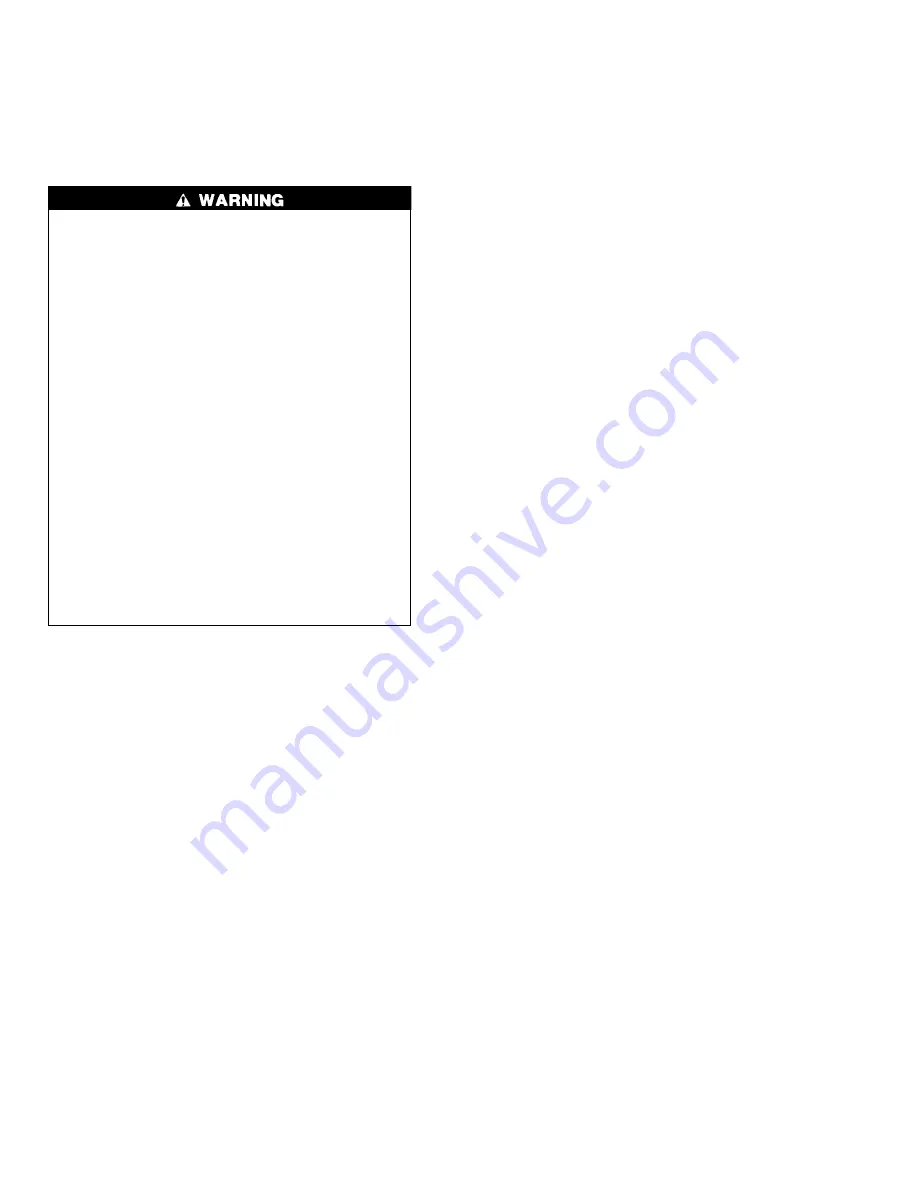
INTRODUCTION
Prior to initial start-up of the 19EF unit, those involved in
the start-up, operation, and maintenance should be thor-
oughly familiar with these instructions and other necessary
job data. This book is outlined so that you may become fa-
miliar with the control system before performing start-up pro-
cedures. Procedures in this manual are arranged in
the sequence required for proper machine start-up and
operation.
This unit uses a microprocessor control system. Do not
short or jumper between terminations on circuit boards
or modules; control or board failure may result.
Be aware of electrostatic discharge (static electricity)
when handling or making contact with circuit boards or
module connections. Always touch a chassis (grounded)
part to dissipate body electrostatic charge before work-
ing inside control center.
Use extreme care when handling tools near boards
and when connecting or disconnecting terminal plugs.
Circuit boards can easily be damaged. Always hold boards
by the edges and avoid touching components and
connections.
This equipment uses, and can radiate, radio fre-
quency energy. If not installed and used in accordance
with the instruction manual, it may cause interference
to radio communications. It has been tested and found
to comply with the limits for a Class A computing de-
vice pursuant to Subpart J of Part 15 of FCC Rules, which
are designed to provide reasonable protection against such
interference when operated in a commercial environ-
ment. Operation of this equipment in a residential area
is likely to cause interference, in which case the user, at
his own expense, will be required to take whatever mea-
sures may be required to correct the interference.
Always store and transport replacement or defective
boards in anti-static shipping bag.
ABBREVIATIONS
Frequently used abbreviations in this manual include:
CCN
— Carrier Comfort Network
CCW
— Counterclockwise
CW
— Clockwise
ECW
— Entering Chilled Water
ECDW — Entering Condenser Water
EMS
— Energy Management System
HGBP — Hot Gas Bypass
I/O
— Input/Output
LCD
— Liquid Crystal Display
LCDW — Leaving Condenser Water
LCW
— Leaving Chilled Water
LED
— Light-Emitting Diode
LID
— Local Interface Device
OLTA
— Overload Trip Amps
PIC
— Product Integrated Control
PSIO
— Processor Sensor Input/Output Module
RLA
— Rated Load Amps
SCR
— Silicon Control Rectifier
SMM
— Starter Management Module
MACHINE FAMILIARIZATION
(Fig. 1 and 2)
Machine Information Plate —
The information plate
is located on the left side of the machine control center panel.
System Components —
The components include the
cooler and condenser heat exchangers in separate vessels,
motor-compressor, lubrication package, control center, econo-
mizer, and motor starter. All connections from pressure ves-
sels have external threads to enable each component to be
pressure tested with a threaded pipe cap during factory
assembly.
Cooler —
This vessel (also known as the evaporator) is
located underneath the compressor. The cooler is main-
tained at lower temperature/pressure so that evaporating re-
frigerant can remove heat from water flowing through its in-
ternal tubes.
Condenser —
The condenser operates at a higher
temperature/pressure than the cooler, and has water flowing
through its internal tubes in order to remove heat from the
refrigerant.
Economizer —
During normal operation, this vessel func-
tions as an economizer, returning flash gas to the second stage
of the compressor and increasing the efficiency of the re-
frigerant cycle.
Motor-Compressor —
This component maintains sys-
tem temperature/pressure differences and moves the heat car-
rying refrigerant from the cooler to the condenser.
Control Center —
The control center is the user inter-
face for controlling the machine. It regulates the machine’s
capacity as required to maintain proper leaving chilled water
temperature. The control center:
• registers cooler, condenser, and lubricating system
pressures
• shows machine operating conditions and alarm shutdown
conditions
• records the total machine operating hours and how many
hours the machine has been running
• sequences machine start, stop, and recycle under micro-
processor control
• provides access to other CCN (Carrier Comfort Network)
devices
Motor Starter —
The starter allows for the proper start-
ing and disconnecting of the electrical energy for the
compressor-motor, oil pump, oil heater, and control center.
This component is freestanding.
REFRIGERATION CYCLE (Fig. 3)
The machine compressor continuously draws large quan-
tities of refrigerant vapor from the cooler at a rate set by the
amount of guide vane opening. This compressor suction re-
duces the pressure within the cooler and causes the remain-
ing refrigerant to boil vigorously at low temperature (typi-
cally 38 to 42 F [3 to 6 C]).
The energy required for boiling is obtained as heat from
the water (or brine) flowing through the cooler tubes. With
heat removed, the chilled water (brine) can then be used for
air conditioning or for process liquid cooling.
4
Содержание 19EF Series
Страница 10: ...Fig 5 19EF Controls and Sensor Locations cont 10...
Страница 13: ...Fig 12 19EF Menu Structure 13...
Страница 14: ...Fig 13 19EF Service Menu Structure 14...
Страница 38: ...Fig 24 19EF Leak Test Procedures 38...
Страница 69: ...Fig 36 Electronic PIC Controls Wiring Schematic 69...
Страница 70: ...Fig 36 Electronic PIC Controls Wiring Schematic cont 70...
Страница 71: ...Fig 37 Machine Power Panel Starter Assembly and Motor Wiring Schematic 71...