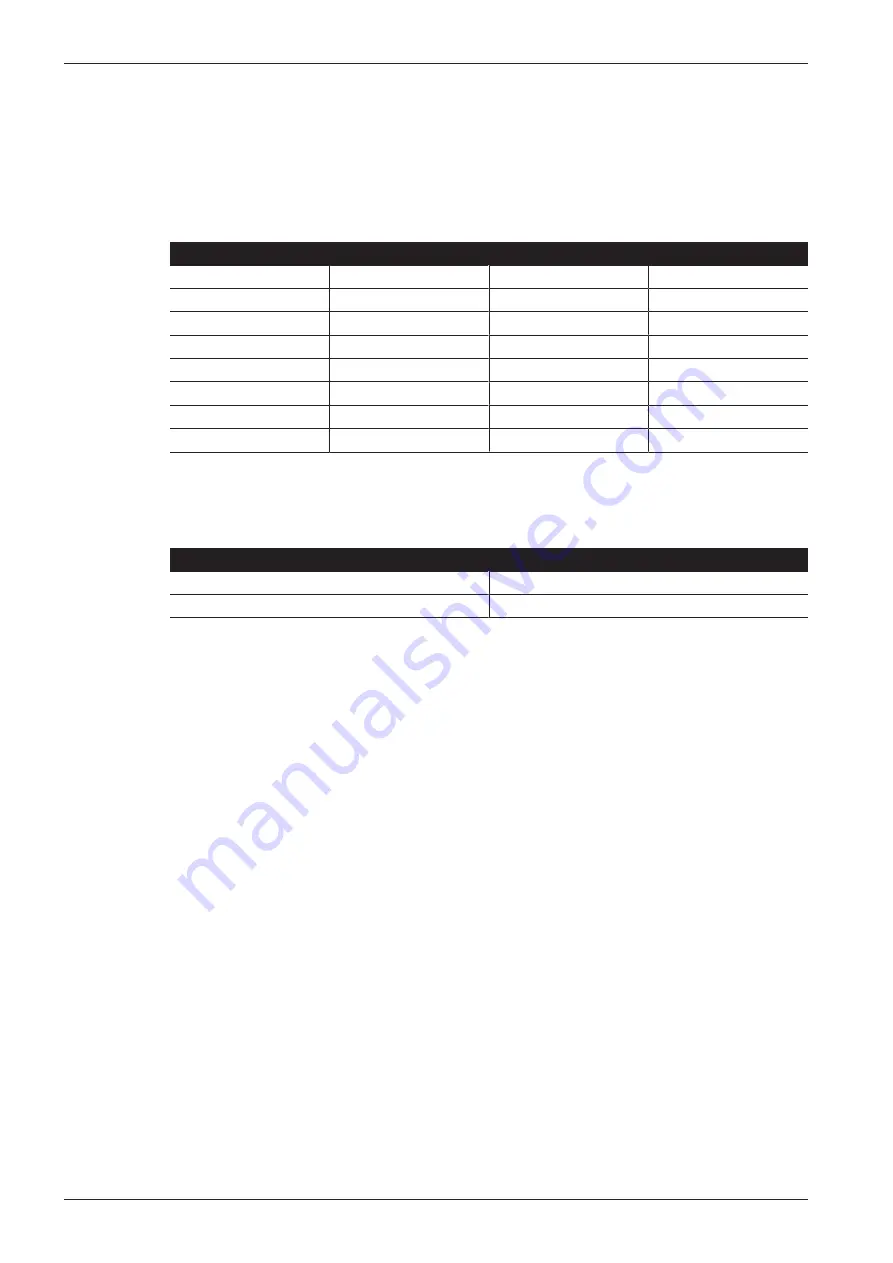
7 | Input / Output Description
26 | 44
Pump Control Instructions INVEOR VFD R5 COBRA_EN_en
7.5
Speed Control via Digital Inputs
7.5.1
Description
This operating mode allows control of the frequency drive with up to 7 configurable fixed
frequ one more for the minimum frequency. Depending on the number of fixed frequencies
required, up to 3 digital inputs are
permanently assigned
:
Frequency
Digital input 3
Digital input 2
Digital input 1
Minimum frequency
0
0
0
Frequency 1
0
0
1
Frequency 2
0
1
0
Frequency 3
0
1
1
Frequency 4
1
0
0
Frequency 5
1
0
1
Frequency 6
1
1
0
Frequency 7
1
1
1
7.5.2
Speed Control: 1 Fixed Fre Min. Frequency
In this configuration, if the "Digital Input 1" is permanently assigned to the frequency selection:
Frequency
Digital input 1
Minimum frequency
0
Frequency 1
1
1.100 Control mode
Selecting the operation mode, following software enabling (1.131) and hardware enabling, the drive
controller runs as follows:
2 = preset speed in inverter software, with the frequencies defined in parameters 2.051 and
Minimum frequency
2.050 Preset speed mode in software
0 = Digital Input 1
►
preset Frequency 1 (2.051)
2.051 Preset speed 1 in software
XX = Set the frequency, it could not be lower than minimum speed and higher than maximum speed.
1.020 Minimum speed
This parameter must not be changed, risk of damage to the machine!