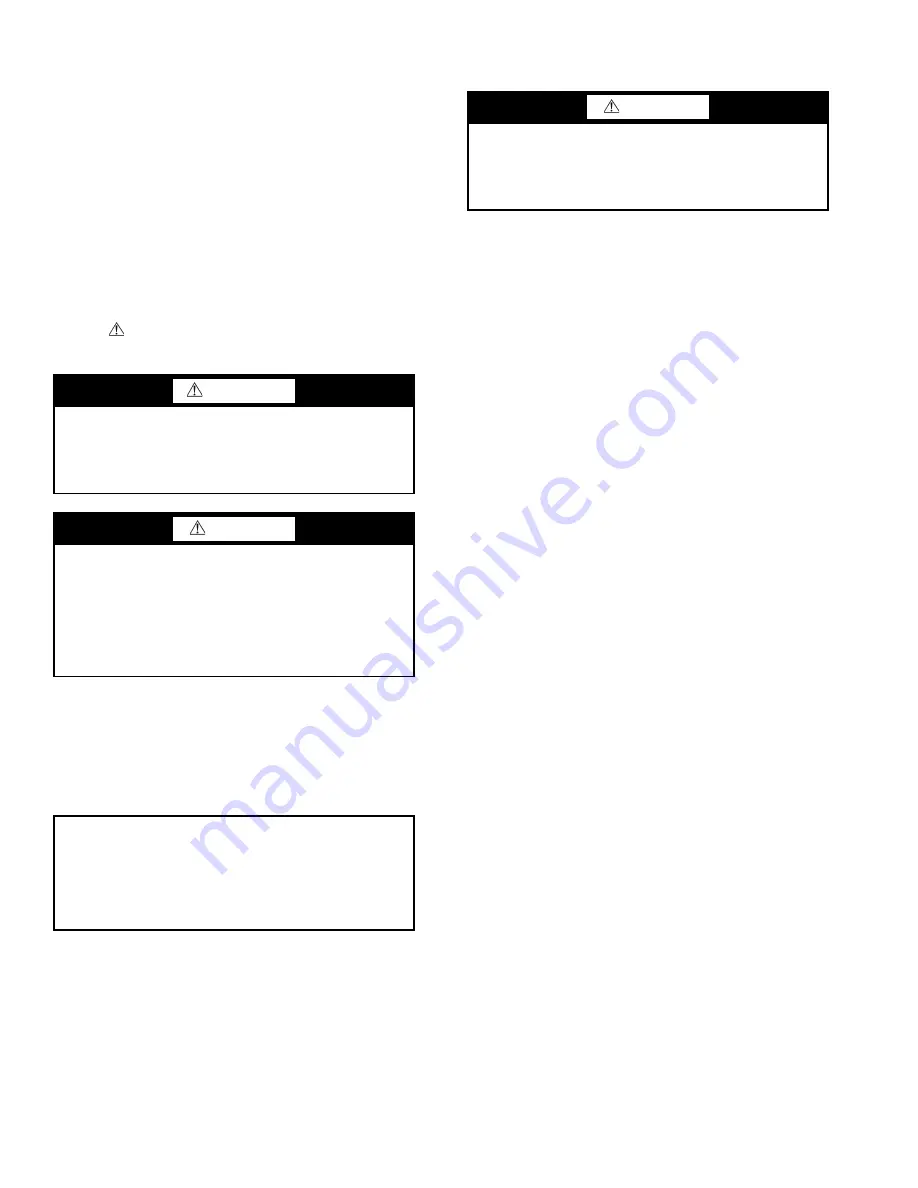
2
accessories when modifying this product. Refer to the
individual instructions packaged with the kits or accessories
when installing.
Follow all safety codes. Wear safety glasses and work
gloves. Use quenching cloth for brazing operations. Have fire
extinguisher available. Read these instructions thoroughly and
follow all warnings or cautions attached to the unit. Consult
local building codes and the National Electrical Code (NEC)
for special installation requirements.
Understand the signal words — DANGER, WARNING,
and CAUTION. DANGER identifies the most serious hazards
which will result in severe personal injury or death. WARN-
ING signifies hazards that could result in personal injury or
death. CAUTION is used to identify unsafe practices, which
would result in minor personal injury or product and property
damage.
Recognize safety information. This is the safety-alert
symbol (
). When you see this symbol on the unit and in
instructions or manuals, be alert to the potential for personal
injury.
GENERAL
This Installation and Start-Up Instructions literature is for
Aquazone™ water source heat pump systems with Puron re-
frigerant.
Water source heat pumps (WSHPs) are single-package hori-
zontally and vertically mounted units with electronic controls
designed for year-round cooling and heating.
INSTALLATION
Step 1 — Check Jobsite —
Installation, operation and
maintenance instructions are provided with each unit. Before
unit start-up, read all manuals and become familiar with the
unit and its operation. Thoroughly check out the system before
operation. Complete the inspections and instructions listed
below to prepare a unit for installation. See Table 1 for unit
physical data.
Horizontal units are designed for indoor installation only.
Be sure to allow adequate space around the unit for servicing.
See Fig. 1 for overall unit dimensions. Refer to Fig. 2 for an ex-
ample of a typical horizontal installation.
Step 2 — Check Unit —
Upon receipt of shipment at
the jobsite, carefully check the shipment against the bill of
lading. Make sure all units have been received. Inspect the car-
ton or crating of each unit, and inspect each unit for damage.
Ensure the shipping company makes proper notation of any
shortages or damage on all copies of the freight bill. Concealed
damage not discovered during unloading must be reported to
the shipping company within 15 days of receipt of shipment.
NOTE: It is the responsibility of the purchaser to file all
necessary claims with the shipping company.
1. Verify unit is correct model for entering water tempera-
ture of job.
2. Be sure that the location chosen for unit installation pro-
vides ambient temperatures maintained above freezing.
Well water applications are especially susceptible to
freezing.
3. Be sure the installation location is isolated from sleeping
areas, private offices and other acoustically sensitive
spaces.
NOTE: A sound control accessory package may be used
to help eliminate sound in sensitive spaces.
4. Check local codes to be sure a secondary drain pan is not
required under the unit.
5. Be sure unit is mounted at a height sufficient to provide
an adequate slope of the condensate lines. If an appropri-
ate slope cannot be achieved, a field-supplied condensate
pump may be required.
6. Provide sufficient space for duct connection.
7. Provide adequate clearance for filter replacement and
drain pan cleaning. Do not allow piping, conduit, etc. to
block filter access.
8. Provide sufficient access to allow maintenance and
servicing of the fan and fan motor, compressor and coils.
Removal of the entire unit from the closet should not be
necessary.
9. Provide an unobstructed path to the unit within the closet
or mechanical room. Space should be sufficient to allow
removal of unit if necessary.
10. Provide ready access to water valves and fittings, and
screwdriver access to unit side panels, discharge collar,
and all electrical connections.
11. Where access to side panels is limited, pre-removal of the
control box side mounting screws may be necessary for
future servicing.
STORAGE — If the equipment is not needed for immediate
installation upon its arrival at the jobsite, it should be left in its
shipping carton and stored in a clean, dry area of the building
or in a warehouse. Units must be stored in an upright position
at all times. If carton stacking is necessary, stack units a
maximum of 3 high. Do not remove any equipment from its
shipping package until it is needed for installation.
PROTECTION — Once the units are properly positioned on
the jobsite, they must be covered with either a shipping carton,
vinyl film, or an equivalent protective covering. Open ends of
pipes stored on the jobsite must be capped. This precaution is
WARNING
Electrical shock can cause personal injury and death. Shut
off all power to this equipment during installation. There
may be more than one disconnect switch. Tag all discon-
nect locations to alert others not to restore power until work
is completed.
CAUTION
This system uses R-410A, which has higher pressures than
R-22 and other refrigerants. No other refrigerant may be
used in this system. Suction tubing design pressure is
3068 kPa and liquid tubing design pressure is 4522 kPa.
Failure to use gage set, hoses, and recovery systems
designed to handle R-410A refrigerant may result in per-
sonal injury and equipment damage. If unsure about equip-
ment, consult the equipment manufacturer.
IMPORTANT: The installation of water source heat pump
units and all associated components, parts, and accessories
which make up the installation shall be in accordance with
the regulations of ALL authorities having jurisdiction and
MUST conform to all applicable codes. It is the responsi-
bility of the installing contractor to determine and comply
with ALL applicable codes and regulations.
CAUTION
To avoid equipment damage, do not use these units as a
source of heating or cooling during the construction pro-
cess. The mechanical components and filters used in these
units quickly becomes clogged with construction dirt and
debris which may cause system damage.
Содержание AQUAZONE 50HQP072
Страница 33: ......