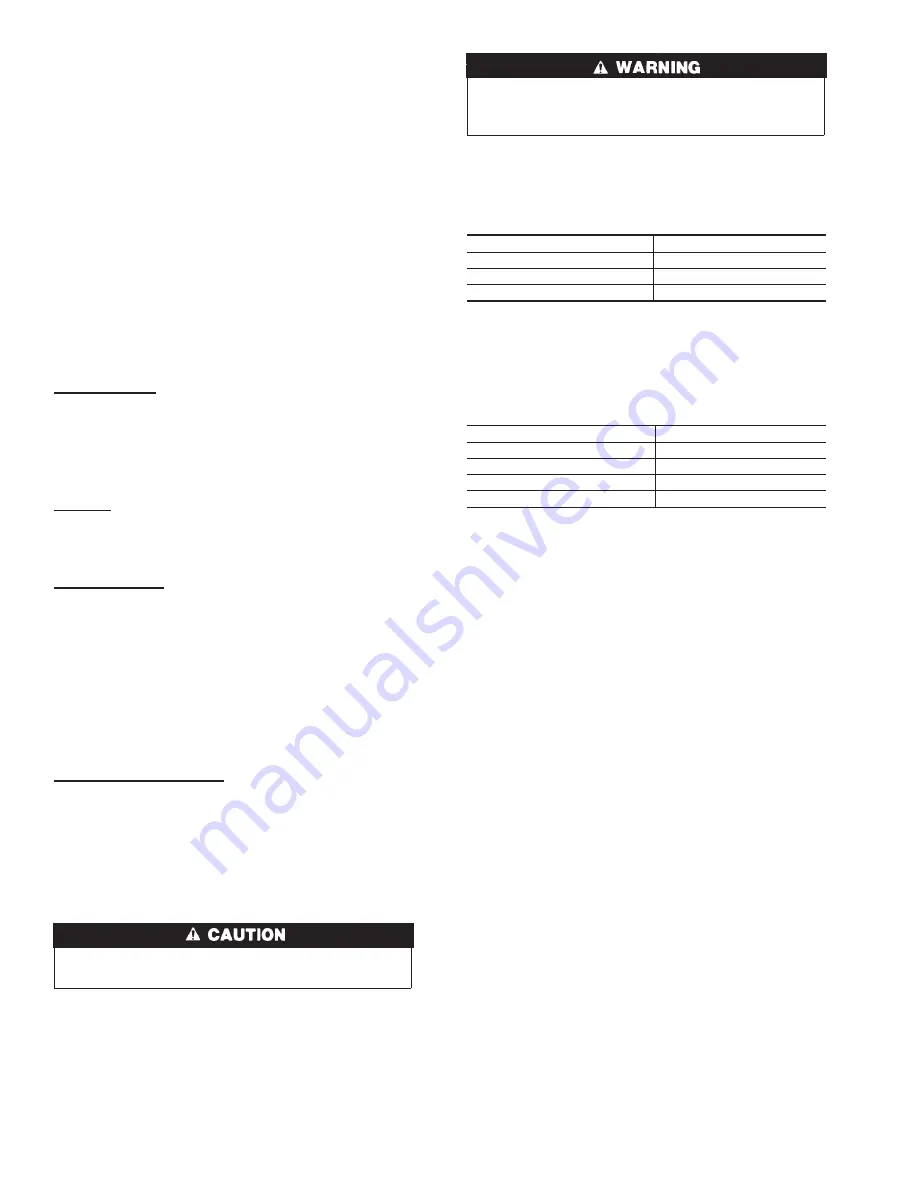
NOTE:
Adjustment of the refrigerant charge is not required
unless the unit is suspected of not having the proper R-410A
charge. The charging label and the tables shown refer to system
temperatures and pressures.
A refrigerant charging chart label is attached to the outside of the
compressor access door. The chart includes the required suction
line temperature at given suction line pressures and outdoor
ambients.
An accurate superheat, thermocouple- or thermistor-type ther-
mometer, a sling psychrometer, and a gage manifold are required
when using the superheat charging method for evaluating the unit
charge.
Do not use mercury or small dial-type thermometers
because they are not adequate for this type of measurement.
IMPORTANT:
When evaluating the refrigerant charge, an indi-
cated adjustment to the specified factory charge must always be
very minimal. If a substantial adjustment is indicated, an abnormal
condition exists somewhere in the cooling system, such as insuf-
ficient airflow across either coil or both coils.
Refrigerant charge
The amount of refrigerant charge is listed on the unit nameplate.
Refer to the Refrigeration Service Techniques Manual, Refriger-
ants section.
Unit panels must be in place when unit is operating during
charging procedures.
No charge
Use standard evacuating techniques. After evacuating system,
weigh in the specified amount of refrigerant (refer to system data
plate).
Low charge cooling
Measure outdoor ambient using Cooling Charging Charts (Figs.
15-19). Vary refrigerant until the conditions of the chart are met.
Note that charging charts are different from type normally used.
Charts are based on charging the units to correct superheat for the
various operating conditions. Accurate pressure gage and tempera-
ture sensing devices are required. Connect the pressure gage to the
service port on the suction line. Mount the temperature sensing
device on the suction line and insulate it so that the outdoor
ambient does not effect the reading. Indoor air CFM must be
within the normal operating range of the unit.
To use cooling charging charts
Take the outdoor ambient temperature and read the suction
pressure gage. Refer to the chart to determine what the suction
temperature should be.
NOTE:
If the problem causing the inaccurate readings is a
refrigerant leak, refer to Check for Refrigerant Leaks section.
INDOOR AIRFLOW AND AIRFLOW ADJUSTMENTS
For cooling operation, the recommended airflow is 350 to 450
cfm for each 12,000 Btuh of rated cooling capacity.
Table 4 shows cooling airflows at various external static pressures.
Refer to these tables to determine the airflow for the system being
installed.
NOTE:
Be sure that all supply- and return-air grilles are open,
free from obstructions, and adjusted properly.
Disconnect electrical power to the unit before changing
blower speed. Electrical shock can cause serious injury or
death.
Airflow can be changed by changing the lead connections of the
blower motor.
All 50GL units are factory wired for low speed and may need to be
wired for medium or high speed in the field.
FOR 208/230-V — The motor leads are color-coded as follows:
3-SPEED
2-SPEED
black = high speed
black = high speed
blue = medium speed
-
red = low speed
red = low speed
To change the speed of the blower motor (BM), remove the fan
motor speed leg lead from the blower relay (BR). This wire is
attached to terminal BM for 3-phase units. To change the speed,
remove and replace with lead for desired blower motor speed.
Insulate the removed lead to avoid contact with chassis parts.
FOR 460-V GE MOTORS — The motor leads are color coded as
follows:
3-SPEED
2-SPEED
black = high
black = high
violet = jumper
blue = jumper
orange = medium
-
red = low
red = low
To change the speed of the blower motor (BM), remove fan motor
speed lead from the blower relay (BR) and replace with the lead
for the desired blower motor speed. The motor speed lead is
attached to terminal BM. For low and medium speeds black must
be connected to the jumper wire.
Insulate removed lead end to
avoid contact with chassis parts.
To select high speed on 460-v GE
motors, separate the black female quick connect (QC) from the
jumper lead male quick connect (QC) and connect the black lead
to the BR. Insulate the jumper to avoid contact with any chassis
parts.
COOLING SEQUENCE OF OPERATION — With the room
thermostat SYSTEM switch in the COOL position and the FAN
switch in the AUTO position, the cooling sequence of operation is
as follows:
When the room temperature rises to a point that is slightly above
the cooling control setting of the thermostat, the thermostat
completes the circuit between thermostat terminal R to terminals Y
and G. These completed circuits through the thermostat connect
contactor coil (C) (through unit wire Y) and blower relay coil
(TDR) (through unit wire G) across the 24-v secondary of
transformer (TRAN).
The normally open contacts of energized contactor (C) close and
complete the circuit through compressor motor (COMP) to con-
denser (outdoor) fan motor (OFM). Both motors start instantly.
The set of normally open contacts of energized relay TDR close
and complete the circuit through evaporator blower (indoor) fan
motor (IFM).
NOTE:
Once the compressor has started and then has stopped, it
should not be started again until 5 min have elapsed.
The cooling cycle remains ‘‘on’’ until the room temperature drops
to point that is slightly below the cooling control setting of the
room thermostat. At this point, the thermostat ‘‘breaks’’ the circuit
between thermostat terminal R to terminals Y and G. These open
circuits deenergize contactor coil C and relay coil TDR. The
condenser and compressor motors stop. After a 30-sec delay, the
blower motor stops. The unit is in a ‘‘standby’’ condition, waiting
for the next ‘‘call for cooling’’ from the room thermostat.
14