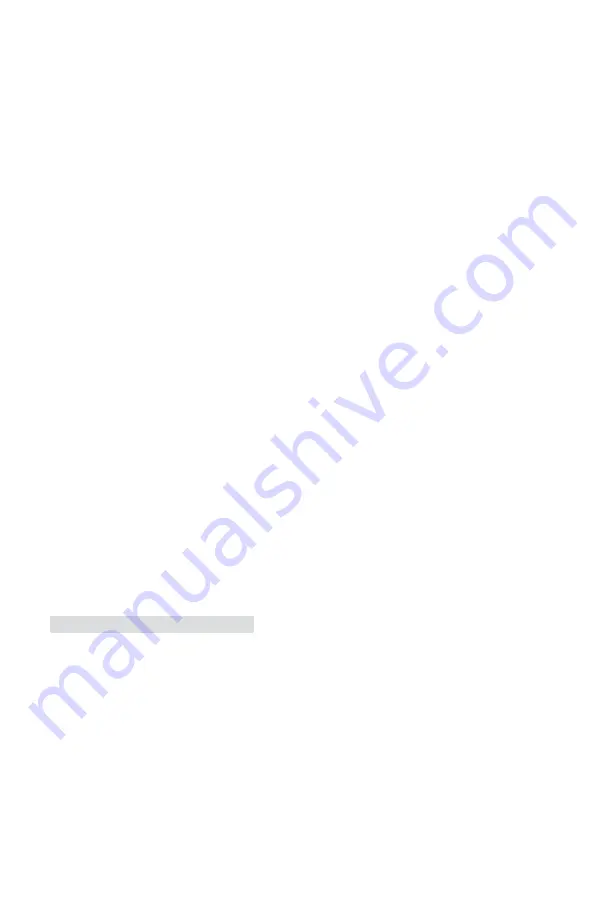
15
b. Calibration Procedure
(continued)
3. Tighten screw on crank to mid-slot position.
4. Turn switch index pointer to “1” (index numbers refer to numbers on
outer edge of scaleplate).
5. Apply 10% differential pressure and adjust switch plate until switch
actuates. Lock the two linkage screws.
6. Rotate index pointer to “9.” Apply 90% differential pressure and adjust
crank radius until switch actuates.
7. Recheck 10% and 90% setpoints. Adjust crank radius and index pointer
until both setpoints are 2% accurate (nominal).
8. If switch is to be field-set at low differential pressure values (1% or 2%
of pressure range), check crank to prevent a top-dead-center position.
Otherwise, minimum setpoint position will be restricted and setpoint
may become reversed.
9. Adjust switch to actuate at desired pressure by applying test pressures in
a decreasing direction, in discrete steps. Allow unit and pressure system
to stabilize. Then change pressure a small amount. The magnitude of
the pressure change is determined by desired accuracy of test. Tighten
lock screw before testing switch performance.
The high switch is usually set to actuate at increasing pressure. There-
fore, when calibrating high switch, apply test pressure in an increasing
direction.
This amount of loading will prevent cam-runout of a similar condition.
Excessive plunger loading (more than 3 flats) may cause roller to drag
on cam. Cam friction will be apparent by excessive hysteresis, erratic
pointer readings and inconsistent switch operation.
10. Check switch deadband, (actuate to reset) by applying differential pres-
sures in a decreasing then increasing (opposite for high switch direc-
tion). Observe pressures. To reduce deadband, advance plunger screw
(two flats maximum).
11. Adjust high switch to actuate at desired pressure. The procedure is the
same as for the low switch.
3-9. Preventative Maintenance
• Indicating Switch — Periodically inspect alarm switch mechanism to
verify that all mounting screws are seated properly. Inspect linkage for
wear. Inspect integrity of electrical circuits. Tighten as necessary.
• DPU —
Warning/Caution notices
, inspection/cleaning procedures, and
maintenance procedures are presented in the Model 199 DPU manual.
Never perform any maintenance/repair on the instrument or DPU
without first reviewing all procedures and Warning/Caution notices in
the DPU manual.