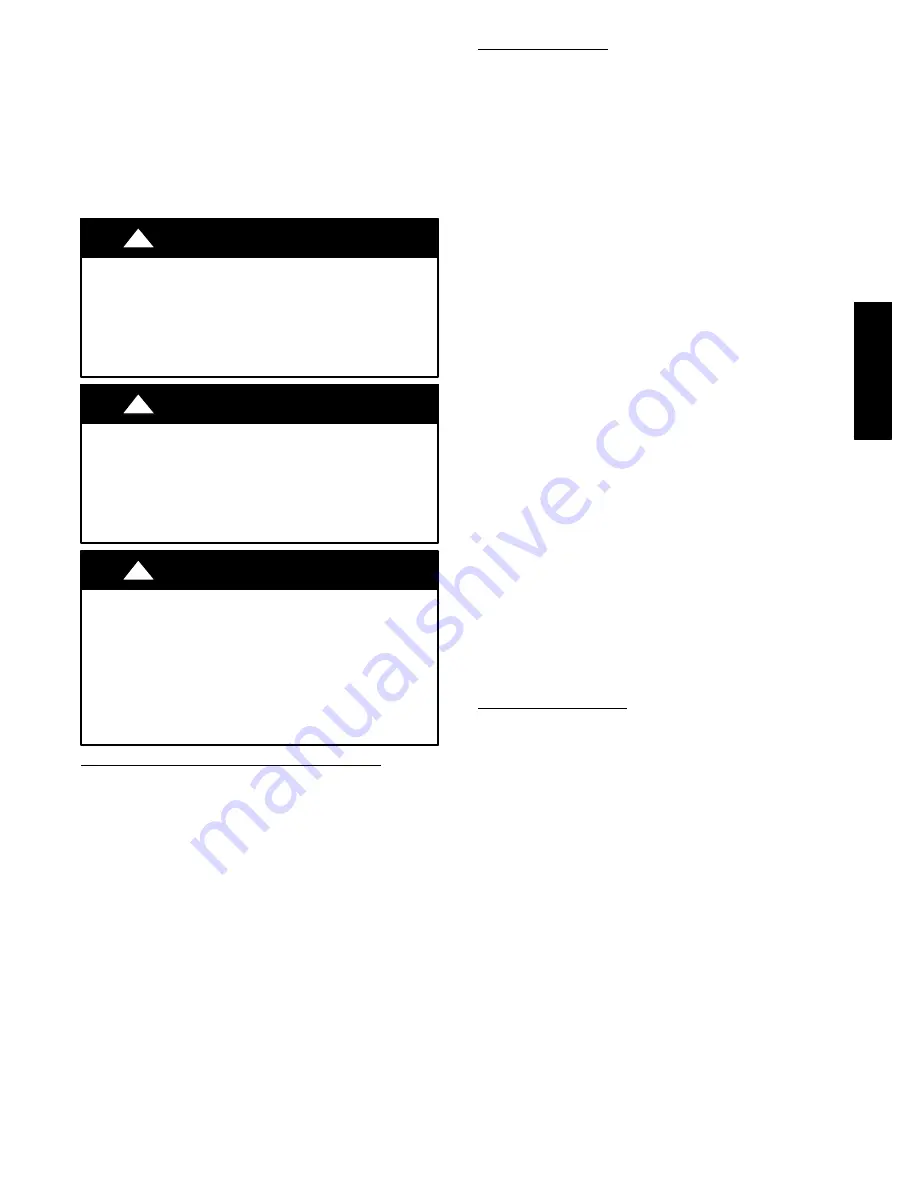
7
Airflow Selection for FV4C Fan Coils
(non
−
communicating)
The FV4 provides high
−
and low
−
stage blower operation to match
the capacities of the compressor at high
−
and low
−
stage.
To select recommended airflow, refer to the FV4C Installation
Instructions. The FV4C utilizes an Easy Select control board that
allows the installing technician to select proper airflows. This fan
coil has an adjustable blower
−
off delay factory set at 90 sec. for
high
−
and low
−
stage blower operation.
Start
−
Up
CAUTION
!
PERSONAL INJURY HAZARD
Failure to follow this caution may result in personal
injury.
Wear safety glasses, protective clothing, and gloves when
handling refrigerant and observe the following:
S
Front seating service valves are equipped with Schrader valves.
CAUTION
!
ENVIRONMENTAL HAZARD
Failure to follow this caution may result in environmental
damage.
Federal regulations require that you do not vent refrigerant to
the atmosphere. Recover during system repair or final unit
disposal.
CAUTION
!
UNIT OPERATION AND SAFETY HAZARD
Failure to follow this caution may result in personal injury,
equipment damage or improper operation.
S
Do not overcharge system with refrigerant.
S
Do not operate unit in a vacuum or at negative pressure.
S
Do not disable low pressure switch in scroll compressor
applications.
S
Compressor dome temperatures may be hot.
Follow these steps to properly start up system:
1. After system is evacuated, fully open liquid and vapor ser-
vice valves.
2. Unit is shipped with valve stem(s) front seated (closed) and
caps installed. Replace stem caps after system is opened to
refrigerant flow (back seated). Replace caps finger
−
tight and
tighten with wrench an additional 1/12 turn.
3. Close electrical disconnects to energize system.
4. Set room thermostat at desired temperature. Be sure set
point is below indoor ambient temperature.
5. Set room thermostat to HEAT or COOL and fan control to
ON or AUTO mode, as desired. Operate unit for 15
minutes. Check system refrigerant charge.
Sequence of Operation
NOTE
: Defrost control board is equipped with 5 minute lockout
timer that is initiated upon any interruption of power.
Turn on power to indoor and outdoor units. Transformer is
energized.
These models utilize a 2
−
stage indoor thermostat. With a call for
first (low) stage cooling or heating, the outdoor fan and low
−
stage
compressor are energized. If low
−
stage cannot satisfy cooling or
heating demand, high
−
stage is energized by the second (high) stage
of the indoor thermostat. After the second stage is satisfied, the
unit returns to low
−
stage operation until second stage is required
again. When both, first and second stage cooling or heating are
satisfied, the compressor will shut off.
Cooling
With first stage cooling, Y and O are powered on; and with second
stage cooling, Y2, Y and O are powered on. The O energizes the
reversing valve, switching it to cooling position. The Y signal
sends low voltage through the safeties and energizes the T1
terminal on the circuit board. If the compressor has been off for 5
minutes, or power has not been cycled for 5 minutes, the OF2 relay
and T2 terminal will energize. This will close the contactor and
start the outdoor fan motor and compressor. When the cycle is
complete, Y is turned off, stopping the compressor and outdoor
fan. The 5 minute time guard begins counting. Compressor will
not come on until this delay expires. In the event of a power
interruption, the time guard will not allow another cycle for 5
minutes.
Heating
With first stage heating, Y is powered on; with second stage
heating, Y2 and Y are powered on. The Y signal sends low
voltage through the safeties and energizes the T1 terminal on the
circuit board. If the compressor has been off for 5 minutes or
power has not been cycled for 5 minutes, the OF2 relay and T2
terminal will energize. This will close the contactor and start the
outdoor fan motor and compressor.
When the cycle is complete, Y is turned off, stopping the
compressor nd outdoor fan. The 5 minute time guard begins
counting. Compressor will not come on until this delay expires. In
the event of a power interruption, the time guard will not allow
another cycle for 5 minutes.
Compressor Operation
The basic scroll design has been modified with the addition of an
internal unloading mechanism that opens a by
−
pass port in the first
compression pocket, effectively reducing the displacement of the
scroll. The opening and closing of the by
−
pass port is controlled
by an internal electrically operated solenoid. The modulated scroll
uses a single step of unloading to go from full capacity to
approximately 67% capacity.
A single speed, high efficiency motor continues to run while the
scroll modulates between the two capacity steps. Modulation is
achieved by venting a portion of the gas in the first suction pocket
back to the low side of the compressor, thereby reducing the
effective displacement of the compressor.
Full capacity is achieved by blocking these vents, thus increasing
the displacement to 100%. A DC solenoid in the compressor
controlled by a rectified 24 volt AC signal in the external solenoid
plug moves the slider ring that covers and uncovers these vents.
The vent covers are arranged in such a manner that the compressor
operates at approximately 67% capacity when the solenoid is not
energized and 100% capacity when the solenoid is energized. The
loading and unloading of the two step scroll is done ”on the fly”
without shutting off the motor between steps.
NOTE
: 67% compressor capacity translates to approximately
75% cooling or heating capacity at the indoor coil.
25HCB6