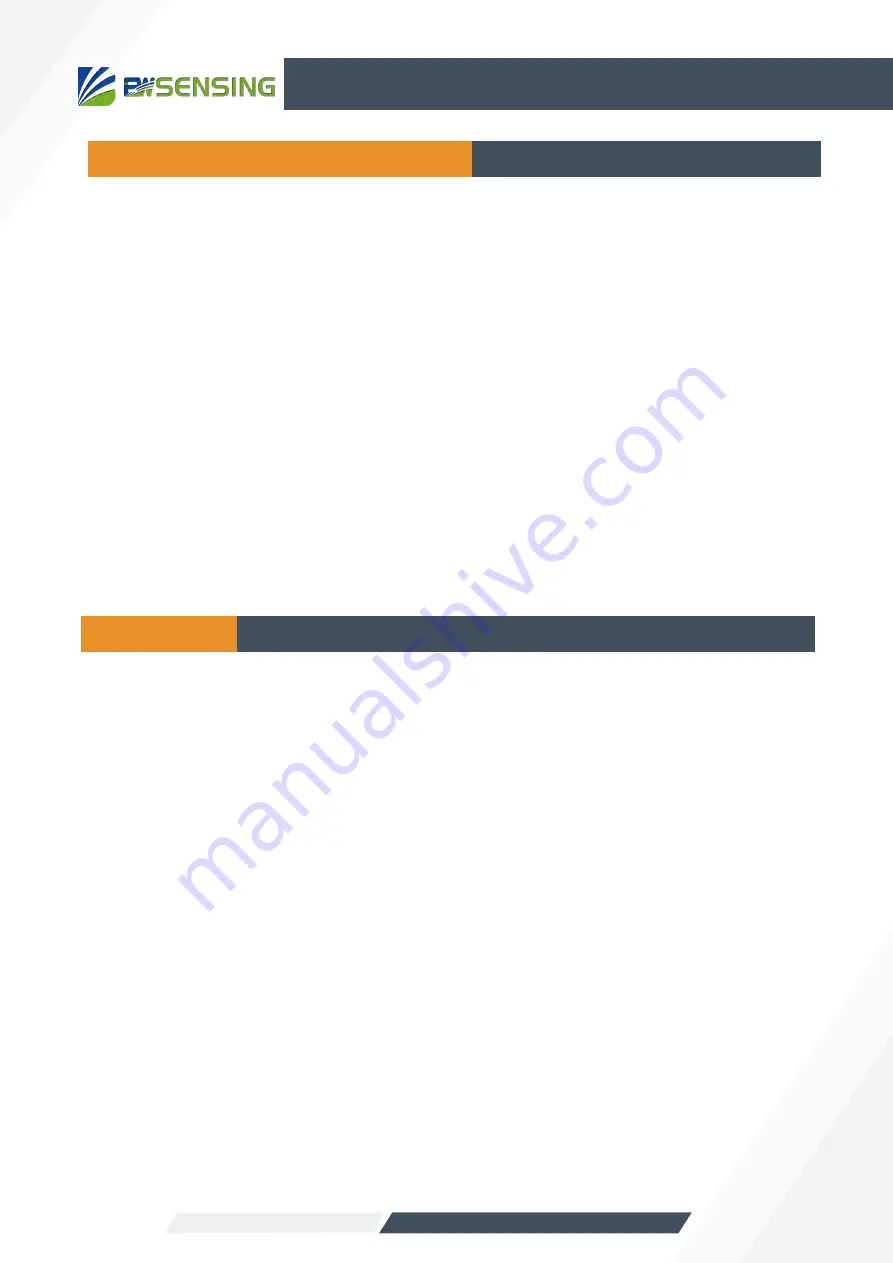
BMR3000
Three-Axis Accelerometer Three-Axis Magnetometer
High Accuracy
Electronic Compass
Calibration
Method 1 - Plane calibration:
1.
Fix the electronic compass in the use environment, and try not to carry magnetic items such as keys
and mobile phones during calibration;
2.
Connect the product to the system and put it in a horizontal state
(within ±5°)
;
3.
Open the serial debugging assistant and send the start calibration command in hexadecimal format:
77 04 00 11 15;
4.
Rotate the product 2-3 turns around the z-axis (the vertical direction of the z-axis) in the horizontal
plane (with the pitch angle and roll angle within ±5°). The rotation process should be as slow as
possible and rotate at a uniform speed. The time of one rotation is about 10~15 seconds;
5.
Rotate the product about 2-3 turns around the X-axis or Y-axis. The rotation process should be as
slow as possible and rotate at a uniform speed. The time of one rotation is about 10~15 seconds.
6.
Complete the calibration and send the save calibration command: 77 04 00 12 16.
The main sensitive components of the
BMR3000
sensor are magnetometers and accelerometers.
The compass uses a magnetometer to sense the geomagnetic field to calculate the direction of the
sensor. The accelerometer is used to measure the angle between the compass and the gravity, and
provides the tilt compensation when the compass calculates the azimuth. The earth's magnetic
field is easily interfered by the external magnetic field. Users should pay attention to the surrounding
magnetic field during installation to ensure that the sensor is exposed to the earth's magnetic field
and avoid using it near ferromagnetic materials and changing magnetic fields, Such as engines,
iron plates, iron bolts and nuts, wires, motors, speakers, antennas, etc. It is important to strictly avoid
magnets, motors and other strong magnetic substances within 10cm of the compass, which may
cause the measurement accuracy of the compass to irreversibly
decrease.
We strongly recommend
magnetic field calibration after installation and every time the magnetic field environment
changes. After the calibration in accordance with the manual, the firmware and program in the
BMR3000
can effectively eliminate the interference of the magnetic field. As long as the position
of the compass and the surrounding magnetic field environment have not changed, it is no longer
necessary to compensate the sensor.
Tests have shown that if the user performs the calibration operation according to the requirements of
the user manual so that the compass can meet the above requirements during installation and
correctly calibrate the sensor, the heading accuracy of the sensor will be less than 0.5 degrees (RMS).
The recommended test method is to mount the
BMR3000
sensor horizontally on a
non-
magnetic material away from interference for heading angle measurement. Avoid extra
magnetic field interference during measurement.
Measurement & Installation
The electronic compass has been calibrated at the factory. In places where the influence of the
magnetic field environment is small, it is not necessary to perform environmental calibration and can
be used directly. During actual use, it is recommended to perform calibration.
Azimuth calibration step
:
Bewis
Sensing
Technology
LLC
www.bwsensing.com Tel
:
+
86
189 0617 7922