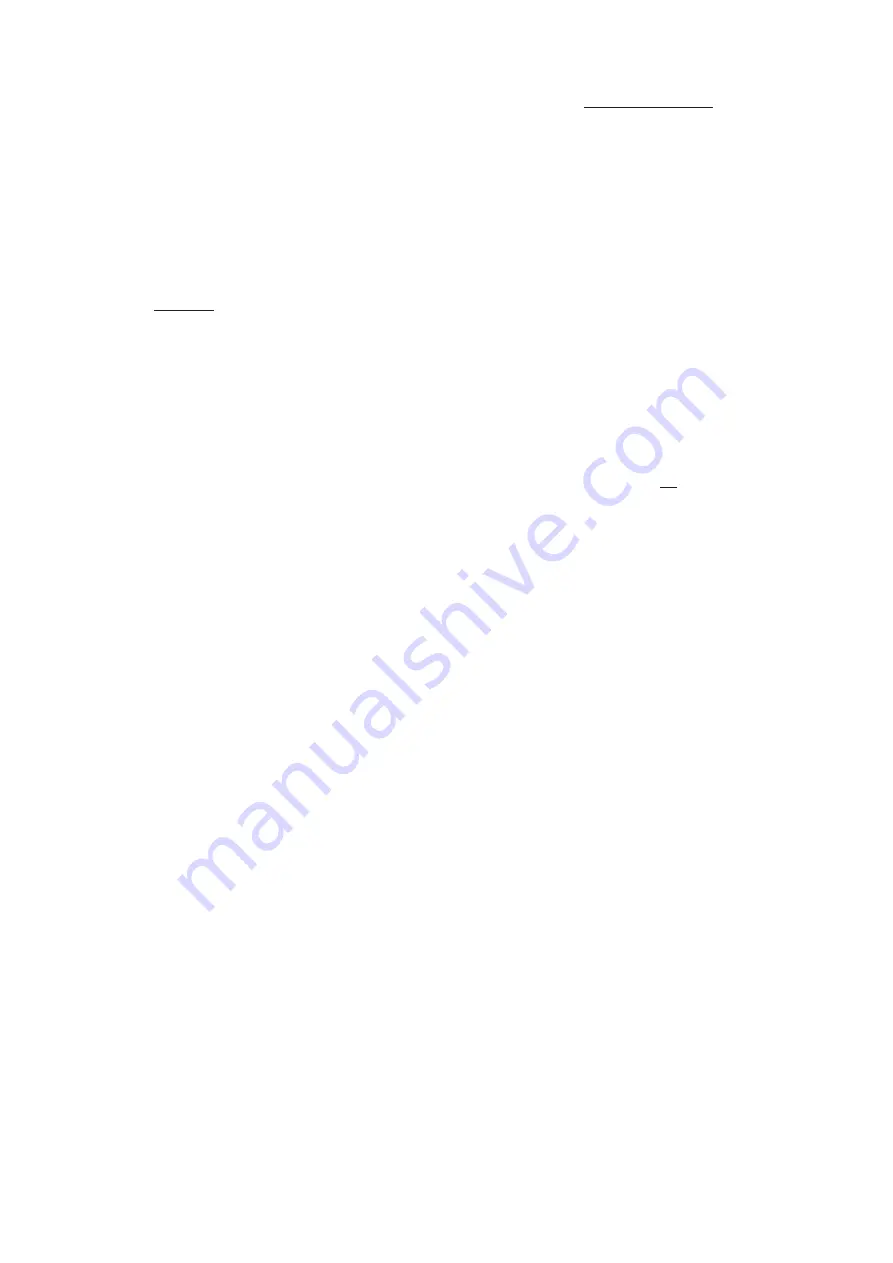
6.5 Replacing the Solenoid
2.
3.
4.
IMPORTANT: In areas where scale can be a problem ,
check that the suspected fault is not due to a blocked
filter
before
replacing the unit . Scale build-up in the filter can
cause intermittent problems.
the pipe will retain a volume
of water that will be released when the connection is
broken.
(this is removable at the inlet to the solenoid)
Remove the silicone hose that joins the solenoid to
the water inlet.
Pull the solenoid from the mounting bracket.
Fit the replacement valve onto the existing mounting
bracket (if a mounting bracket was supplied with the new
valve, remove this first).
1.
NB Do not
over-tighten the drain plug when re-fitting.
Allow the contents of the boiler to cool sufficiently for
the water to be removed safely using the drain plug (see
fig. 7). The body can now be de-scaled
W
arning
IMPORTANT: The correct operation of the boiler relies
on a regulated flow of water from the solenoid valve
and therefore a genuine replacement part supplied by
Calomax must be fitted.
6.6 Checking the overflow screen
Refer to the parts identification drawings on pages
1,2,3 and 4 to identify the location of the overflow
screen
.
1. Remove the P.C.B. and support bracket as one
assembly by releasing the two fixing screws.
3.
. The Overflow screen can be removed by easing
off the silicone tubing at each end. Check the screen for
blockage. The overflow screen can be cleaned or replaced
with a new part (supplied by Calomax) as required.
6.7 Adjusting the Water Temperature Set Point
The temperature potentiometer (Pot) is pre-set at
Calomax and will only require adjustment in
exceptional circumstances.
The temperature adjustment Pot 1 (located at the bottom
left hand corner of the main printed circuit board) controls
the operating temperature of the boiler. ½ turn clockwise
on this device will raise the temperature of the water by
approximately 1 ½ degrees centigrade.
Water boils at
different temperatures depending on barometric
pressure. The temperature should not be tuned
higher than the pre-set 98 degrees, or overboiling
may occur during low barometric pressure
conditions, causing the unit to trip the overheat cut-
out device.
Any adjustments made to the P.C.B should
be noted on the boiler to aid fault diagnosis
if problems persist.
Issue 17
page 8
Issue 17
page 8
7. FAULT FINDING
To protect the unit in the event of continuous over
boiling, the unit is fitted with a thermal cutout device.
This device will cut power to the entire machine and
can be re-set manually. Before re-setting the device,
the cause of the trip.(de-scale required etc.) should
be investigated.
The Service Indicator Light on the front of the machine
and Light Emitting Diodes (LED’s)fitted to the Main PCB,
can be used to diagnose operating problems with the
machine.
Certain types of operational fault will cause the green
'
light, mounted on the front facia,
to flash certain sequences.
SERVICE INDICATOR'
.A
-light pulse generally indicates that the low
level probe requires a de-scale .
A
light pulse indicates a loss of signal from the
normal water level probe causing the unit to overfill,
The probe requires a de-scale.
A
-light pulse indicates the machine has over-
filled due to debris trapped in the solenoid valve. This
is usually solved by drawing
water from the tap,
causing the valve to operate and flush out the
obstruction.
If this does not rectify the
problem, turn off the water supply and clean the
valve’s filter of debris.
A
light pulse indicates the boiler has over filled
due to scale on both the low and normal level sensors.
A
light pulse indicates
L
two
three-
four
five-
six-
The unit can be used normally while the service
indicator is flashing
all
The machine will reset itself once the
problem has cleared.
the machine has over-filled
due to debris trapped in the solenoid valve.(
) but also the low level probe requires a descale.
see four
pulse
For further information contact Calomax ltd direct.
Stating Model, S.No, and fault
symptoms.
ED’s fitted to the Main PCB indicate the operation of
the solenoid and element. The red LED indicates that
the element should be energized and the yellow LED
indicates that the solenoid should be energized.
The switching of the element and solenoid is all solid
state, driven by the PCB’s .In all cases the power to the
element and solenoid is switched through the neutral
connection.