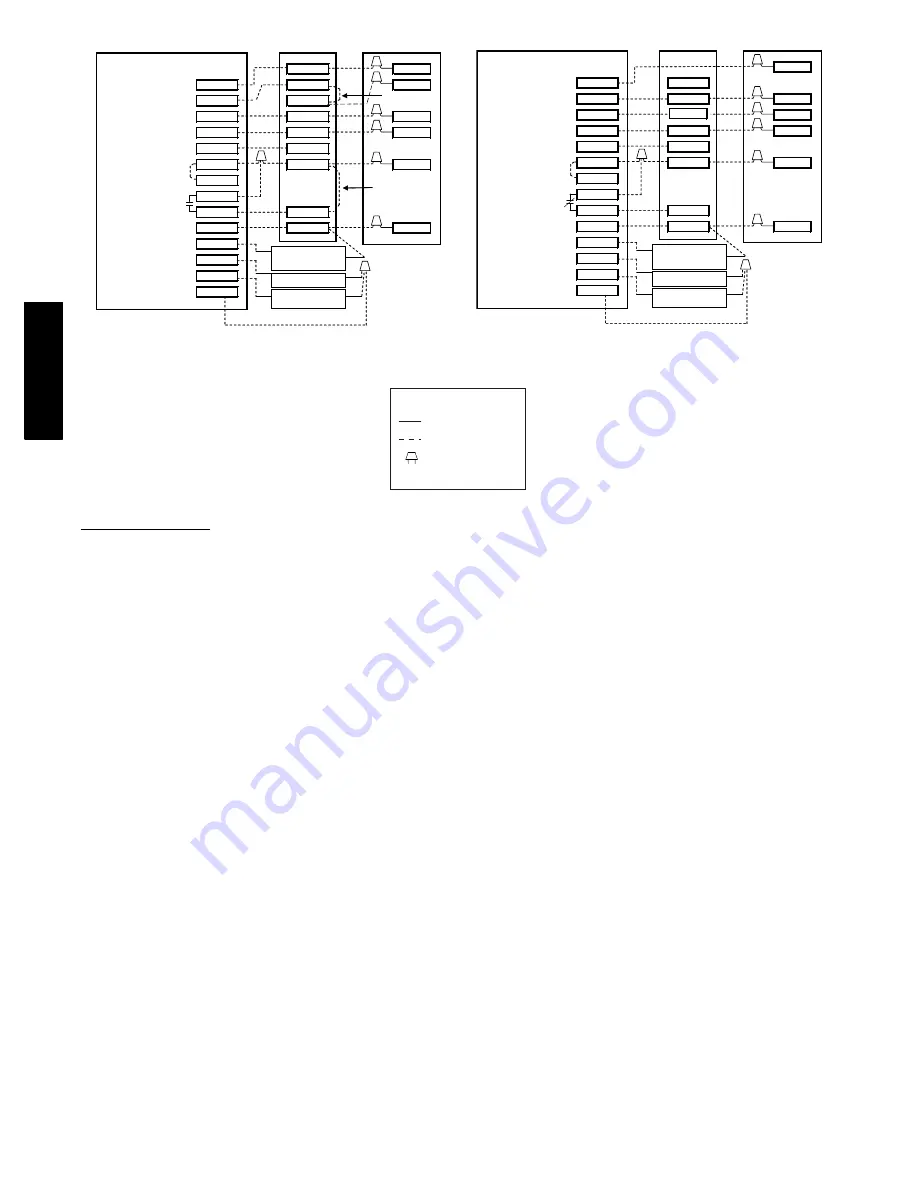
6
LEGEND
24v Factory Wiring
24v Field Wiring
Field Splice Connection
A09306
Fig. 9
−
Thermidistat Model TP
−
PRH
−
01 or TP
−
NRH
−
01
Wiring with Fan Coil and 25HCB6 2
−
Stage Heat Pump
(non
−
communicating)
Fig. 10
−
Thermidistat Model TP
−
PRH
−
01 or TP
−
NRH
−
01
with Variable Speed Furnace and 25HCB6 2
−
Stage Heat Pump
(non
−
communicating)
O
O
RVS Cooling
O/B W2
W1
W2
Heat Stage 3
W/W1
W2
Heat/Cool Stage 1
Y1 / W2
Y1
Y
Heat/Cool Stage 2
Y/Y2
Y/Y2
Y2
Fan
G
G
24VAC Hot Heating
Rh
R
R
24VAC Hot Cooling
Rc
J2 Jumper
on Control Board
Dry Contact 1
D1
Dry Contact 2
D2
DH
24VAC Common
C
C
C
Humidify
HUM
Outdoor Air Temp
OAT
Remote Room Sensor
RRS
OAT/RRS Com
SRTN
Thermidistat
Fan Coil
Heat Pump
Outdoor Sensor
Humidifier Solenoid
Valve
Remote Room
Sensor
Remove J1 Jumper
for Dehumidify modes
Thermidistat
Furnace
Heat Pump
O
RVS Cooling
O/B W2
W2
Heat Stage 3
(furnace)
W/W1
W/W1
W2
Heat/Cool Stage 1
Y1 / W2
Y
Heat/Cool Stage 2
Y/Y2
Y/Y2
Y2
Fan
G
G
24VAC Hot Heating
Rh
R
R
24VAC Hot Cooling
Rc
Dry Contact 1
D1
Dry Contact 2
D2
DHUM
24VAC Common
C
COM
C
Humidify
HUM
Outdoor Air Temp
OAT
Remote Room Sensor
RRS
OAT/RRS Com
SRTN
Outdoor Sensor
Humidifier Solenoid
Valve
Remote Room
Sensor
Y1
A12258
A12259
Final Wiring Check
IMPORTANT
: Check factory wiring and field wire connections
to ensure terminations are secured properly. Check wire routing to
ensure wires are not in contact with tubing, sheet metal, etc.
Compressor Crankcase Heater
All sizes are equipped with a crankcase heater. Furnish power to
heater a minimum of 24 hours before starting unit. To furnish
power to heater only, set thermostat to OFF and close electrical
disconnect to outdoor unit.
A crankcase heater is required if refrigerant tubing is longer than
80 ft. (24.4 m), or when outdoor unit is 20 ft. (6.1 m) below the
indoor unit. Refer to the
Residential Piping and Long Line
Guideline
.
Install Electrical Accessories
Refer to the individual instructions packaged with kits or
accessories when installing.
Airflow Selections (ECM Furnaces)
The ECM Furnaces provide blower operation to match the
capacities of the compressor during high and low stage cooling
operation. Tap selections on the furnace control board enable the
installing technician to select the proper airflows for each stage of
cooling. Below is a brief summary of the furnace airflow
configurations
1. The Y2 call for high stage cooling energizes the “Cool” tap
on the control board. The grey wire from cool tap is connec-
ted to tap 5 on the motor. Refer to the furnace Product Data
to find the corresponding airflow. If the airflow setting for
high cooling needs to be switched from tap 5 to a different
tap, jumper a connection from the cool tap to the desired tap
so that the Y2 signal is communicated via the cool tap to the
desired speed tap.
2. The Y1 call for low stage cooling energizes the “Fan” tap
on the control board. The red wire from the fan tap is con-
nected to tap 1 on the motor. Refer to the furnace Product
Data to find the corresponding airflow. If the airflow setting
for low cooling needs to be switched from tap 1 to a differ-
ent tap, jumper a connection from the Fan tap to the desired
tap so that the Y1 signal is communicated via the Fan tap to
the desired speed tap. The Y1 setting will also govern the
continuous fan airflow for the furnace.
Refer to the literature for the furnace for further details.
Airflow Selection for Variable Speed Furnaces
(non
−
communicating)
The variable speed furnaces provide blower operation to match the
capacities of the compressor during high and low stage cooling
operation. The furnace control board allows the installing
technician to select the proper airflows for each stage of cooling.
Below is a summary of required adjustments. See furnace
installation instructions for more details:
1. Turn SW1
−
5 ON for 400 CFM/ton airflow or OFF for 350
CFM/ton airflow. Factory default is OFF.
2. The A/C DIP switch setting determines airflow during high
stage cooling operation. Select the A/C DIP switch setting
corresponding to the available airflow shown in the furnace
Installation Instructions that most closely matches the re-
quired airflow shown in the air conditioning Product Data
for HIGH speed.
3. The CF DIP switch setting determines airflow during low
stage cooling operation. Select the CF DIP switch setting
corresponding to the available airflow shown in the furnace
installation instructions that most closely matches the re-
quired airflow shown in the air conditioning Product Data
for LOW speed. If a higher or lower continuous fan speed is
desired, the continuous fan speed can be changed using the
fan switch on the thermostat. Refer to the furnace Installa-
tion Instructions for details of how to use this feature.
25HCB6