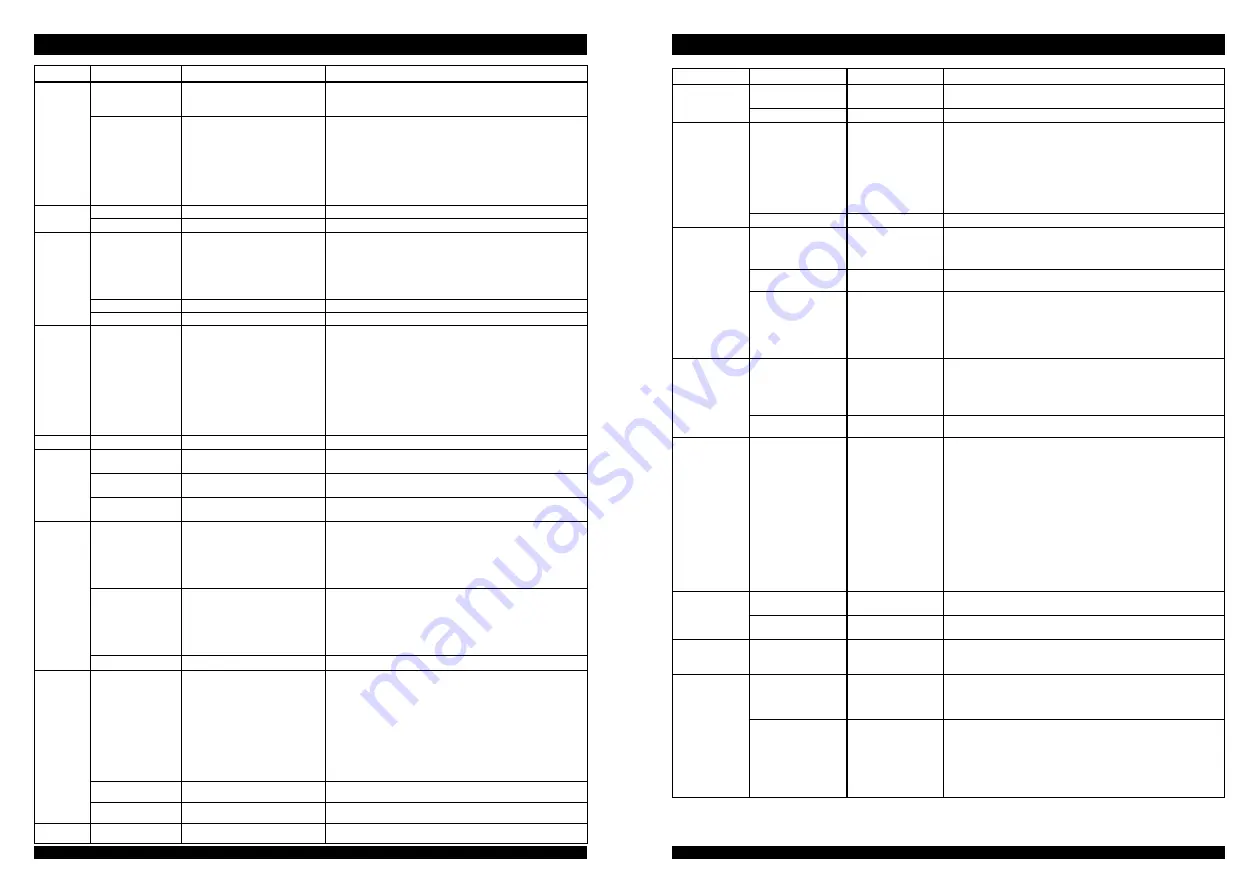
MAINTENANCE
OPERATOR MANUAL
66
EPS14P
67
OM-EPS14P2019001-EN
Display
ALARM
Fault name
Recommended inspection
02A68
SMARTDRIVER KO
Drive of electromagnetic brake
fault
Check whether the high end (CNB#1) of the drive of
electromagnetic brake is short circuited to the terminal B-.
If not, the internal drive module could be damaged.
W A I T I N G F O R
NODE
Waiting for signal from a node
In the CAN communication network, a certain controller
has received the signal that another controller cannot
communicate normally. The said certain controller hence
remains waiting until the whole CAN communication
network reverts to normality. Check the controller that
cannot communicate normally for failed connection. Check
whether the software version or parameter settings are
correct.
02A70
encoder error
Encoder fault
Check the motor encoder
EPS RELAY OPEN
EPS relay open
Check whether the EPS controller has fault
02A71
EEPROM KO
Memory is damaged
Forklift does not travel. Parameter storage becomes faulty
so that forklift stops operation. Operate the key switch for
several times. If the fault still exists, replace the logic card.
If the fault disappears, parameters previously stored have
been replaced by wrong parameters. It is imperative to set
the parameters again.
HANDBRAKE
handbrake
02A72
VMN LOW
VMN low
Cause: When the motor is turned on, the high-end voltage
of MOS tube is less than 66% the capacitor voltage, or
when the motor is running, the high-end voltage of MOS
tube is less than the requirement. Possible causes:
1.Incorrect phase connection or faulty circuit of the motor.
Check the motor for incorrect phase connection. Check
the motor for current leakage to the ground. Check the
motor for broken coil.2.Check whether the main contactor
engages securely. Check the contacts for wear.
3.Replace the controller.
02A73
sens.Motor temp.ko Motor temperature sensor error Check harness of motor temperature sensor.
02A74
DRIVER SHORTED
Short circuit of contactor
Check whether there is short circuit in the coil output from
the controller. If not, replace the controller
AUX BATT.SHORT.
Fault with auxiliary drive voltage Check whether BI is correctly connected to B5. If so, replace
the controller;
DRV.SHOR.EV
Short circuit of EV cable
Check whether the low end of EV1/EV2/EV3 is short
circuited to B-. If not, it is required to replace the controller;
02A75
C O N T A C T O R
CLOSED
Contacts of contactor get stuck
Before energizing the coil of main contactor, the controller
will check whether the contacts of main contactor get stuck.
Attempt to discharge the capacitor. If the capacitor voltage
is reduced by 20% the battery voltage, the fault could exist.
1. Check whether the contacts of the contactor get stuck. If
so, replace the contactor.
CONTACTOR DRIV-
ER
Short circuit of drive
With the key switch turned to “ON”, the microprocessor
will check the drive of main contactor for short circuit. In
case of short circuit, the warning will be displayed. Check
whether the positive terminal of coil of main contractor is
short circuited to A16 or negative terminal of power supply.
If externality is normal, replace the controller.
CONT.DRV.EV
EV drive of the controller is inoperable
Replace the controller;
02A76
KEY OFF SHORTED Short circuit of the key switch
In the startup phase, if the controller detects a low logic level when
the key switch is turned to “OFF”, this fault will be displayed. Fault
analysis: A highly possible cause is voltage being too low. Perform the
following checks. -Key switch based external load (for example, turning
on the DC-DC converter. Relay or contactor switch input signal lower
than startup voltage).-Check the connections of the power supply
cables to the positive and negative terminals of the battery, and to
the terminals -BATT and + BATT terminals of the main contactor and
controller. The screws shall be tightened to torque 13Nm to 15Nm.-If
no voltage drop in the power supply circuit is detected, this fault will be
reported each time the key switch is turned to “ON”. The hardware of
controller could become faulty. It is necessary to replace the controller.
COIL SHOR.MC-EB
Main contactor or elec-tromagnetic
brake is heavily loaded
1. Check whether the output and load of the controller are excessive; 2.
Replace the controller;
COIL SHOR.EV.
PEV coil fault
Fault with the PEV drive coil. Check whether the PEV drive coil
connection or the coil itself are in good conditions;
coil shorted
Short circuit of coil
Check whether there is short circuit of main contactor coil and oil pump
contactor coil
Display
ALARM
Fault name
Recommended inspection
02A77
CONTACTOR OPEN
Main contactor open 1. Broken circuit of main contactor coil. 2. Main contactor
damaged
end teach ko
Not used in BYD system
02A78
VACC NOT OK
Accelerator fault
Inspection time: With the forklift idling, the accelerator voltage is at
least 1V higher than the minimum set in the “PROGRAM VACC”
menu for accelerator signal range.
Possible causes:
1.Upper and lower limits of accelerator voltage are not taken. Move
to the PRPGRAM VACC menu to take the limits again.
2.Accelerator error. Possible cause is that accelerator pedal failure to
return to original position, or internal error of accelerator.
3.Controller fault.
Possible causes:
02A79
INCORRECT START
Star tup sequence
fault
Incorrect startup sequence. Possible causes:
1.The direction switch has already been turned on before the motor is
turned on.2.Operation sequence error.3.Incorrect wiring connection.
4.If the fault cannot be eliminated, replace the controller.
WRONG STEER PAR.
PUMP INC START
Oil pump startup se-
quence fault
Incorrect oil pump startup sequence. Possible causes:
1.The “LIFT” or “TILT” switch has already at the “ON”
position before the forklift is started.
2.Operation sequence error.
3.Incorrect wiring connection.
4.If the fault cannot be eliminated, replace the controller.
02A80
FORW + BACK
Forward and reverse
signals exist at the
same time (direction
switch gets stuck)
The controller can keep checking for this fault. Having detected
that request signals in the two directions occur at the same
time, the controller will issue a warning. Possible causes:
1.Wire damaged2.Direction switch fault3.Improper operation
4.If the fault cannot be eliminated, replace the controller
EMERGENCY
02A82
ENCODER ERROR
Encoder fault
The controller detects that two successive speed readings of the
encoder differs greatly from each other. A normal encoder in
the system cannot change speed readings greatly within a very
short time. Hence, a possible cause for the symptom is that the
wires of one or more encoders are worn or broken. Check the
mechanical and electrical parts of the encoder. Another possible
for the symptom is electromagnetic interference from the
sensor bearing. If the symptom is not due to the two causes,
replace the controller.Note: Sometimes manual operations may
also cause this fault indicating on the controller. In these cases,
it is required to turn off power supply and start the forklift
again. For example:1.The forklift suddenly collides with an
obstacle so that it is incapable of travelling;2.The driver applies
the brake sharply while the forklift is travelling at a high speed.
02A84
CAN BUS KO BMS
BMS communication
fault
Check whether the BMS communication line operates normally.
canbus ko bms
BMS communication
fault
Check CAN communication wire
02A85
VACC OUT RANGE
Accelerator input
i s o u t s i d e t h e
permissible range.
1. Upper and lower limits of accelerator voltage are not correctly
taken. Move to the PRPGRAM VACC menu to take the limits
again; 2. Check whether the accelerator connection is correct;
02A86
PEDAL WIRE KO
Fault with connection
o f p o s i t i v e a n d
negative terminals of
accelerator
Check whether the positive and negative terminals of the
accelerator have been connected to the controller;
POS.EB.SHORTED
High end of drive
of electromagnetic
b r a k e p r o v i d e s
output earlier than
expected
High end of drive of electromagnetic brake outputs high voltage
with the interlock not engaged. 1. Check whether another high
voltage circuit is connected to the high end output connector
of electromagnetic brake; 2. If the high end output connector
of electromagnetic brake is not connected but high voltage
still exists, the drive circuit in the controller has already been
damaged;
Содержание EPS14P
Страница 1: ...EPS14P OPERATOR MANUAL OM EPS14P2019001 EN...
Страница 2: ...EPS14P OPERATOR MANUAL OM EPS14P2019001 EN...
Страница 38: ......