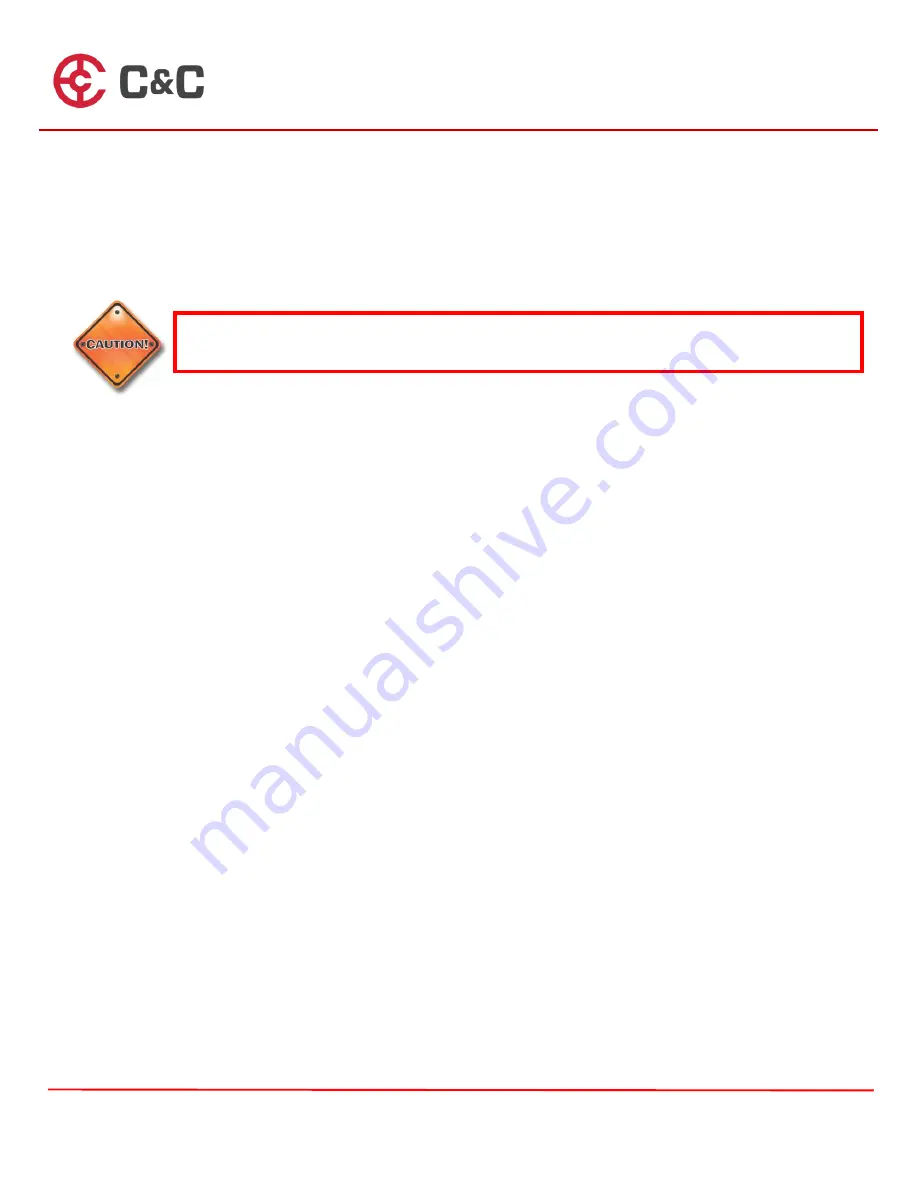
API 6D Two - Piece
Cast Trunnion
Mounted Ball Valve
Atlas Series
Document Number:
Revision:
Release Date:
EDC 506
0
01/03/2018
IOM: Installation, Operation and Maintenance Manual
14/17
For either gear operated valves or actuated valves, make sure that both the travel ends act when
the valve is fully open and closed.
7 PROPER VALVE TESTING
Always perform an API 6D pressure test before re-installing the valve into the line to verify that the
maintenance operation have been satisfactorily performed and to re-certify pressure containment capability
of the valve.
7.1 SHELL TEST
There shall not be any leakage under the pressure when ball is partially open and both ends are blanked.
Testing pressure is 1.5 times the maximum operating pressure. Test duration are 2min for 4” and under
valves, 5mi
n for 6” to 10” valves, 15min for 12” to 18” and 30min for 20” and larger.
(a) Fit the vent valve and set it in open position.
(b) Operate the valve to the half-open position.
(c) Fill in the valve with the fluid (Venting the air through the vent valve)
(d) Close the vent valve and apply pressure in accordance with maximum operating pressure of the
pipeline.
(e) Visually check the outside of the ball valve for leakage.
(f) Depressurize the valve.
7.2 HYDROSTATIC SEAT TEST
Valves are to be subjected to a hydrostatic seat test. There is to be no leakage under test pressure. Test
pressure is to be applied to the appropriate end of the valve. Testing pressures 1.1 times maximum
operating pressure. Test durations are 2
min for 4” and under valves, 5min for 6” to 18” and 10mim for 20”
and larger valves.
(a) Operate the valve to the fully close position and open the vent valve.
(b) Pressurize one side in accordance with max operating pressure of the pipeline.
(c) From the body vent or bleed fitting, check for possible seat leakage.
(d) Repeat same operations as per points (b) & (c) on opposite side of the valve.
(e) Depressurize the valve.
7.3 DOUBLE BLOCK AND BLEED (DBB) TEST
If the valve seats have DBB function, then the seat test shall be performed as follows:
(a) With the valve unseated and partially open, the valve cavity shall be completely filled with test fluid.
(b) The valve shall then be closed and the vent valve opened to allow excess test fluid to overflow form
the valve
– cavity test connection.
(c) The test pressure shall be applied simultaneously from both ends.
(d) Seat tightness shall be monitored from the cavity connection.
(e) Depressurize the valve.
Installing the valve in the line without pressure testing could cause leakage
of production fluid and, potentially hazardous situation.