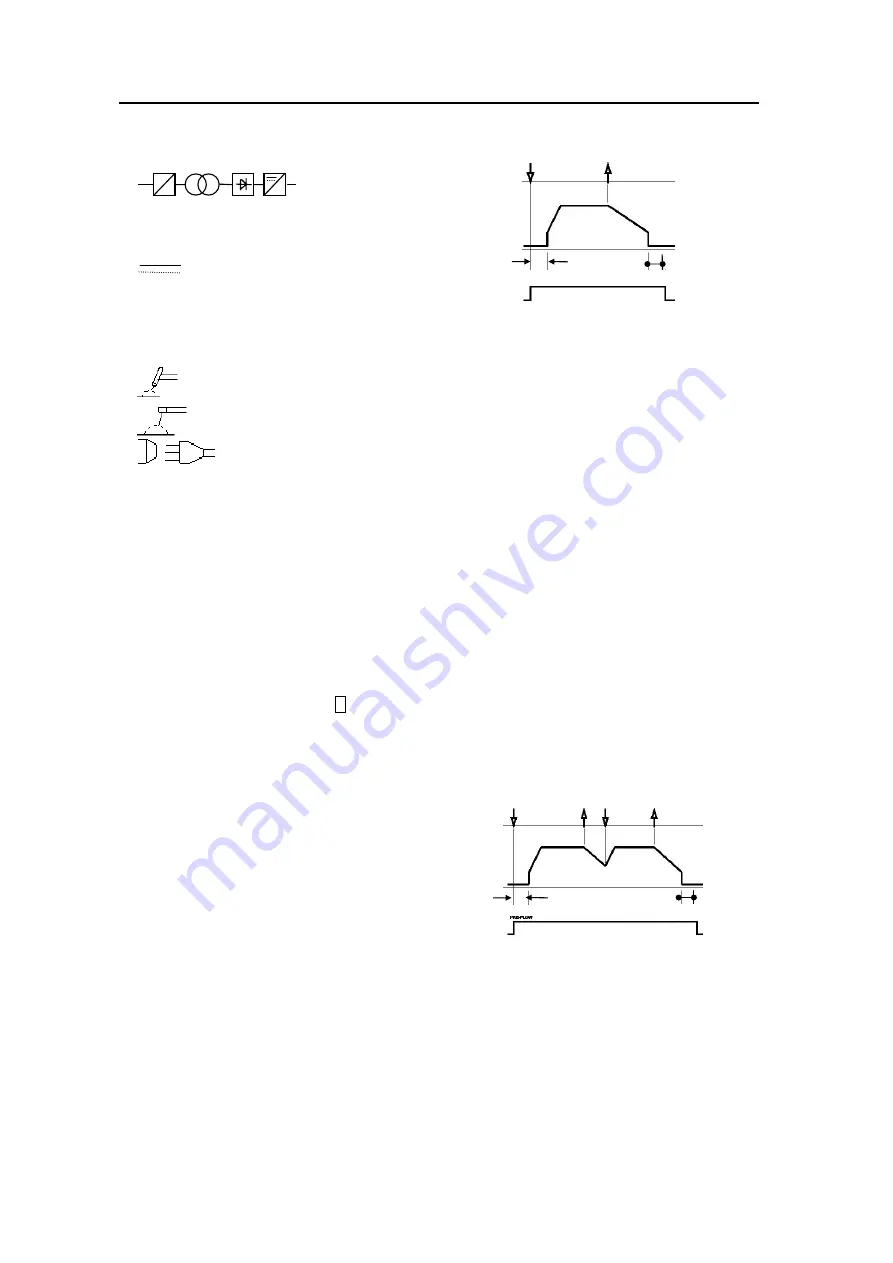
B-5 OPERATION B-5
* (a) Manufacturer's name and address
* (b) Trademark
* (c) Model
* (No) Serial number
* ( ) The welding power
source comprises a frequency converter followed by
an transformer and rectifier that transforms input
voltage into direct current.
* (EN 60974-1/EN 50199) Standards applied.
* ( ) Direct current.
* (x) Utilisation factor expressed as a percentage of
useful work over a cycle of 10 minutes at an
ambient temperature of 40
o
C.
* (I
2
) Rated weld current.
* (U
2
) Conventional load voltage.
* (Uo) Rated no-load voltage.
* ( ) TIG welding.
* ( ) MMA welding.
* ( )) 1input phases.
* (IP21S) Casing protection degree in compliance
with the EN 60529 Standard:
IP2XX Casing protected against access to
dangerous components with fingers and against the
introduction of foreign matters with diameter 12.5
mm.
IPX3X Casing protected against rain failing at
60~on the vertical line.
IPXXC Casing protected against contact of a test
gauge
φ
2.5 mm length 100 mm with live
dangerous parts,
* (U
1
) Rated power supply voltage.
* (50/60 Hz) Power supply rated frequency.
* (l
lmax
) Maximum supply current.
(I
1 eff
) Effective supply current.* ( S ) Generator
suitable for installation in places where major risks
of electric shocks are preset
* (CE) In compliance with the European regulations
in force.
24.fan
when power switch on, the cooling fan runs
25.safety earthing column
The earthing must be made according to the
national regulations. Make sure that the supply
mains and the earthing are sufficient and adequate
26. 2 steps/ 4 steps switch
Tig Trigger Sequences -
For the TIG machine AC/DC, TIG welding can be
done in either the 2-step or 4-step mode which is
selected with the Trigger Mode Push Button.
2-Step Sequence
With the Trigger Mode switch in the 2-step position,
the following welding sequence will occur. This
sequence is shown in (2-step diagram 1)
2 STEP DIAGRAM 1
1. Press and hold the Arc Start Switch to start the
sequence.
The machine will open the gas valve to start the
flow of the shielding gas. After a 0.5 second preflow
time, to purge air from the torch hose, the output of
the machine is turned ON. At this time the arc is
started.
After the arc is started the output current will be
increased from the start current to the welding
current. Both the start current and increase, or
upslope time are presettable. The default start
current is 15 amps and the default upslope time is
0.2 seconds.
2. Release the Arc Start Switch to stop welding.
The machine will now decrease the output current
at a controlled rate, or down slope time, until the
Finish current, (also commonly referred to as Crater
Current) is reached and the output of the machine is
turned OFF. Both the Down slope Time and the
Finish Current are can be preset.
After the arc is turned OFF, the gas valve will
remain open to continue the flow of the shielding
gas to the hot electrode and work piece. The
duration of this postflow shielding gas is adjusted by
the Postflow Parameter.
Possible variations of this standard sequence is
shown in (2 step diagram 2). It is possible to press
and hold the TIG torch trigger a second time during
downslope to restart. After the trigger is pressed the
output current will increase to the welding current.
This operation is shown in (2 step diagram 2).
2 STEP DIAGRAM 2
~
1~
f1
f2
~
TORCH
BUTTON
OUTPUT
CURRENT
GAS
PRE-FLOW
GAS ON
POST-FLOW
TORCH
BUTTON
OUTPUT
CURRENT
GAS
PRE-FLOW
GAS ON
POST-FLOW
Содержание PowerMaster205
Страница 27: ...B 13 OPERATION B 13...
Страница 28: ...B 14 OPERATION B 14...
Страница 29: ...B 15 OPERATION B 15...
Страница 33: ...B 19 OPERATION B 19...
Страница 34: ...B 20 OPERATION B 20...
Страница 35: ...B 21 OPERATION B 21...
Страница 36: ...B 22 OPERATION B 22...