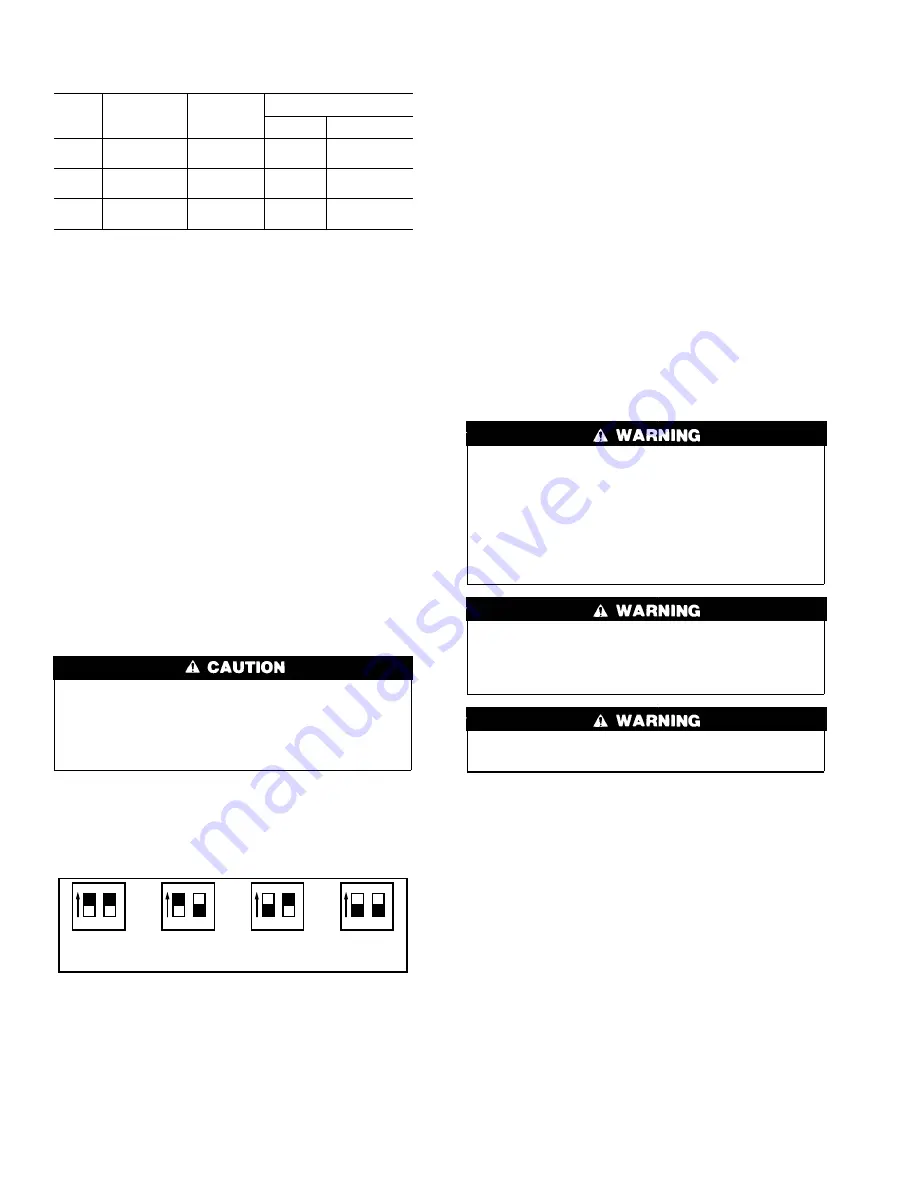
On a new installation, air entrapped in oil line leading from
tank to nozzle must be thoroughly purged in order to prevent
excessive after drip. The oil pump is provided with a special
fitting which allows purging of any air between tank and oil
pump. The proper procedure for performing this operation is
as follows:
a. Place a piece of clear plastic 1/4-in. diameter tubing over
purge fitting on oil pump.
b. Start oil burner, then open purge fitting and allow burner to
run until purge tube is completely free of air bubbles.
c. Tighten purge fitting. Allow oil to run to nozzle and fire
burner.
d. If purging takes longer than 30 sec and no flame has been
established, burner stops. Push reset button on top of
primary control to restart burner.
e. For detailed information on operation of primary control,
refer to instructions included with furnace.
Step 3—Fan Adjustment Check
This furnace is equipped with a 3-speed direct-drive motor to
deliver a temperature rise (between return and supply plenums)
within range specified on rating plate at external duct static
pressure noted on rating plate.
When operating furnace in heating mode, static pressure and
temperature rise (supply-air temperature minus return-air
temperature) must be within those limits specified on rating
label. Failure to follow this warning could lead to severe
furnace damage.
Adjust fan speed so that temperature rise is within rise range
specified on rating plate. Consult wiring diagram for speed
changes on direct-drive motor.
To adjust fan off time, set DIP switches on control board to obtain
desired timing. (See Fig. 1.)
Step 4—Limit Control Check
After furnace has been in operation for at least 15 minutes, restrict
return-air supply by blocking filters or closing return registers and
allow furnace to shut down on high limit. The burner should shut
off, and main blower should continue to run.
Remove restriction, and burner should come back on in a few
minutes.
Step 5—For Year-Round Air Conditioning
This furnace is designed for use in conjunction with cooling
equipment to provide year-round air conditioning. The blower has
been sized for both heating and cooling, however, fan motor speed
may need to be changed to obtain necessary cooling airflow.
Step 6—Heating
The blower speed is factory set to deliver required airflow at
normal duct static pressure.
Step 7—Cooling
The blower speed may be field adjusted to deliver required airflow
for cooling application. (See Table 5.)
Step 8—Constant Blower Switch
This furnace is equipped with a constant low-speed blower option.
Whenever room thermostat is not calling for heating or cooling,
blower runs on low speed in order to provide air circulation. If
constant blower option is not desired, the rocker switch on side of
control box may be used to turn off constant speed.
MAINTENANCE
The ability to properly perform maintenance on this equip-
ment requires certain expertise, mechanical skills, tools, and
equipment. If you do not possess these, do not attempt to
perform any maintenance on this equipment other than those
procedures recommended in the User’s Manual. FAILURE
TO FOLLOW THIS WARNING COULD RESULT IN
POSSIBLE DAMAGE TO THIS EQUIPMENT, SERIOUS
PERSONAL INJURY, OR DEATH.
Before performing any service functions, unless operations
specifically require power to be on, make sure all utilities are
turned off upstream of appliance. Failure to comply with this
warning will cause a fire hazard and/or bodily harm.
To avoid personal injury, make sure electrical supply power
is off before servicing.
Step 1—General
In order to keep this furnace in good operating condition and to
maintain its warranty, the furnace MUST be serviced on an annual
basis. This servicing includes a nozzle change, a burner inspection,
a visual check of tube passages through flue outlet and cleanout
ports, and a visual inspection of combustion chamber when burner
is removed.
Depending on above inspection, service could also include a
cleaning and vacuuming of heat exchanger tubes and possibly the
heat exchanger drum section.
Removal of any heat exchanger components which are sealed by
gaskets requires replacement of gasket.
→
Table 4—Burner, Nozzle, and Pump
Pressure Chart
UNIT
SIZE
FIRING
RATE
GAL/HR (US)
PUMP
PRESSURE
(PSIG)
BECKETT OIL BURNER
Model
Nozzle
105-12
0.76
103
AFG
0.75 gph
70° Hollow
125-16
0.90
100
AFG
0.90 gph
70° Hollow
155-20
1.12
104
AFG
1.10 gph
70° Hollow
Fig. 1—Fan Off Time DIP Switch Settings
(Black Box Represents Switch Position)
A95115
1
2
60 Sec
1
2
90 Sec
DELAY OFF DIP SWITCH SETTINGS
1
2
1
2
1
2
120 Sec
1
2
150 Sec
6
→
→