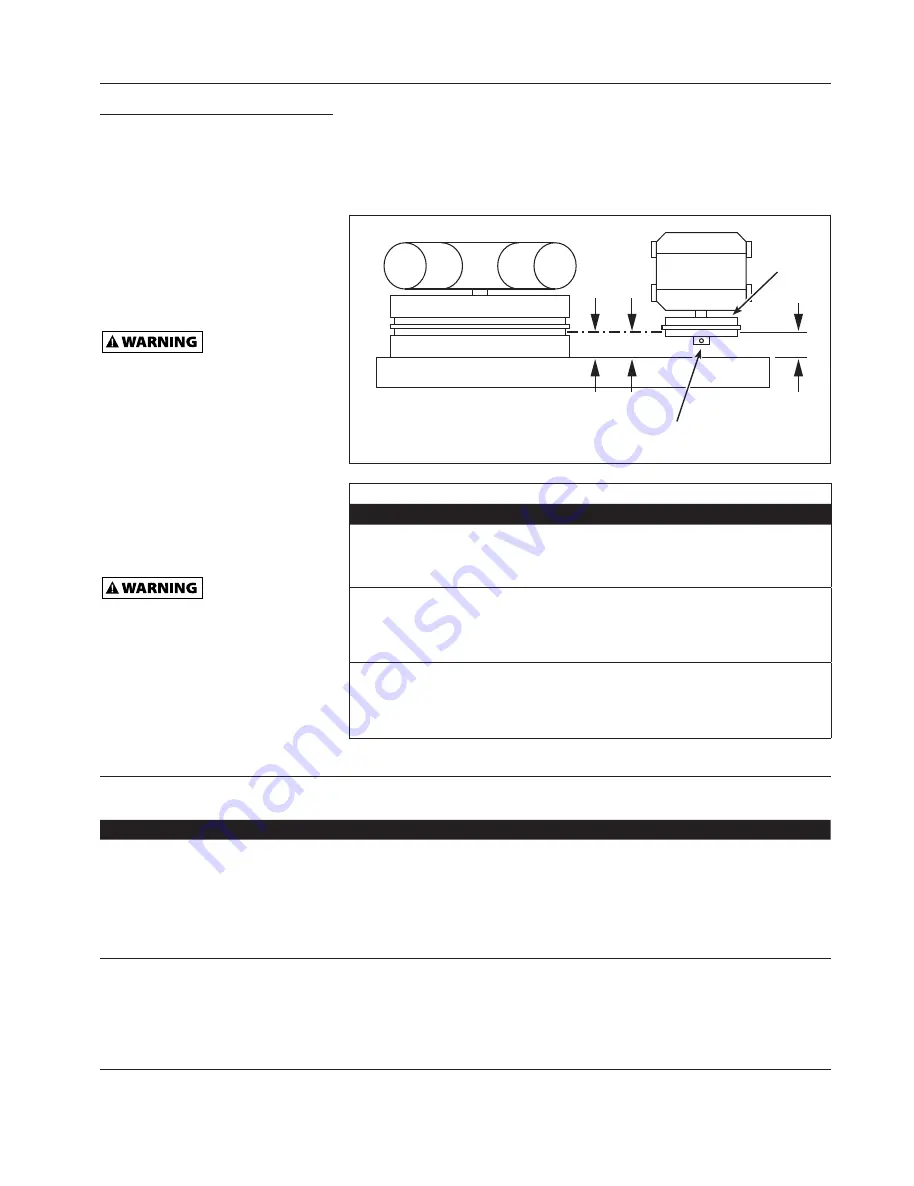
TF2101, TF2111, TQ3010, TQ3011, TX2101, TX2118
7
Maintenance
(Continued)
AIR FILTER
Never run the compressor pump
without an intake air filter nor
with a clogged intake air filter. Use
compressed air to blow the filter clean.
Do not wash or oil the element. If it
cannot be blown clean, the filter must
be replaced. Operating compressor
with a dirty filter can cause high
oil consumption and increase oil
contamination in the discharge air.
INTERCOOLER (TWO-STAGE
COMPRESSORS ONLY)
Intercooler fins
are sharp, always
wear gloves and use care when you
clean or work near the intercooler.
Weekly, check the intercooler to be sure
all fittings are secure and tight. Blow all
dirt, dust and other accumulations from
the intercooler fins.
COMPONENTS
Turn off all power and use light air
pressure to blow dust and foreign
material from cylinder head, motor, fan
blades, air lines, intercooler and tank
on a monthly basis.
BELTS
Lock out and tag
the power then
release all pressure from the tank to
prevent unexpected movement of the
unit.
Check belt tension every 3 months.
Adjust belt tension to allow 3/8 to 1/2
inch deflection with normal thumb
pressure. Also, align belts using a
straight edge against the face of the
flywheel and touching the rim on both
sides of the face. The belts should be
parallel to this straight edge (see
Figure 9). Dimension A should be the
same as B and C to ensure proper
alignment of the belts.
Slots in the bed-plate allow for sliding
the motor back and forth to adjust belt
tension.
STORAGE
If compressor is to be stored for a short
period of time, make sure that it is
stored in a normal position and in a
cool protected area.
�
B
C
Air Compressor
Motor
Flywheel
Straight Edge
Setscrew
Motor
Drive
Pulley
Figure 9 - Top View
Troubleshooting Chart
Symptom
Possible Cause(s)
Corrective Action
Motor hums and
runs slowly or not
at all
1. Low voltage or no voltage
1. Check with voltmeter, check overload relay in magnetic starter or reset
switch on motor. If overload or reset switch trips repeatedly, find and
correct the cause. See next item
2. Shorted or open motor winding
2. Replace motor
3. Malfunctioning check valve or
unloader valve
3. Replace check valve or unloader valve
4. Malfunctioning pressure switch -
contacts will not close
4. Repair or replace pressure switch
Reset mechanism
cuts out repeatedly
or fuses blow
repeatedly
1. Pressure switch set too high
1. Adjust or replace
2. Malfunctioning check valve
2. Clean or replace faulty valve
3. Incorrect fuse size or magnetic
starter heaters
3. Be sure that fuses and heaters are rated properly
4. Malfunctioning motor
4. Replace motor
5. Loose Wiring
5. Check all electrical connections
MAINTENANCE SCHEDULE
Operation
Daily
Weekly
Monthly
3 Months
Check Safety Valve
�
Drain Tank (See Figure 6)
�
Check Oil Level
�
Clean or Change Air Filter
�
Check Intercooler (two-stage
compressors only)
�
Clean Unit Components
�
Check Belt Tightness
�
Change Oil (See Figure 5)
�
Change Oil Filter (Pressure
lubricated pumps only)
�
All manuals and user guides at all-guides.com