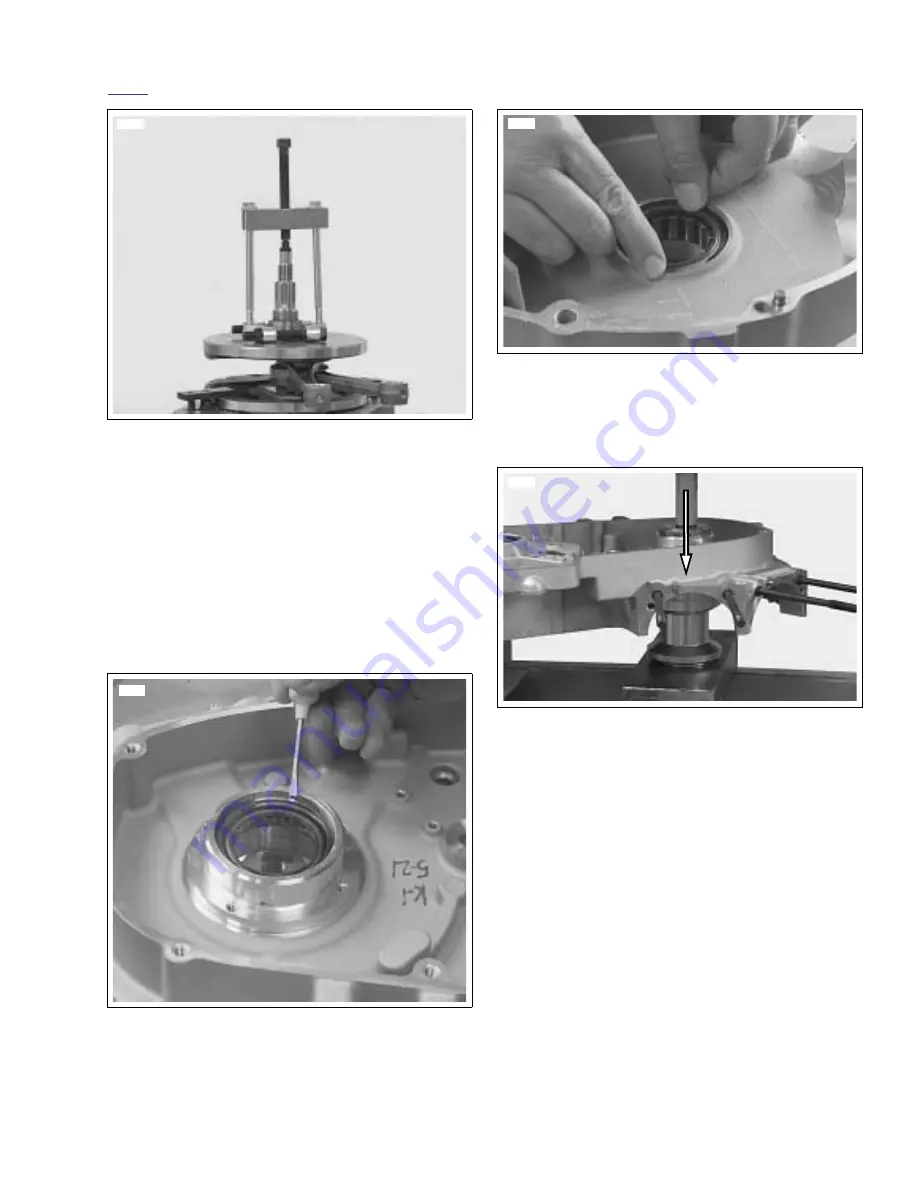
2005 Buell Firebolt: Engine
3-95
HOME
3.
See
Figure 3-138.
Place flywheel assembly in FLY-
WHEEL SUPPORT FIXTURE (Part No. HD-44385). Pull
sprocket shaft bearing inner race with WEDGE ATTACH-
MENT for CLAW PULLER (Part No. HD-95637-46A) with
BEARING RACE REMOVER/INSTALLER (Part No. HD-
34902B) and END CAP (Part No. HD-34902-7).
NOTE
Sprocket shaft bearing inner race does not need to be ground
once it is installed on the sprocket shaft.
4.
See
Figure 3-139.
Remove sprocket shaft oil seal retain-
ing ring.
5.
See
Figure 3-137.
Remove sprocket shaft oil seal 3) from
crankcase using Snap-On Tool (Part No. CJ 114, Body
Dent Puller)
6.
Remove outer thrust washer (4) next to sprocket shaft
bearing (6).
7.
See
Figure 3-140.
Remove sprocket shaft bearing retain-
ing ring from the inside of the left crankcase half.
8.
See
Figure 3-141.
Using CRANKCASE BEARING
REMOVER/INSTALLER with ADAPTER (Part No. B-
45655, HD-42720-2 and HD-46663) press sprocket shaft
bearing out of the left crankcase half.
NOTE
The bearing presses to the inside. There is a shoulder incor-
porated into the left crankcase half which allows the bearing
to be removed in one direction only.
Figure 3-138. Removing Sprocket Shaft Inner Bearing
Race
Figure 3-139. Sprocket Shaft Seal Retaining Ring
8760
8861
Figure 3-140. Removing Sprocket Shaft Bearing
Retaining Ring
Figure 3-141. Direction of Bearing Removal
From Left Crankcase
8762
8790
Содержание 2005 FIREBOLT
Страница 3: ......
Страница 59: ...HOME NOTES ...
Страница 61: ......
Страница 113: ...HOME NOTES ...
Страница 161: ......
Страница 233: ...HOME NOTES ...
Страница 267: ...HOME NOTES ...
Страница 311: ...HOME NOTES ...
Страница 407: ......
Страница 429: ...HOME NOTES ...
Страница 431: ......
Страница 477: ...HOME Figure 6 87 Crankcase Fasteners D b1016x3x Indicates Bolt Pattern Location One Behind Shifter Mechanism ...
Страница 483: ...HOME NOTES ...
Страница 485: ......
Страница 507: ...HOME NOTES ...
Страница 559: ......
Страница 567: ...HOME NOTES ...
Страница 585: ...B 18 2005 Buell Firebolt Electrical HOME 2005 XB Firebolt Main Harness 2005 XB Firebolt Main Harness ...
Страница 589: ...B 22 2005 Buell Firebolt Electrical HOME 2005 XB Firebolt Lighting Circuit 2005 XB Firebolt Lighting Circuit ...
Страница 593: ...B 26 2005 Buell Firebolt Electrical HOME 2005 XB Firebolt Starting Circuit 2005 XB Firebolt Starting Circuit ...
Страница 597: ...B 30 2005 Buell Firebolt Electrical HOME 2005 XB Firebolt Component Circuits 2005 XB Firebolt Component Circuits ...
Страница 601: ...D 2 2005 Buell Firebolt Appendix D HOME Figure D 2 Rear Brake Systems Top View b1115xbx ...
Страница 602: ...2005 Buell Firebolt Appendix D D 3 HOME Figure D 3 Rear Brake Systems Left Side View b1116xcx ...
Страница 613: ...HOME NOTES ...