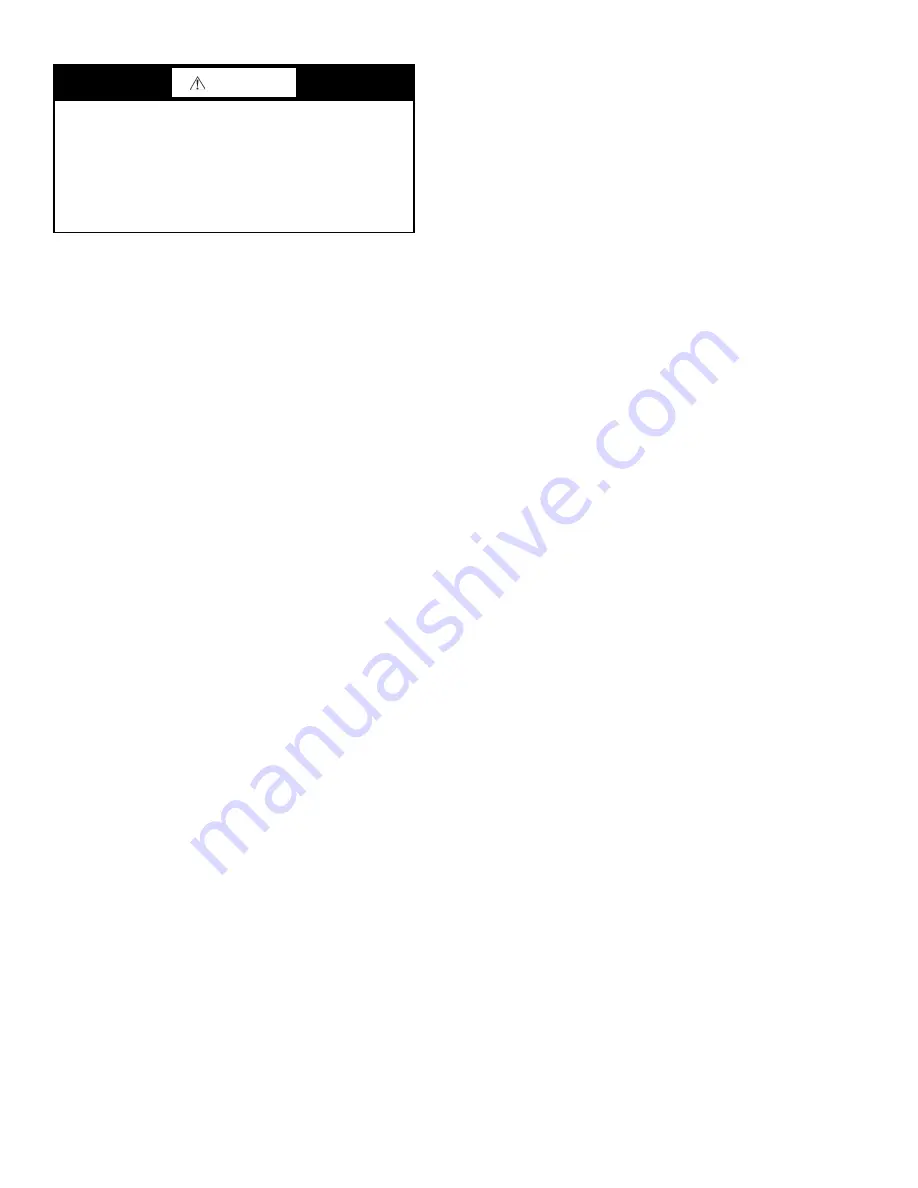
2
GENERAL
This publication contains Controls, Operation and Trouble-
shooting information for the 50XJ units. The Omnizone™
packaged units are self-contained, water-cooled indoor units
for use in VAV (variable air volume) applications. Units are
equipped with Carrier multi-protocol controls. Refer to the unit
Installation Instructions for unit layout.
MAJOR SYSTEM COMPONENTS
Controller Processor 6126 (PCB1) —
The cen-
tral processing unit for the Omnizone system control is the UC
Multi-Protocol XP. The controller provides general purpose
HVAC (Heating, Ventilation and Air Conditioning) control and
monitoring capability in a stand-alone or network environment
using closed-loop, direct digital controls. The controller has
been pre-programmed to work in either stand-alone or
BACnet*, MODBUS†, or Johnson N2 network system instal-
lations. The controller will also operate on a LonWorks** net-
work with an accessory LON-OC board installed.
The controller is designed to provide heating and cooling
control, loop control, scheduling, and custom programming.
The main processor provides 24 field points (12 universal in-
puts, 6 relay outputs, and 6 analog outputs). Additional points
are provided by the I/O (input/output) modules. Table 1 lists
the control inputs and outputs for all modules.
Specifications for the Multi-Protocol Controller may be
found in the Open System literature.
I/O Flex Module 8160 (PCB2) —
This input/output
module is factory-installed and allows additional factory and
field points (16 inputs and 8 outputs).
The module provides the following inputs: outdoor-air tem-
perature (accessory), leaving-water temperature (accessory),
tower sump temperature (accessory), mixed-air or return-air
temperature (factory), water economizer freeze sensor (option)
or freeze thermostat (accessory), entering water temperature
(option), enthalpy sensor (accessory), filter status switch (op-
tion), phase rotation monitor (option), condenser water flow
switch (option), and compressor status (factory).
This module provides the following field digital outputs:
heat interlock (HIR), VAV terminal control (TRMCT), ventila-
tion request (VENTR), VAV terminal open (TRMOP), pump
request, tower request, and external dehumidification.
Local Interface Display —
The BACview interface
display is mounted on the front of the 50XJ units. A number of
user-adjustable features are entered/changed using the display
keypad. These features described in detail in the Control and
Display section of this manual.
Control Module Communication —
When power is
applied to the Omnizone™ system control panel, green power
LED (light-emitting diode) lights. Once the control program
initializes, the green RUN LED on each module should flash
on/off about twice a second and the red error (ERR) LED
should be off. The green Tx/Rx LEDS flicker when data is
communicated over the network. The green Tx/Rx LEDS near
the Xnet remote expansion port flicker when the main board
and the expansion board are communicating.
PCB Addresses —
Rotary switch 1 (SW1) is used to set
each controller’s address, as well as the input/output module
address. Individual jumpers on each board are used to config-
ure the input point type. For more information, refer to Table 1
and the Optional and Field-Installed Accessory Sensors/Devic-
es section.
Optional and Field-Installed Accessory Sensors/
Devices —
These units can be ordered with options and ac-
cessories that add functionality and control. These options and
accessories are used as described below.
NOTE: The control software includes all PCB1 and PCB2
functions, and most of the sensors/devices associated with
those functions are factory installed. However, some sensors/
devices must be field-connected to the proper terminal.
REMOTE OCCUPANCY CONTROL (PCB1) — This con-
trol is a field located switch, controller or timer input which,
when activated, tells system when to switch from unoccupied
to occupied mode.
When in occupied mode, the unit turns on the supply fan
and controls supply fan speed to maintain a duct static set point
measured at the duct static pressure sensor (DSP). The unit
operates to provide conditioning to a set point. When in
unoccupied mode, the unit provides no cooling/heating, or
controls to a ‘setback’ set point.
FIRE ALARM (PCB1) — The fire alarm is a normally
closed, dry contact input that causes the controller to shut the
system down in the event of a fire.
CONDENSER WATER FLOW SWITCH (PCB2) — This
flow switch is located in the unit waterline to ensure that there
is water flow before allowing the unit to start the compres-
sor(s). Compressor operation and economizer cooling is dis-
abled when no flow is detected. These remain disabled until
water flow is again detected.
The factory-installed water flow switch on the 50XJ unit is
a thermal dispersion type switch located inside the unit cabinet.
HEAT INTERLOCK OUTPUT (PCB2) — This output is ac-
tivated whenever heating is activated, commanding the VAV
dampers to operate in heating control mode.
NOTE: In order for this output to function, the terminal
occupied output must also be on.
TERMINAL CONTROL (PCB2) — Terminal control is acti-
vated to command VAV dampers to control to the cooling set
point. Terminal control must be on along with heat interlock for
heating set point control to function.
EXTERNAL RESET INPUT (PCB1) — This modulating
input (0 to 10 vdc) allows remote adjustment (upward) of the
supply air temperature (SAT) sensor set point. The default ex-
ternal reset input setting is 55 F. This variable input can raise
the set point by up to 20 F for a full-range input signal or to any
point in between.
WATER ECONOMIZER COIL (PCB2) — This
factory-in-
stalled option contains a water-to-air coil, two (2) electronic
motorized water valves, and related piping. Control of the water
economizer also requires a mixed/return air temperature sensor,
an entering water temperature sensor and an economizer freeze-
stat sensor or switch.
The electronic motorized water valves are each controlled
by the unit controller via separate 2 to 10 vdc variable signals
to define variable valve position.
CAUTION
DO NOT re-use compressor oil or any oil that has been
exposed to the atmosphere. Dispose of oil per local codes
and regulations. DO NOT leave refrigerant system open to
air any longer than the actual time required to service the
equipment. Seal circuits being serviced and charge with
dry nitrogen to prevent oil contamination when timely
repairs cannot be completed. Failure to follow these proce-
dures may result in damage to equipment.
* Sponsored by ASHRAE (American Society of Heating, Refrigerat-
ing and Air-Conditioning Engineers).
† Registered trademark of Schneider Electric.
** Registered trademark of Echelon Corporation. Requires additional
hardware card.