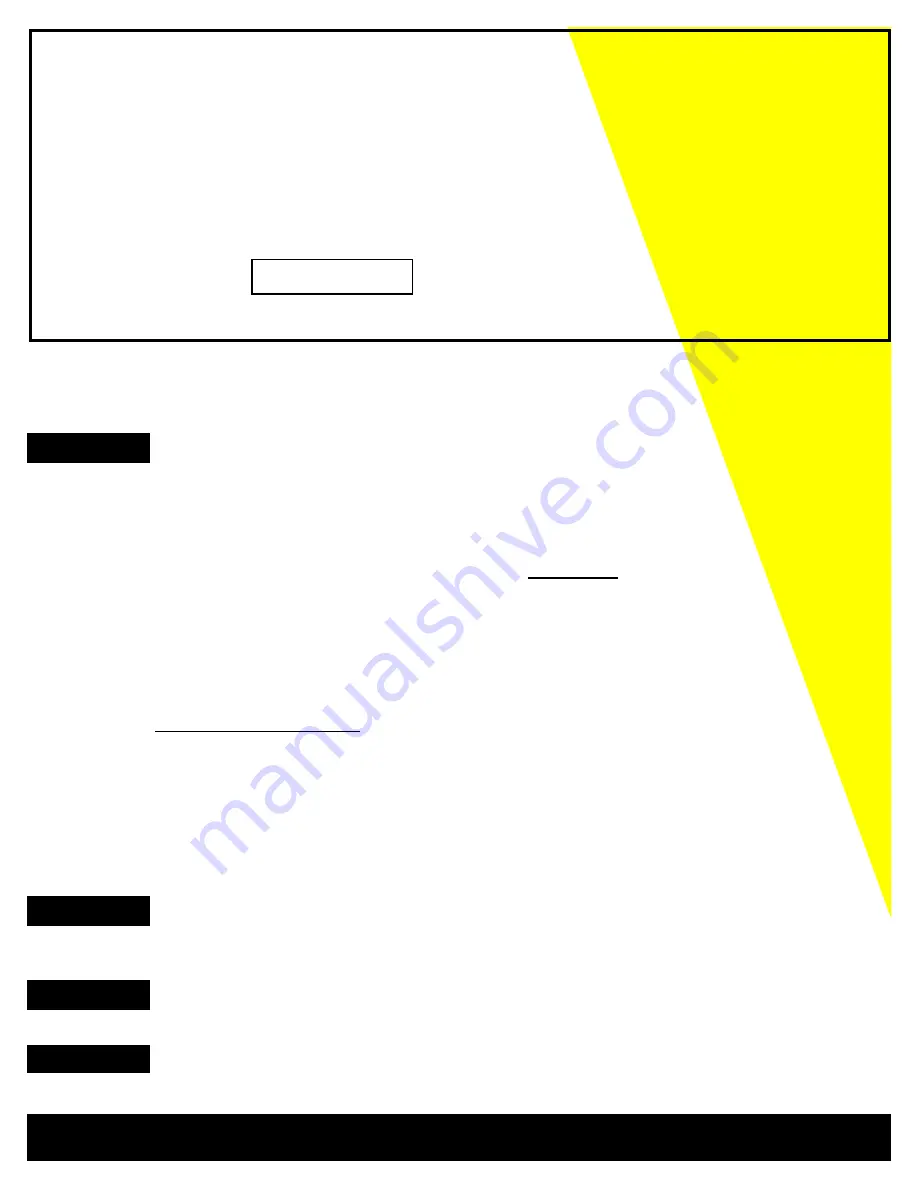
FOR INFORMATION TEL: 514.337.4415 FAX: 514.337.4029
3
APPLICATIONS
Designed for a permanent installation for homes
and cottages application.
To pumping where the total head requirements
do not exceed 15 feet, including pipe friction
losses.
CAPACITY:
20’
1400 US GPH
40’
1200 US GPH
60’
1000 US GPH
80’
750
US GPH
FEATURES
Vortex designed impeller made from noryl,
will not corrode.
Rugged cast iron pump body.
Stainless steel mechanical rotary type motor
seal.
2” NPT pump discharge.
Thermal and overload protection.
Mechanical type float switch, 15A.
4/10HP, 115VAC, 60Hz, 4A, 8A (when start).
INSTALLATION STEPS
see typical installation diagram in page 4
We recommend that you install your pump and basin in a clean location where there is
adequate room for servicing at a later date. Protection from freezing temperatures and good
ventilation should be considered as well, to provide the pump an environment for long life.
Assuming that you have a sump pit located in your basement floor... Your sump pit should be
constructed from concrete, brick, tile or more recently a sump basin made from plastic and/or
fiberglass. The minimum size of your sump pit must be 18” in diameter and no less than 25”
deep. When pit is ready, proceed to next step.
Friction losses in the discharge pipe must be taken into consideration when many elbows and
fittings are installed in the discharge line. Each elbows and fittings must be considered as 1
feet of head.
Never run the pump dry
. Damage to the seal may occur.
THE RUN OF THE PIPE FROM THE CHECK VALVE TO THE
EXISTING WASTE OR DRAIN LINE MUST NEVER BE SLOOPING
DOWNWARD EXCEPT WHEN CONNECTING TO SAME.
For a new installation, install your sewage basin in the excavation you have provided in the
basement floor of your home. Connect the necessary piping from your shower trap, toilet,
etc., to the inlet of your sewage basin, with the proper pipe and fittings (see diagram).
Cut a length of 40” to 42” of 2” ABS/DWV pipe. Cement the 2” ABS/DWV male adaptor to 2”
slip to one end of this pipe.
With your drill, make a 1/4” hole in the adaptor previously glued. This hole will prevent any
air locking wich might occur.
STEP 1
FRICTION LOSS IN
PIPE NOT INCLUDED
STEP 2
STEP 3
STEP 4