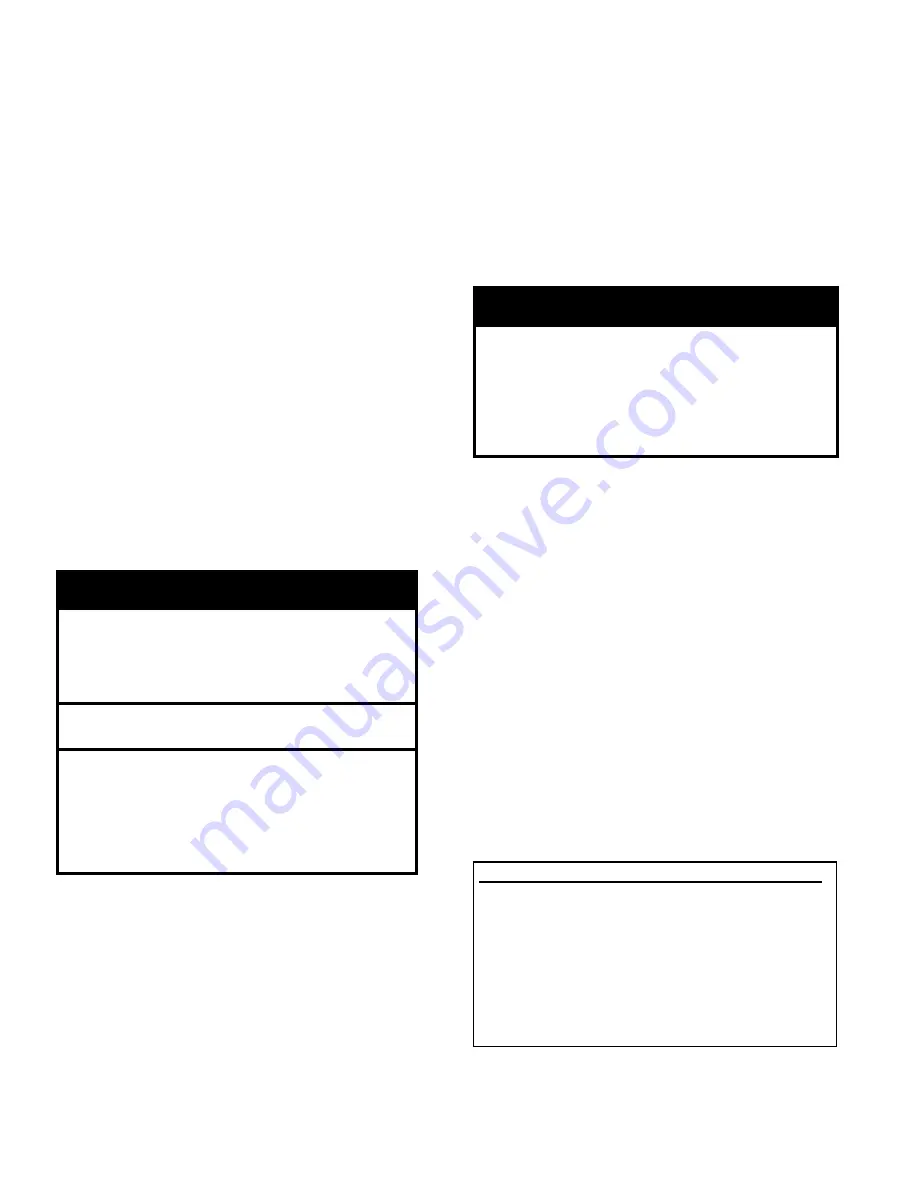
48
k. Drain the system in a manner and to a location
that hot water can be discharged with safety.
l. Remove plugs from all available returns and
wash the water side of the boiler as thoroughly as
possible, using a high-pressure water stream.
m. Refill the system with fresh water.
3. Add appropriate boiler water treatment compounds
as recommended by your local qualified water
treatment company.
4. Make pH or Alkalinity Test.
After boiler and system have been cleaned and
refilled as previously described, test the pH of the
water in the system. This can easily be done by
drawing a small sample of boiler water and testing
with hydrion paper which is used in the same
manner as litmus paper, except it gives specific
readings. A color chart on the side of the small
hydrion dispenser gives the reading in pH. Hydrion
paper is inexpensive and obtainable from any
chemical supply house or thru your local druggist.
The pH should be higher than 7 but lower than 11.
Add some appropriate water treatment chemicals, if
necessary to bring the pH within the specified range.
With this lower level of protection, care must be
exercised to eliminate all of the free oxygen in the
system.
5. Boiler is now ready to be put into service.
IMPORTANT
IF, DURING NORMAL OPERATION, IT IS
NECESSARY TO ADD MORE WATER PER
MONTH THAN INDICATED BELOW, CONSULT A
QUALIFIED SERVICE TECHNICIAN TO CHECK
YOUR SYSTEM FOR LEAKS.
EXCESSIVE WATER ADDITION:
(Gal/Month)
V903A
16½
V908A 44
V904A
22
V909A 49½
V905A
27½
V910A 55
V906A
33
V911A 60½
V907A
38½
V912A 66
H.
FREQUENT WATER ADDITION
A leaky system will increase the volume of make-up
water supplied to the boiler which can significantly
shorten the life of the boiler. Entrained in make-up
water are dissolved minerals and oxygen. When the
fresh, cool make-up water is heated in the boiler the
minerals fall out as sediment and the oxygen escapes
as a gas. Both can result in reduced boiler life. The
accumulation of sediment can eventually isolate
the water from contacting the cast iron. When this
happens the cast iron in that area gets extremely hot
and eventually cracks. The presence of free oxygen
in the boiler creates a corrosive atmosphere which, if
the concentration becomes high enough, can corrode
the cast iron through from the inside. Since neither of
these failure types are the result of a casting defect, the
warranty does not apply. The maintenance of system
integrity is the best method to prevent these types of
failure.
I.
OXYGEN CORROSION:
WARNING
Oxygen contamination of the boiler water
will cause corrosion of iron and steel boiler
components, and can lead to boiler failure.
Burnham’s standard warranty does not cover
problems caused by oxygen contamination of
boiler water or scale (lime) build-up caused by
frequent addition of water.
There are many possible causes of oxygen
contamination such as:
a. Addition of excessive make-up water as a result
of system leaks.
b. Absorption through open tanks and fittings.
c. Oxygen permeable materials in the distribution
system.
In order to insure long product life, oxygen sources
must be eliminated. This can be accomplished
by taking the following measures:
a. Repairing system leaks to eliminate the need for
addition of make-up water.
b. Eliminating open tanks from the system.
c. Eliminating and/or repairing fittings which allow
oxygen absorption.
d. Use of non-permeable materials in the
distribution system.
e. Consult your local water treatment specialist for
specific recommendations.
Recommended Water Quality Requirements
pH - 8.3 - 10.5
TDS - 3500 ppm (Max)
Total alkalinity ppm as CaCO
3
- 1200 (Max)
Total copper ppm - .05
Oily matter ppm -1
total harness ppm -3
chlorines - < 50 ppm
Содержание operating and
Страница 2: ...2 ...
Страница 8: ...8 Section I General Information Figure 1 Dimensional Information ...
Страница 21: ...21 Figure 16 Bare Boiler Assembly ...
Страница 25: ...25 Figure 22 V9A Series Jacket Assembly Boiler Models V903A thru V912A ...
Страница 31: ...31 Figure 26 V9A Series Minimum Piping Parallel Water Boiler ...
Страница 32: ...32 Figure 27 V9A Series Minimum Piping Primary Secondary Water Boiler ...
Страница 33: ...33 Figure 28 V9A Series Minimum Piping Details Bypass with Blend Pump Water Boiler ...
Страница 34: ...34 Figure 29 V9A Series Minimum Piping Primary Secondary with Bypass Water Boiler ...
Страница 35: ...35 Figure 30 Minimum Piping Details Multiple Boiler Application Primary Secondary Piping With Bypass ...
Страница 36: ...36 Figure 31 Minimum Piping Details Multiple Boiler Application Parallel Piping With Blend Pump ...
Страница 37: ...37 Figure 32 Minimum Piping Requirements For Gravity Return V9A Series Steam Boilers ...
Страница 38: ...38 Figure 33 Typical Steam Piping Arrangement for Boilers with Pumped Condensate Return and Boiler Feed Unit ...
Страница 42: ...42 Figure 37b DHW Generation with Tankless Coils Storage Tank and Destratification Pump ...
Страница 43: ...43 Figure 37c DHW Generation with Indirect Water Heater ...
Страница 56: ...56 SECTION VII REPAIR PARTS Continued Figure 39 V9A Series Jacket Assembly Boiler Models V903A thru V912A ...
Страница 58: ...58 Figure 40 Bare Boiler Assembly ...
Страница 62: ...62 SERVICE RECORD DATE SERVICE PERFORMED ...
Страница 63: ...63 SERVICE RECORD DATE SERVICE PERFORMED ...
Страница 64: ...64 ...