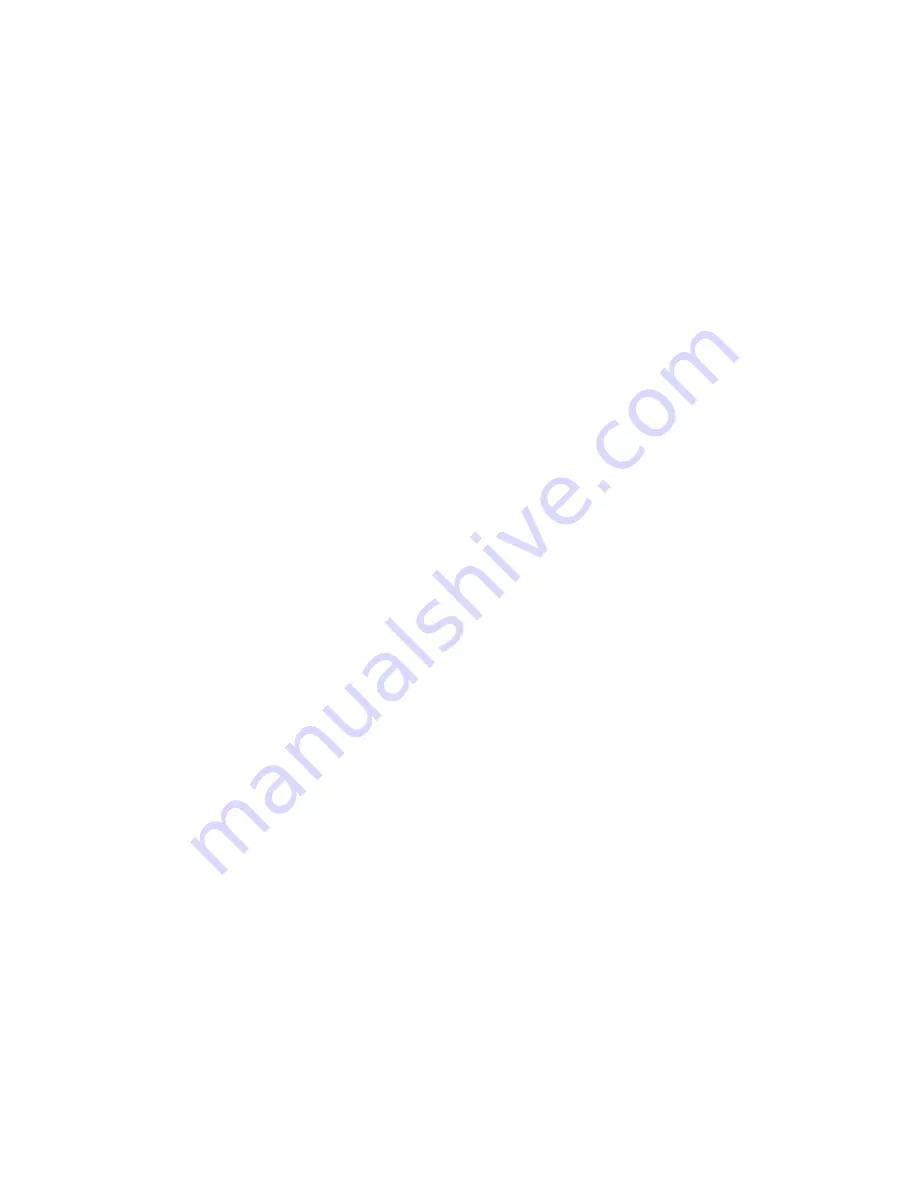
Revised 14 June 2003
4
Note:
Tape is best removed by unwinding. This will result in a minimum of tape
residue on antenna elements. Tape residue on elements can be removed
with mineral spirits or WD-40.
JOINING PIECES:
Except for the feed point, which is joined to the fiberglass, assemble joints as follows:
1. Clean any dirt, dust, or tape residue from the outer surface of the smaller diameter
tubing to be joined. To the extent possible, also clean the inside surface of the larger
tube. Tape residue may easily be removed with WD-40 or mineral spirits on a piece
of rag or paper towel, then the residue of either of those solvents is removed with
Acetone.
2. Use the supplied Scotch-Brite pad to clean the surface of the part of the tube to be
mated. This cleaning will produce a uniform, matte finish.
3. Wipe down with Methyl Ethyl Ketone (MEK) (preferred) or Acetone. Either of these
is available from most hardware stores in pint cans. Please read and understand the
warnings on the container regarding use of these solvents.
4. Apply the supplied silicone grease, working it into the cleaned surface thoroughly.
The amount of silicone grease needed is just enough to create a film between the two
pieces of metal.
Note:
The grease, which is an insulating dielectric, serves to prevent galling, to
exclude moisture from between the metal pieces at points of contact, and
to protect the electrical connection from oxidation. We recommend using
pure, heavy silicone grease for this purpose. Contact between element
pieces is between the aluminum. The grease will be forced from any
areas where contact is made. But it will remain and protect the regions
which are not in contact. Conductive materials in the grease are neither
required nor desirable. Joint compounds containing copper, such as
Penetrox B, should never be used for joining aluminum.
Note:
Because freshly cleaned aluminum immediately begins to re-grow its
protective oxide coating, it is important to apply the silicone grease within
a few minutes of cleaning. For this reason, it may be necessary to clean,
grease, and fasten just one or two joints at a time.
5. After treatment, assemble the pieces by sliding them together, with a rotary motion if
necessary. Be careful not to allow any dirt or grit into the joint.
6. Carefully align the holes, hand-marked legend to legend. A tapered pin or small-
diameter punch may be useful for the initial alignment of the holes. For riveted joints,
place rivets in all holes before setting any of them. Then set them. Rivets will have
from an easy slide fit to a snug fit. Excessive play indicates the wrong size rivet.
Holes for the larger (5/32” diameter) rivets have the part number of the correct rivet
to be used marked in red on the swaged portion of the tubing. The remaining smaller
(1/8” diameter) holes all take AD-42H rivets.