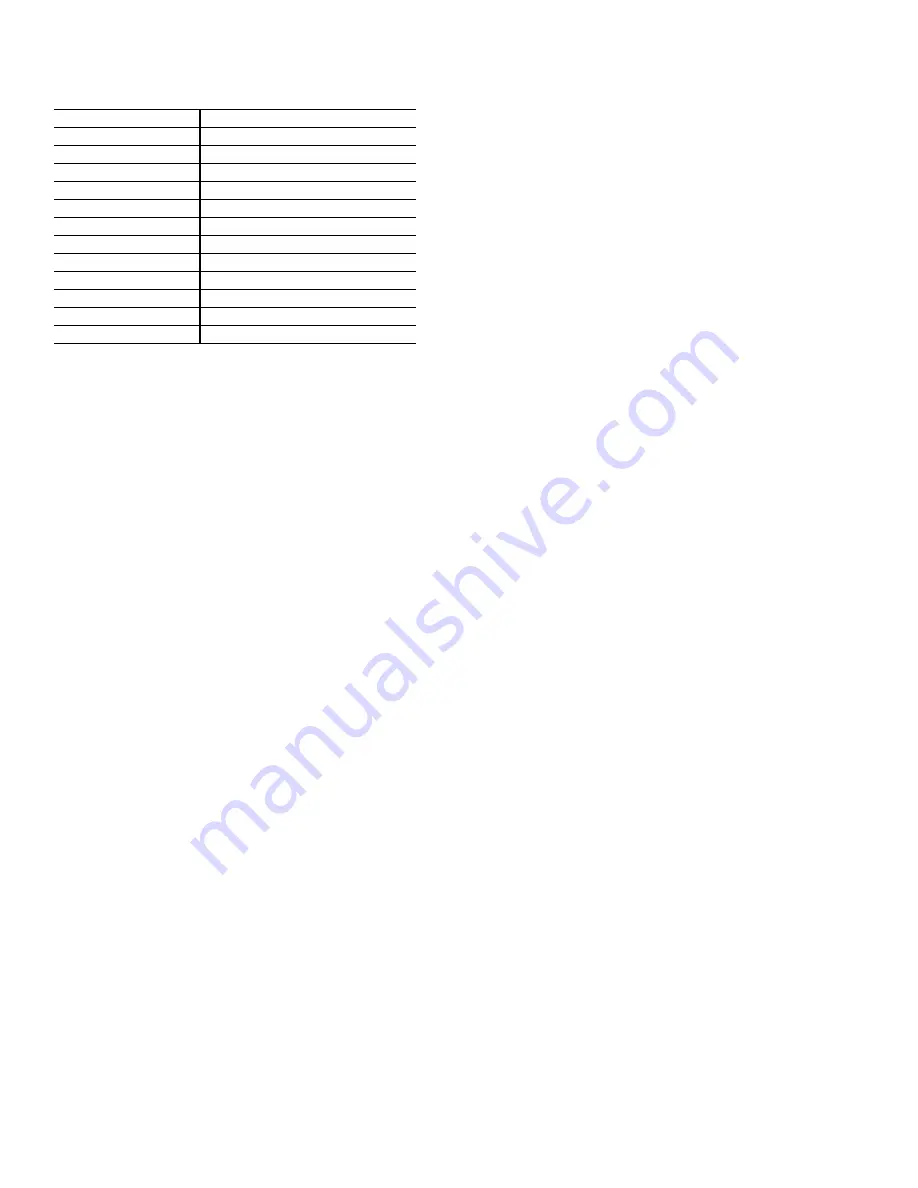
50
Failure to provide proper water quality will void the fan
coils unit's warranty.
Table 6 — Water Quality Concentrations
Controls Operation —
Before proper control operation
can be verified, all other systems must be operating properly.
The correct water and air temperatures must be present for the
control function being tested. Some controls and features are
designed to not operate under certain conditions. For example,
on a two-pipe cooling/heating system with auxiliary electric
heat, the electric heater cannot be energized with hot water in
the system.
A wide range of controls, electrical options and accessories
may be used with the equipment covered in this manual. Con-
sult the approved unit submittals, order acknowledgments, and
other literature for detailed information regarding each individ-
ual unit and its controls. Since controls and features may vary
from one unit to another, care should be taken to identify the
controls used on each unit and their proper control sequence.
Information provided by component manufacturers regarding
installation, operation, and maintenance of their individual con-
trols is available upon request.
When changing from one mode to another (cooling to heat-
ing or heating to cooling), it may take some time to actually no-
tice a change in the leaving air temperature. In addition, some
units may be designed for a very low air temperature rise in
heating. Before declaring a unit inoperative or a component
defective, it may be necessary to verify operation by more than
one method.
SERVICE
Excessive Condensation on Unit —
Running
chilled water through a fan coil unit with the unit fan off can
cause excessive condensation. If fan cycling is used, a water
flow control valve should be installed to shut off the water
when the fan stops.
Other methods of control that avoid condensation problems
are as follows:
1. Continuous fan operation with motorized chilled water
valve controlled by a thermostat.
2. Continuous fan operation with thermostat control to
switch fan from high to low speed (instead of off).
To Clean Coil
1. Be sure electrical service switch is open, locked, and
tagged while working on unit.
2. Remove return-air grille access panel and brush between
coil fins with stiff wire brush. Care should be taken to not
damage coil fins. Follow-up by cleaning with vacuum
cleaner. If coil is cleaned with air hose and nozzle, take
care not to drive dirt and dust into other components.
Blow air through the coil fins from the leaving air face.
This should again be followed by vacuuming. Units
provided with the proper type of air filters, replaced regu-
larly, will require less frequent coil cleaning.
3. Install clean filter. Refer to Clean or Replace Air Filters
section.
Drain —
The drain must be checked before initial start-up
and at the beginning of each cooling season to assure that the
drain trap and line are clear. If it is clogged, take steps to clear
the debris so that condensate will flow easily.
Make periodic checks of the drain during the cooling season
to maintain a free flowing condensate. Units provided with sec-
ondary or tell-tale drain connection will indicate a clogged
main line by flow from the tell-tale connection.
NOTE: Should the growth of algae and/or bacteria be a con-
cern, consult an air conditioning and refrigeration supply orga-
nization familiar with local conditions for chemical or other
solution available to control these growths.
Check Drain —
Lock open and tag unit electrical service
switch.
Check drain pan, drain line and trap before initial start-up
and at start of each cooling season. A standard type pipe clean-
er for
3
/
4
-in. ID pipe can be used to ensure that pipe is clear of
obstruction so that condensate is carried away. Check the drain
line at filter cleaning time during the cooling season. Be sure
that debris has not fallen into unit through supply-air grille.
Should the growth of algae and/or bacteria be a concern, con-
sult an air conditioning and refrigeration supply organization
familiar with local conditions for chemicals or other solutions
available to control these agents.
Fan Motor Bearings —
Lock open and tag unit electri-
cal service switch.
Standard motors are permanently sealed and lubricated. No
lubrication is required unless special motors have been
supplied or unusual operating conditions exist.
Clean Fan Wheel —
Lock open and tag unit electrical
service switch.
For access to fan assembly, remove front or bottom panel.
Fan assembly may be removed from its tracks if unit has a long
conduit lead. Dirt and debris should not be allowed to accumu-
late on the blower wheel or housing. This can result in an un-
balanced blower wheel condition which can damage a blower
wheel or motor. The wheel and housing may be cleaned peri-
odically using a vacuum cleaner and a brush, taking care not to
dislodge the factory balancing weights on the blower wheel
blades.
Clean Electric Heater —
Lock open and tag unit elec-
trical service switch.
1. Remove dust, dirt, or foreign material before start-up. Do
not block normal airflow to and from units; blockage may
damage electric heaters.
2. Clean heater elements with soft brush or vacuum cleaner
as necessary.
3. To replace blown fusible links (nichrome heaters only):
a. Remove fan deck (horizontal units only) for
access to heater.
b. Remove nut securing link at each end; install new
link; reinstall nuts.
c. Reinstall fan deck (if removed).
Electric resistance heaters typically require no normal
periodic maintenance when unit air filters are changed
properly. The operation and service life may be affected by
other conditions and equipment in the system. The two most
important operating conditions for an electric heater are proper
airflow and proper supply voltage. High supply voltage and/or
poorly distributed or insufficient airflow over the element will
WATER CONTAINING
REQUIRED CONCENTRATION
Sulphate
Less than 200 ppm
pH
7.0 to 8.5
Chlorides
Less than 200 ppm
Nitrate
Less than 100 ppm
Iron
Less than 4.5 mg/l
Ammonia
Less than 2.0 mg/l
Manganese
Less than 0.1 mg/l
Dissolved Solids
Less than 1000 mg/l
CaCO3 Hardness
300 to 500 ppm
CaCO3 Alkalinity
300 to 500 ppm
Particulate Quantity
Less than 10 ppm
Particulate Size
800 micron max