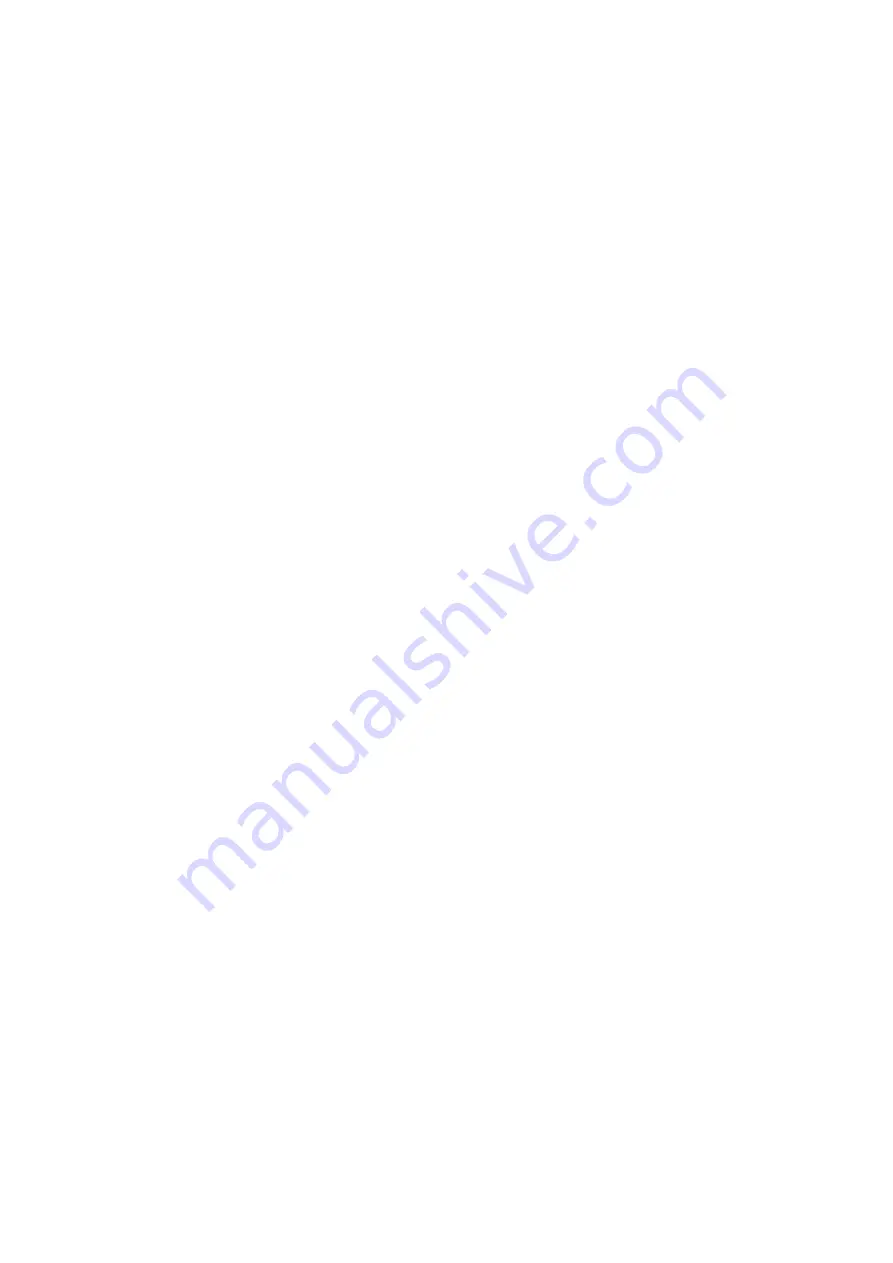
- 18 -
6 COMMISSIONING
6.11
Pre-commissioning checklist:
Before starting the commissioning process the following conditions must be
met. If these conditions are not adhered to, damage to the equipment, system
and property may result.
Ensure the unit is sited in a frost free area, away from precipitation and
water
sprays/jets.
All necessary pipe/electrical connections should have been made to a
satisfactory standard by a qualified person.
The temperature and pressure at the point of connection are within the
operating limits of the pressurisation unit.
The heating/cooling system is fitted with a safety valve and expansion
vessel sized appropriately.
6.12 In order for the pressurisation unit and heating/cooling system to function
correctly the following conditions must be met. If these conditions have not
been met, the commissioning process should not continue.
Ensure the system connection has been made into the heating/chiller
system return header.
Ensure Non-return valves, pressure reducing valves or RPZ valves are
NOT
installed between the pressurisation unit and the heating/cooling system.
The expansion vessel is pre-charged to the correct pressure (equal to
initial system design pressure).
6.13 Prior to commissioning fill the heating/cooling system via a filling loop if
possible. If this is not possible, the pressurisation unit can be used to fill the
system after commissioning has taken place. Depending on the size of the
system, this may take a considerable amount of time. The system fill function of
the unit will stop after 24 hours, if further filling is required, reset this function.
Ensure the heating/cooling system is filled and pressurised to the required
cold fill pressure, with the water at approximately ambient temperature.
Ensure the system is dosed with a suitable corrosion inhibitor. Note the
unit is not designed for dosing chemicals into the system, this must be
done via other means.
6.14
Expansion vessel setting:
To set or check the expansion vessel charge pressure the lock-shield
valve between the pressurisation unit and the vessel must be closed and the
vessel drained using the drain valve.
A suitable gauge should be used to check the charge pressure.
If the charge pressure is too high it can be reduced by releasing air from
the vessel pre-charge valve or by using a pressure gauge with an integral
air release valve.
If the charge pressure is too low a small increase can be provided using a
car foot pump otherwise an oil free compressor or nitrogen bottle is
recommended.
When the correct pressure is set the Schrader valve protective cap must
be
replaced.
Check the integrity of the pipework. Ensure the lock-shield valve between the
system and the expansion vessel is open and the drain valve is closed.
Содержание Unimat-E Series
Страница 35: ...35 Cont NOTES...