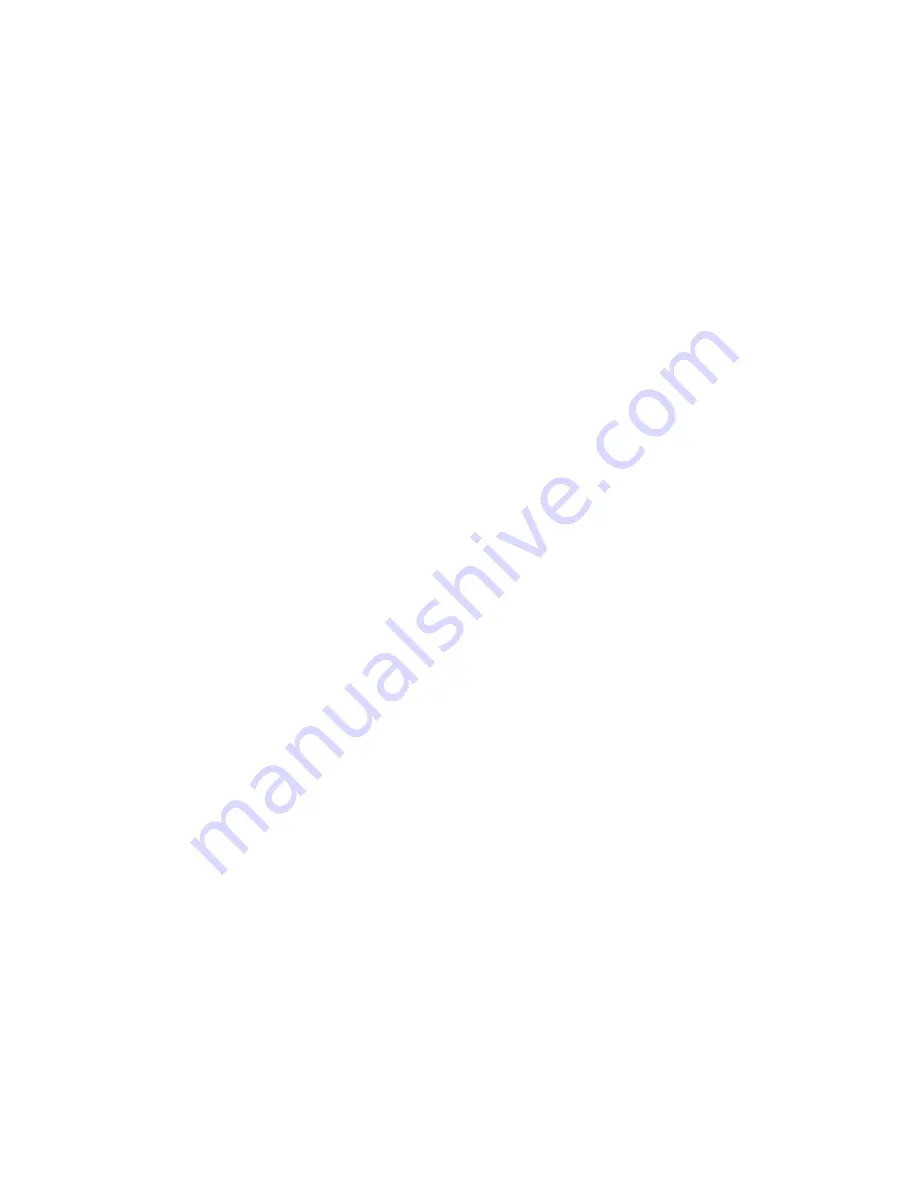
5
For any parts that need to be removed, use a mini tubing cutter.
Perform phos-copper brazing on all field-made connections while
protecting adjacent joints from heat.
REFRIGERANT LINE SIZING
Sizing depends on length of lines between various sections of the
refrigerant system. Consider the amount of liquid lift and drop in
the system as well as proper compressor oil return. Consult Carrier
System Design Manual, Part 3 for proper piping sizes and design.
PRESSURE RELIEF
The ASHRAE Standard 15, Safety Code for Mechanical Refriger
-
ation states: ‘‘Every refrigerating system shall be protected by a
pressure relief device or some other means designed to safely re
-
lieve pressure due to fire or other abnormal conditions.’’ Since
09XC condensers do not have pressure relief devices, one must be
field supplied and installed either before the liquid line service
valve or inside the 09XC unit. Each circuit must have its own
pressure relief.
If desired, the pressure relief requirement can also be satisfied by
installing a fusible plug in the liquid line. To do so, install a tee in
the liquid line with a
1
⁄
4
-in. NPT fitting on the tee side, and install a
fusible plug (part no. EK02KK105 or similar). The temperature
rating of the fusible plug should be between 205°F and 220°F
(96°C and 104°C). If a service valve is used on the liquid line, be
sure that both the piping system and the condenser are protected
for relief if all service valves are closed. Note that if the condenser
is located indoors, requirements for venting the fusible plug to the
outdoors may apply. Consult local code requirements.
REFRIGERANT RECEIVER
A refrigerant receiver is not furnished with 09XC condensers and
is not recommended for normal applications as its use is detrimen
-
tal to adequate refrigerant storage volume and desired effects of
subcooling.
COIL CONNECTIONS
See Table 2 for the necessary connections.
LIQUID LIFT
Amount of liquid lift available before refrigerant flashing occurs
depends on amount of liquid subcooling in the system.
All 09XC condensers have positive subcooling when applied with
optimum charge. With subcooling, it is possible to overcome an
appreciable pressure drop and/or static head pressure (due to ele
-
vation of the liquid metering device above the condenser when
condenser is below evaporator coil).
When 09XC condensers are applied with minimum charge, they
do not provide positive subcooling. If subcooling is required, it
must be obtained by external means such as a liquid suction inter
-
changer.
It is recommended that the evaporator be either at the same level
as the condenser or lower than the condenser when minimum
charge is used.
SWEAT CONNECTIONS
Connections are made outside the unit, and piping enters from the
right side. For ease in brazing, it is recommended that all internal
solder joints be made before unit is placed in its final position. See
50XCR (or other compressor-bearing unit) base unit installation
instructions for proper line sizing and piping procedures.
FIELD PIPING
For 09XC remote installation, select pipe sizes according to length
from Table 3. Use refrigerant grade piping. If tubing size is other
than unit connection sizes, use adapter fittings.
Refer to 50XCR (or other compressor-bearing unit) base unit in
-
stallation instructions to determine refrigerant charge adjustment
for remote and special piping applications.
NOTE: When installing 09XC units in systems, add charge for
other components (i.e., filter drier, moisture indicator, etc.) to de
-
termine system charge quantity. Record charge.
CHECK VALVE
When the 09XC condenser is installed with the condenser located
above the compressor evaporator, it is recommended that a field-
supplied check valve be installed on the hot gas discharge line.
This prevents refrigerant which condenses in the discharge line
during the off cycle from draining back into the compressor. In
-
stall the check valve at the compressor line before the line goes up
to the condenser. Check valve part no. EC37BP183 or similar may
be used.
Step 4 — Install Ductwork
The 09XC unit is designed for use either with or without
ductwork. If ductwork is used, care must be taken to eliminate air
recirculation. Recirculation can be minimized by discharging
through an extension elbow. When properly designed, single de
-
flection discharge louvers can be applied to ductwork and to the
condenser air discharge. Fixed rain louvers over discharge outlets
can cause excessive recirculation and nuisance high pressure
switch cutouts. Obstructions closer than 10 ft to the discharge air
pattern can also cause significant recirculation. See Fig. 6 for
ductwork installation to prevent recirculation of air.
CONDENSER AIR DUCT
The condenser supply and discharge air duct should be as short as
possible. The cross section area of the duct should be the same as
the face area of the unit openings. For units with multiple fans, “a
pair of pants” duct configuration should be used in accordance
with the System Design Manual and ASHRAE guidelines; in
some instances, settling media may be required to ensure uniform
airflow. Ductwork should be insulated to prevent moisture con
-
densation on the unit panels during cold weather.
Insulate as follows:
1. If metal ductwork is used, insulation may be applied on the
inside of the duct. This installation should be extended to
cover the inside of the duct flanges. It is necessary to insulate
the inside of the ducts at the duct flanges to reduce heat loss
from the metal cabinet by conduction through the duct
flanges and into the cold duct. Interior insulation allows the
metal duct to approach room temperature. It also prevents
condensation from forming and collecting under the insula
-
tion which will occur with exterior duct insulation.
NOTE: Fiberglass duct board may also be used if permitted by lo
-
cal codes.
2. If insulation is applied to the outside of the metal duct, the
inside must be insulated for a length of 10 in. from the unit
(including the duct flanges) or up to the flexible duct vapor
barrier on the outside, which must be tightly sealed to prevent
condensation under the insulation.
Step 5 — Insulate the Unit
The 09XC units are not insulated. If the unit will be operated
during cold weather and the equipment room is not at outdoor
temperatures, the unit cabinet should be insulated to prevent con
-
densation. Insulate the unit in the same manner as the ductwork in
-
sulation described in Condenser Air Duct section above.