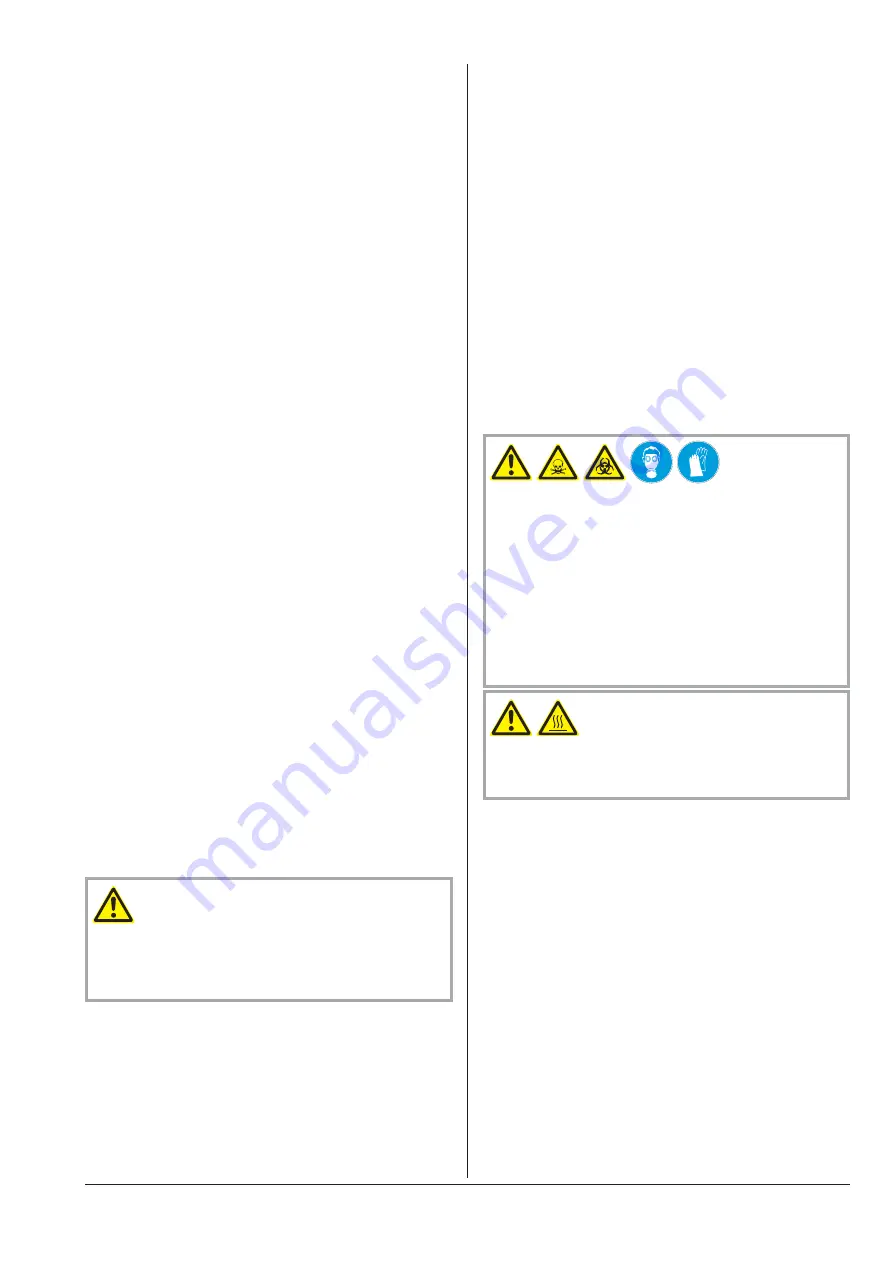
Setting Operating Conditions
Selection of Operating Liquid
Water is usually used as operating liquid for the conveyance of air and
other inert gases. Other ring liquids may be used in order to comply
with the selected gases and separation methods.
The kinematic viscosity at operating temperature shall not exceed
2 mm²/s. Higher viscosities require increased drive power. The vapour
pressure of the ring fluid in case of vacuum operation shall not exceed
16 mbar. Higher vapour pressures deteriorate the suction capacity and
the ultimate pressure as stated in the performance tables or curves
resp. In case of use of ring liquids other than water confirmation of the
vacuum pump’s conveying characteristics shall be sought from Busch.
If liquids get conveyed together with the process gas (three to five
times the quantity of the circulating liquid rate as given in the
datasheet) the addition of fresh liquid can be reduced significantly.
Condensation of vapour inside the vacuum pump can cause cavitation
and destroy components of the vacuum pump. Condensation up-
stream of the vacuum pump (jet or surface condenser) shall therefore
be preferred. Under certain conditions the accumulating condensate
can be conveyed along by the vacuum pump. Otherwise a separate
liquid pump must be provided for. The design shall be performed by
the manufacturer/supplier.
The suction capacity (or volume flow) as given in the performance ta-
ble is achieved at an operating water temperature of 15 °C. Operation
at higher water temperatures leads to a reduced suction capacity (or
volume flow), but leaves the option to save fresh water or cooling liq-
uid in case of open or closed circuit cooling. This liquid rate shall be set
by means of the regulating valve r
F
or r
B
only to such a quantity, that
the required suction capacity (or volume flow) is achieved. The regulat-
ing valve shall be locked in this position.
Fresh Water Requirement
Fresh water flow rate requirements are shown in the technical data
section
Ú
page 25. The data given applies to once through operation.
These water flow rates result in approximately a 5.5 °C rise in tempera-
ture for a single stage vacuum pump, and a 2.7 °C rise for a two stage
vacuum pump when handling dry air. Condensable vapours in the gas
stream, however, will add to the heat load and cause a higher temper-
ature rise through the vacuum pump.
Partial recovery flow rates may be reduced by up to 50 percent de-
pendant upon temperature rise through the vacuum pump (see above
comment).
If operating speed is varied from the given values, the flow rate re-
quirements vary accordingly.
Operating Liquid Level
Note
: The options to check the level depend on the installation. In case
the installation provides no means for level check, undo the plug (b).
Excess operating liquid will then flow out of the port. If necessary fill in
operating liquid, until it reaches the bottom edge of the port. Reinsert
the plug (b) prior to starting the vacuum pump.
CAUTION
_a
Starting the vacuum pump with a completely flooded housing can
bend the blades of the rotor.
The operating liquid shall reach the middle of the shaft only when
the vacuum pump is to be started.
●
Make sure that the operating liquid reaches the middle of the shaft
when the vacuum pump is to be started
Pressure Control
At very low pressures and sufficiently high temperatures the operating
liquid can locally transfer into the vapour phase, creating bubbles
within the operating liquid. As the pressure rises towards the outlet slot
the bubbles collapse. This process is called cavitation. In case of bub-
bles that have been located on surfaces the operating liquid cannot in-
trude the cavity left by the bubble equally from all directions. Instead
the inflowing liquid hits the surface with high speed. This causes ero-
sion, which can destroy the vacuum pump rapidly. The formation of
bubbles also deteriorates the pump performance. Cavitation is clearly
audible by its crackling noise.
The working pressure of the vacuum pump shall therefore be suffi-
ciently above the vapour pressure of the operating liquid. In particular
the pressure control in the vacuum system must by no means be
achieved by throttling or even closing of the suction line!
The vapour pressure of the operating liquid and consequently the ulti-
mate pressure can be reduced by cooling. However, this increases the
cooling water flow considerably. In most cases the low ultimate pres-
sure is not required and cavitation shall be avoided by means of vac-
uum limitation rather than cooling.
Removing Contaminations and Deposits
●
In closed operating liquid circuits with water use softened water
●
Make sure that no dirt particles with a diameter larger than
0.1 mm will intrude the vacuum pump, neither via the process gas
nor via the operating liquid. Filter out larger dirt particles before
the vacuum pump.
The dirt concentration shall not exceed 5 volume percent.
Maintenance
DANGER
_age32
In case the vacuum pump conveyed gas that was contaminated
with foreign materials which are dangerous to health, harmful ma-
terial can reside in filters.
Danger to health during inspection, cleaning or replacement of fil-
ters.
Danger to the environment.
Personal protective equipment must be worn during the handling
of contaminated filters.
Contaminated filters are special waste and must be disposed of
separately in compliance with applicable regulations.
CAUTION
_ac
During operation the surface of the vacuum pump may reach tem-
peratures of more than 70 °C.
Risk of burns!
●
Prior to disconnecting connections make sure that the connected
pipes/lines are vented to atmospheric pressure
Maintenance Schedule
Monthly:
●
Check for audible abnormal noise, e.g.:
–
Excessive rumble (possible cavitation problem)
–
Periodic click/knock (possible mechanical contact / bearing degra-
dation)
Version with mechanical seals:
–
Mechanical seal squealing noise (possible lack of lubrication)
●
Check for excessive vibration
Vibration should be less than 5.5 mm/s RMS when measured in
the axial, vertical radial and vertical horizontal planes on the bear-
ing housing.
High vibration could indicate a coupling misalignment, fixing bolt
looseness or bearing degradation.
●
Check the operating liquid temperature
(with a hand held probe or a permanent gauge, if fitted; consult
LA 0053-1111 A, LB 0063-1011 A
Maintenance
0870150638 / 091222
page 10
Содержание DOLPHIN LA 0053-0143 A
Страница 1: ...0870150638 A0001 26 10 2021 Original instructions DOLPHIN LA 0053 1111 A DOLPHIN LB 0063 1011 A ...
Страница 20: ...LA 0053 1111 A LB 0063 1011 A Sectional Drawings and Spare Parts Lists 0870150638 091222 page 19 ...
Страница 22: ...LA 0053 1111 A LB 0063 1011 A Sectional Drawings and Spare Parts Lists 0870150638 091222 page 21 ...
Страница 24: ...LA 0053 1111 A LB 0063 1011 A Sectional Drawings and Spare Parts Lists 0870150638 091222 page 23 ...
Страница 27: ......