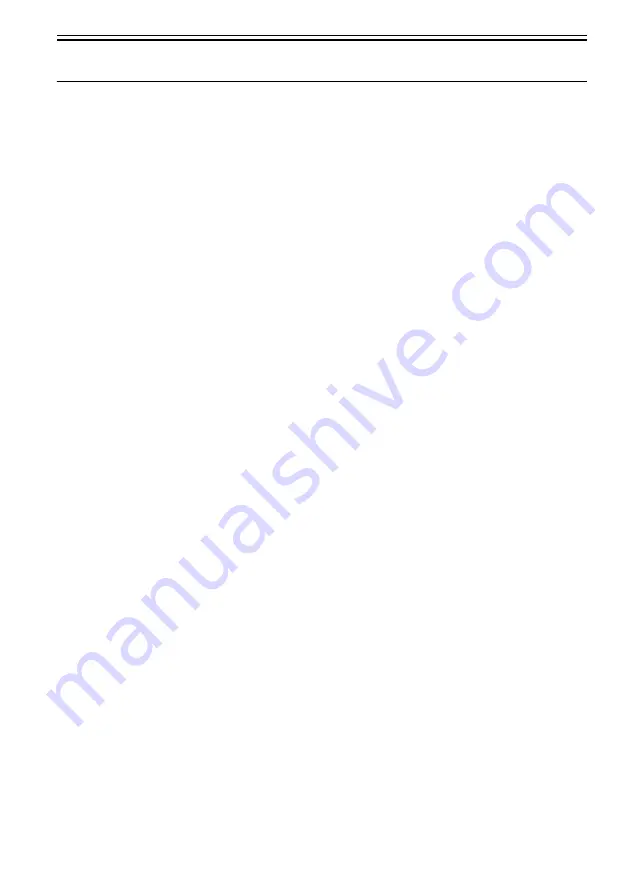
Chapter 6
6-1
6.1 Troubleshooting
6.1.1 Outline
6.1.1.1 Outline of Troubleshooting
0013-1941
1. Overview
Targets of troubleshooting are classified into the troubles displayed on the LCD (i.e., warnings, errors, and
service calls) and the troubles not displayed on the LCD.
Warnings and errors are displayed on the printer's LCD along with a code comprising alphanumeric characters.
2. Precautions for Troubleshooting
1) Check the environmental conditions and the media used.
2) Before starting troubleshooting, check that the connectors and cables are connected properly.
3) If you repair the printer with its external panel detached without disconnecting the AC cord from the outlet,
take great care to prevent electric shock and short-circuiting of PC boards.
4) Countermeasures to take after completion of troubleshooting are described starting with the most probable
component that can cause the trouble determined by troubleshooting. If there are two or more equally
probable components, countermeasures are described starting with the component that requires the easiest
repair. After performing each countermeasure step, carry out test printing to check whether the problem has
been solved. If not solved, try the next countermeasure step.
5) After completion of troubleshooting, check that all the necessary connectors and screws have been
installed securely.
6) After completion of replacement or repair of a component, be sure to carry out test printing to make sure
that the trouble has been solved.
Содержание iPF710 - imagePROGRAF Color Inkjet Printer
Страница 10: ...Chapter 1 PRODUCT DESCRIPTION...
Страница 61: ...Chapter 2 TECHNICAL REFERENCE...
Страница 113: ...Chapter 3 INSTALLATION...
Страница 119: ...Chapter 4 DISASSEMBLY REASSEMBLY...
Страница 155: ...Chapter 5 MAINTENANCE...
Страница 162: ...Chapter 6 TROUBLESHOOTING...
Страница 190: ...Chapter 7 SERVICE MODE...
Страница 225: ...Chapter 8 ERROR CODE...
Страница 233: ...APPENDIX...
Страница 238: ......