board is powered along with the
related compressor contactor.
Whenever the compressor current falls below a threshold lev-
el (i.e., compressor not operating) on an energized circuit, the
lockout board activates an on-board relay which opens power to
the compressor contactor and pilot relay. The pilot relay contacts
signal the controller with the compressor status. If any of the
safety devices described above opens, the compressor shutdown
sequence is started. In the event this occurs, the controller should
turn off this compressor, and start the next compressor in se-
quence. After a 5-minute period, the controller should restart this
compressor, and turn the other one off, as cooling demand re-
quires. If the “problem” compressor then operates for 10 minutes
of run time normally, the unit reverts to normal operation and
compressor sequencing. If not, and the same error occurs again,
this compressor should be shut down and replaced with the next
compressor, as before, and held off for 10 minutes. It should then
be restarted and the other compressor shut down, as before. If it
does not run successfully for 10 minutes of normal run time
again, it is shut down and replaced a third time. This time it is
held off for 15 minutes. If the "problem" compressor does not
operate successfully for the 10 minutes of normal run time this
third time, this compressor ONLY is shut down and locked out
for servicing. A compressor lockout alarm is generated and the
BACview alarm lamp is turned on.
HIGH-PRESSURE SWITCH (HPS) — This switch is located
in the discharge refrigerant line of each compressor, and is set
to open at pressures above 570 psig. It is wired in the 24-vac
control power line of the compressor contactor (in series with
the LPS and FRZ) and disables compressor operation when it
opens.
LOW-PRESSURE SWITCH (LPS) — The low-pressure
switch (LPS) is located in the suction refrigerant line of each
compressor, and is set to open at pressures below 27 psig. The
LPS is wired in the 24-vac control power line of the
compressor contactor (in series with the HPS and FRZ) and
disables compressor operation when it opens.
EVAPORATOR FREEZE SWITCH (FRZ) — The evaporator
freeze switch (FRZ) is a thermal disk type switch, mounted on
a return bend of the evaporator, refrigerant circuit for which
corresponds to each respective compressor, and is set to open at
temperatures below 28 F. The FRZ is wired in the 24-vac con-
trol power line of the compressor contactor (in series with the
LPS and HPS) and disables compressor operation when it
opens.
COMPRESSOR EXTERNAL OVERLOAD PROTEC-
TION MODULE — This board is provided with each com-
pressor that does not include internal line-break overload pro-
tection. When installed, this board is in the compressor termi-
nal box. This board activates at an over temperature setting,
and locks out operation of the compressor for 30 minutes; there
is no method to override or reset this timer. Due to this timing
function, please note that the compressor will not attempt to re-
start until the third attempt described above.
COMPRESSOR INTERNAL LINE-BREAK OVERLOAD
PROTECTION MODULE — Some compressors are built
with internal line-break protection. When the winding tempera-
ture exceeds the protector setting, the protector opens two of
the three power lines within the compressor. This protector
keeps the compressor locked out until the winding temperature
falls below the protectors reset temperature. There is no meth-
od to override or reset this protector, except by lowering the
winding temperature. Under some circumstances, the compres-
sor may not attempt to restart until the third attempt described
above.
ALARMS — There are four methods to annunciate alarms:
BACview alarm lamp, BACview alarm display, network com-
munications, or the discreet alarm output dry contacts. Alarms
are covered in detail in the Troubleshooting section.
TROUBLESHOOTING
Standard Diagnostic Features, Alarms and
Alarm Lamps —
Unit reset of alarm failure operation is
automatic when fault is cleared, except as noted.
SUPPLY AIR TEMPERATURE ALARM — If supply air
temperature input falls outside the range of 25 to 150 F, the
alarm output will close and the red alarm lamp will be lit. An
alarm with an ID of "sat_alarm" will be generated, but the unit
will operate normally.
SUPPLY AIR TEMPERATURE SENSOR FAILURE — If
the supply air temperature sensor fails the system will display a
supply-air temperature of 0.00° F, the compressor outputs will
be disabled, the alarm output will close and the red alarm lamp
will be lit. An alarm with an ID of "sat_sen_alarm" will be
generated.
DUCT STATIC PRESSURE ALARM — If the duct static
pressure input falls outside the range of 0.06 to 5.45 in. wg, the
alarm output will close and the red alarm lamp will be lit. An
alarm with an ID of "dsp_alarm" will be generated, but the unit
will operate normally.
DUCT STATIC PRESSURE SENSOR FAILURE — If the
duct static pressure sensor fails, the system will display 0.00 in.
wg, the controller outputs will be forced off, the alarm output
will close and the red alarm lamp will be lit. An alarm with an
ID of "dsp_sens_alarm" will be generated.
DUCT HIGH STATIC INPUT (DHS) — This factory-
installed air switch provides over pressurization protection for
the ductwork. The switch is a normally open switch, with ad-
justable manual setting (range is 1 to 5 in. wg with a default of
3.0 in. wg). Upon switch closure, the controller outputs will be
forced off, the alarm output will close and the red alarm lamp