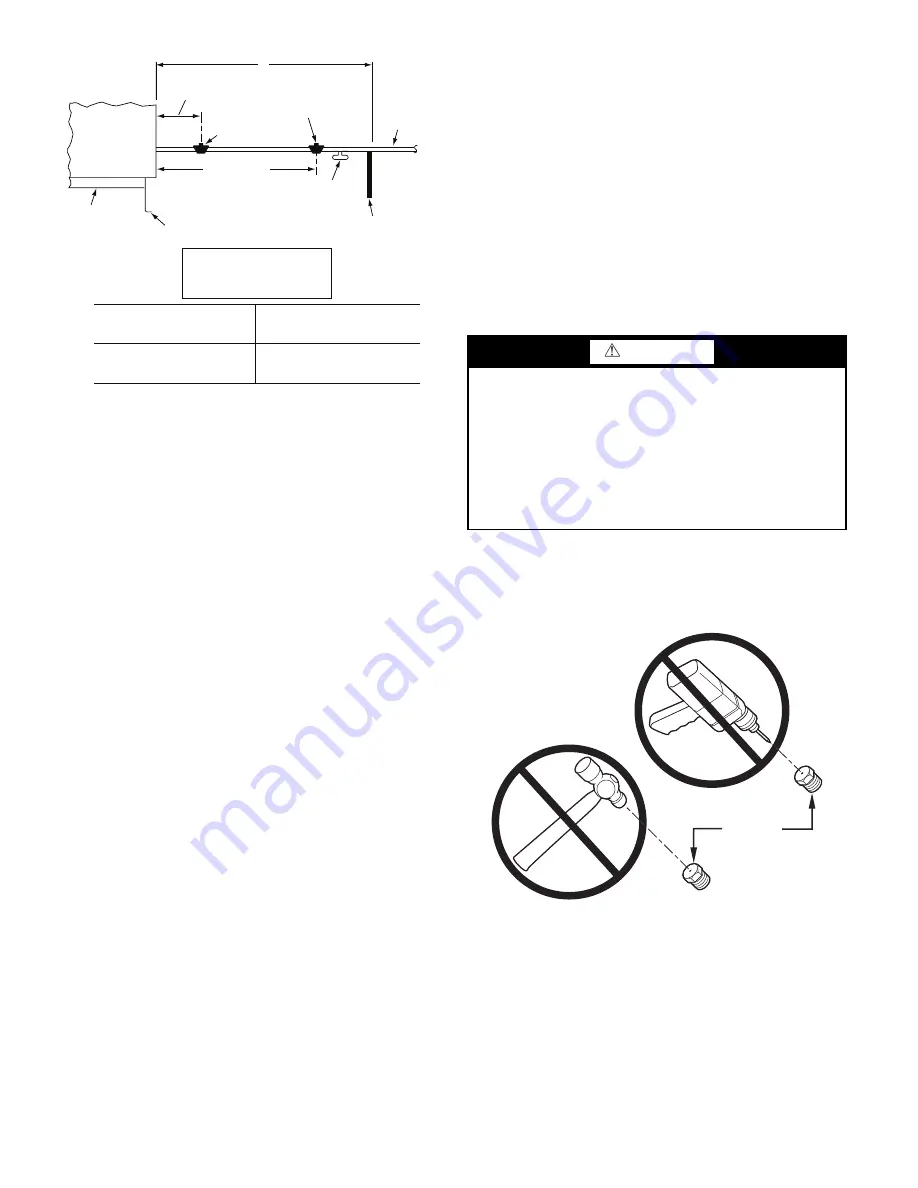
26
Fig. 28 — Gas Piping Guide
FACTORY-OPTION THRU-BASE CONNECTIONS
Electrical Connections
Knockouts are located in the control box area. Remove the appro-
priate size knockout for high voltage connection. Use the field
supplied connector depending on wiring or conduit being utilized.
Remove the
7
/
8
-in. (22 mm) knockout and appropriate connector
for low voltage wiring. If non-unit powered convenience outlet is
being utilized, remove the
7
/
8
-in. (22 mm) knockout and utilize ap-
propriate connector for 115 volt line. See “Step 11 — Make Elec-
trical Connections” on page 27 for details.
Gas Connections
Remove the knockout in the base pan and route
3
/
4
-in. gas line up
through the opening. Install an elbow and route gas line through
opening in panel after first removing plastic bushing. Install a gas
shut off followed by a drip leg and ground-joint union. Route gas
line into gas section through the grommet (Part #: KA56SL112) at
the gas inlet and into the gas valve. See Fig. 26 and Table 7. If a
regulator is installed, it must be located 4 feet (1.22 meters) from
the flue outlet.
Some municipal codes require that the manual shutoff valve be lo-
cated upstream of the sediment trap. See Fig. 28 for typical piping
arrangements for gas piping that has been routed through the side-
wall of the base pan.
When installing the gas supply line, observe local codes pertaining
to gas pipe installations. Refer to the NFPA 54/ANSI Z223.1
NFGC latest edition (in Canada, CAN/CSA B149.1). In the ab-
sence of local building codes, adhere to the following pertinent
recommendations:
1. Avoid low spots in long runs of pipe. Grade all pipe
1
/
4
-in. in
every 15 ft (7 mm in every 5 m) to prevent traps. Grade all
horizontal runs downward to risers. Use risers to connect to
heating section and to meter.
2. Protect all segments of piping system against physical and
thermal damage. Support all piping with appropriate straps,
hangers, etc. Use a minimum of one hanger every 6 ft
(1.8 m). For pipe sizes larger than
1
/
2
-in., follow recommen-
dations of national codes.
3. Apply joint compound (pipe dope) sparingly and only to
male threads of joint when making pipe connections. Use
only pipe dope that is resistant to action of liquefied petro-
leum gases as specified by local and/or national codes. If
using PTFE (Teflon) tape, ensure the material is Double
Density type and is labeled for use on gas lines. Apply tape
per manufacturer’s instructions.
4. Pressure-test all gas piping in accordance with local and
national plumbing and gas codes before connecting piping to
unit.
NOTE: Pressure test the gas supply system after the gas supply
piping is connected to the gas valve. The supply piping must be
disconnected from the gas valve during the testing of the piping
systems when test pressure is in excess of 0.5 psig (3450 Pa). Pres-
sure test the gas supply piping system at pressures equal to or less
than 0.5 psig (3450 Pa). The unit heating section must be isolated
from the gas piping system by closing the external main manual
shutoff valve and slightly opening the ground-joint union.
Check for gas leaks at the field-installed and factory-installed
gas lines after all piping connections have been completed. Use
soap-and-water solution (or method specified by local codes
and/or regulations).
NOTE: If orifice hole appears damaged or it is suspected to have
been redrilled, check orifice hole with a numbered drill bit of cor-
rect size. Never redrill an orifice. A burr-free and squarely aligned
orifice hole is essential for proper flame characteristics. See
Fig. 29.
Fig. 29 — Orifice Hole
Step 10 — Install External Condensate Trap and
Line
The unit has one
3
/
4
-in. condensate drain connection on the end of
the condensate pan (see Fig. 30). See Fig. 3, 7, and 11 for the loca-
tion of the condensate drain connection.
LEGEND
*
Field supplied.
NOTE:
Follow all local codes.
NFGC –
National Fuel Gas Code
STEEL PIPE
NOMINAL DIAMETER
(in.)
SPACING OF SUPPORTS
X DIMENSION
(ft)
1
/
2
3
/
4
or 1
1
1
/
4
or larger
6
8
10
X
BASE UNIT
BASE RAIL
ROOF
CURB
9” MINIMUM CLEARANCE
FOR PANEL REMOVAL
MANUAL GAS
SHUTOFF VALVE
*
GAS
REGULATOR
*
48” MINIMUM
DRIP LEG
PER NFGC
*
FIELD-
FABRICATED
SUPPORT
*
FROM
GAS
METER
WARNING
Failure to follow this warning could result in personal injury,
death and/or property damage.
• Connect gas pipe to unit using a backup wrench to
avoid damaging gas controls.
• Never purge a gas line into a combustion chamber.
• Never test for gas leaks with an open flame. Use a
commercially available soap solution made specifically
for the detection of leaks to check all connections.
• Use proper length of pipe to avoid stress on gas control
manifold.
BURNER
ORIFICE
Содержание 48TC D/E17 Series
Страница 5: ...5 Fig 2 48TC 17 20 Vertical Airflow...
Страница 6: ...6 Fig 3 48TC 17 20 Back View and Condensate Drain Location...
Страница 7: ...7 Fig 4 48TC 17 20 Corner Weights and Clearances...
Страница 8: ...8 Fig 5 48TC 17 20 Bottom View...
Страница 9: ...9 Fig 6 48TC 24 28 Vertical Airflow...
Страница 10: ...10 Fig 7 48TC 24 28 Back View and Condensate Drain Location...
Страница 11: ...11 Fig 8 48TC 24 28 Corner Weights and Clearances...
Страница 12: ...12 Fig 9 48TC 24 28 Bottom View...
Страница 13: ...13 Fig 10 48TC 30 Vertical Airflow...
Страница 14: ...14 Fig 11 48TC 30 Back View and Condensate Drain Location...
Страница 15: ...15 Fig 12 48TC 30 Corner Weights and Clearances...
Страница 16: ...16 Fig 13 48TC 30 Bottom View...
Страница 19: ...19 Fig 16 Roof Curb Details 17 and 20 Size Units...
Страница 20: ...20 Fig 17 Roof Curb Details 24 and 28 Size Units...
Страница 21: ...21 Fig 18 Roof Curb Details 30 Size Units...
Страница 47: ...47 Fig 52 PremierLink Wiring Diagram...
Страница 48: ...48 Fig 53 PremierLink Wiring Diagram with Humidi MiZer System...
Страница 49: ...49 Fig 54 Typical RTU Open System Control Wiring Diagram...
Страница 50: ...50 Fig 55 Typical RTU Open System Control Wiring Diagram with Humidi MiZer System...
Страница 51: ...51 Fig 56 48TC 17 30 Control Wiring Diagram...
Страница 52: ...52 Fig 57 48TC 17 30 Power Wiring Diagram 208 230 3 60...
Страница 53: ...53 Fig 58 48TC 17 30 Power Wiring Diagram 460 3 60...
Страница 54: ...54 Fig 59 48TC 17 30 Power Wiring Diagram 575 3 60...
Страница 55: ...55 Fig 60 48TC 17 30 Control Wiring Diagram with Humidi MiZer System...
Страница 56: ...56 Fig 61 48TC 17 30 Power Wiring Diagram with Humidi MiZer System 208 230 3 60...
Страница 57: ...57 Fig 62 48TC 17 30 Power Wiring Diagram with Humidi MiZer System 460 3 60...
Страница 58: ...58 Fig 63 48TC 17 30 Power Wiring Diagram with Humidi MiZer System 575 3 60...