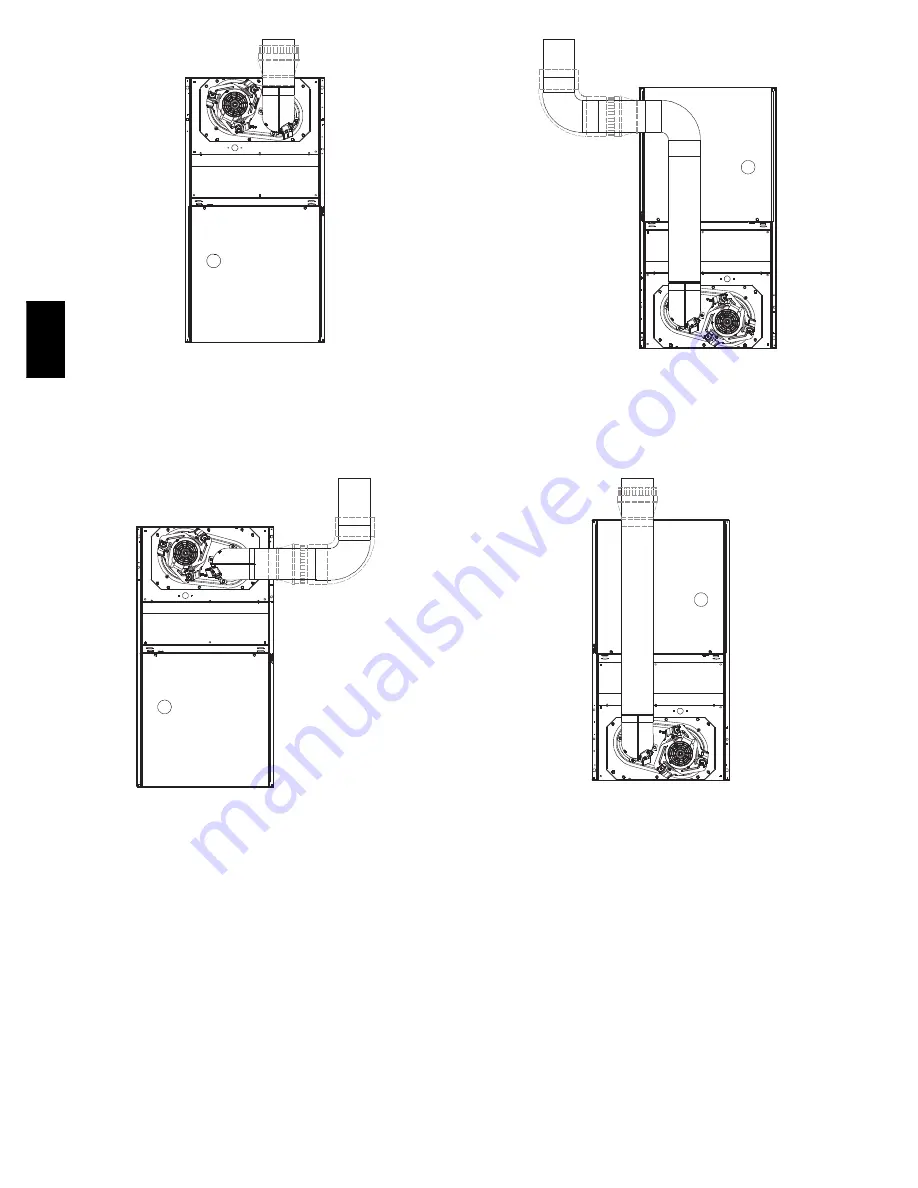
32
SEE NOTES: 1,2,4,7,8,9
on the page following
these figures
A03208
Fig. 34 -- Upflow Application--Vent Elbow Up
SEE NOTES: 1,2,3,4,7,8,9
on the pages following
these figures
A03209
Fig. 35 -- Upflow Application--Vent Elbow Right
SEE NOTES:1,2,3,4,5,7,8,9
on the page following
these figures
A03210
Fig. 36 -- Downflow Application--Vent Elbow Up then Left
SEE NOTES: 1,2,4,5,7,8,9
on the page following
these figures
A03211
Fig. 37 -- Downflow Application--Vent Elbow Up
58D
L