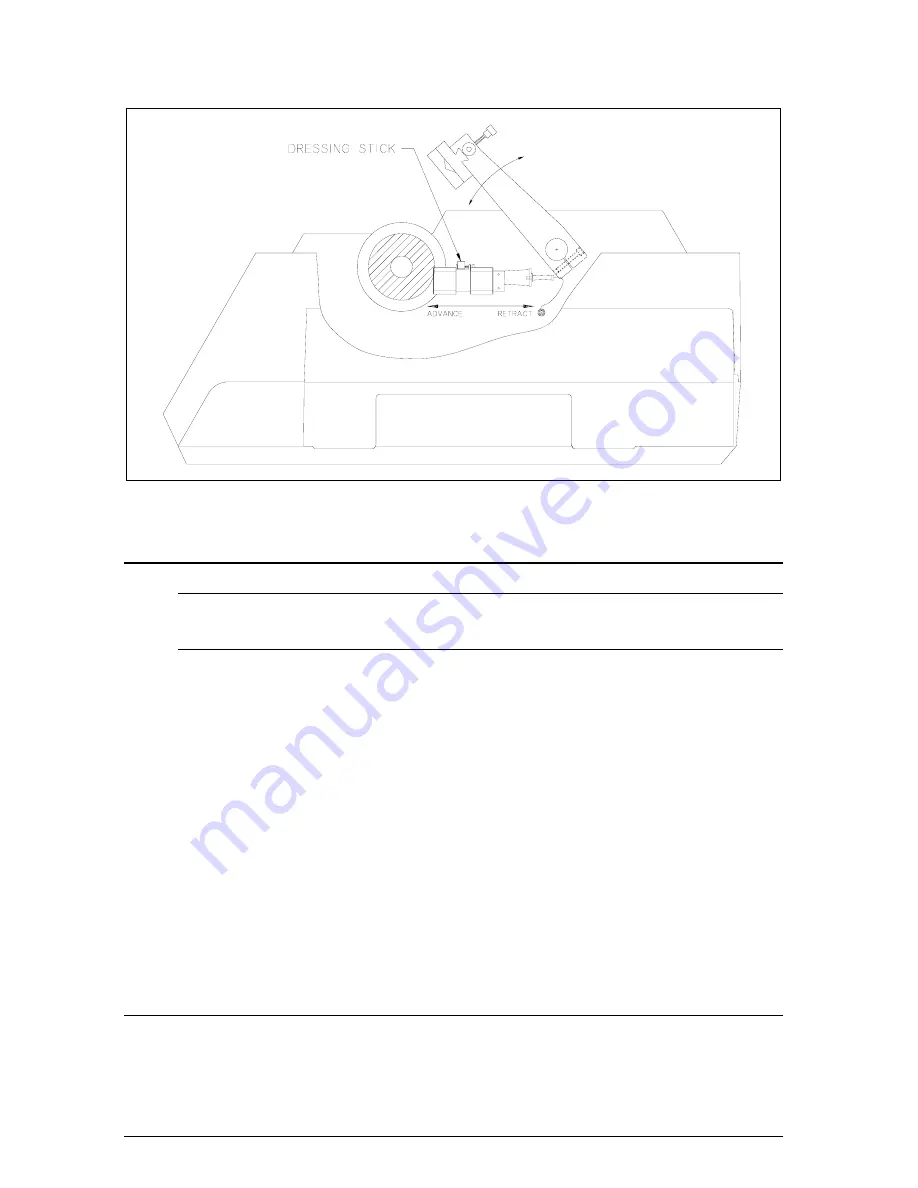
Figure 7
Dressing Chuck and Blade Dressing
Maintenance
General Specification:
1.
Sound level is 77dBA maximum.
Internal Coolant/Lubricant Recirculating System
When Coolant/Lubricant is contaminated with abrasive residue or swarf, it
should be discarded and replaced.
1.
To drain coolant; turn off unit, lift the hood, remove the blade and
flanges.
NOTE
Retract arm to the far left position.
2.
DISCONNECT THE POWER CORDS FROM THE CABINET
.
3.
Remove the Dressing Chuck Bracket and Coolant Assembly, and
Screen.
4.
Lift the Coolant Tank at the handle and pull so that the tank slides
horizontally.
5.
Thoroughly clean the Coolant Pump, Specimen Screen, Dressing
Chuck and Coolant Tank.
6.
Slide the Coolant Tank back into the cabinet.
7.
Place the components back into the tank as shown in Figure 8.
Connect the power cords into the correct connectors.
Cleaning the Unit
The ISOMET™ 2000 Precision Saw should be cleaned periodically to
prevent build-up of cutting residue and cutting fluids. Exterior painted
surfaces including the cutting chamber may be cleaned with non-abrasive
household cleaners.
11
MA112480-20
03/06/00
Содержание ISOMET 2000
Страница 1: ...ISO 9001 Registered Company ISOMET 2000 Precision Saw MA112480 20 03 06 00 ...
Страница 15: ...Figure 9 Parts Diagram for ISOMET 2000 Precision Saw 13 MA112480 20 03 06 00 ...
Страница 16: ...Figure 10 Parts Diagram for ISOMET 2000 Precision Saw 14 MA112480 20 03 06 00 ...
Страница 17: ...Figure 11 Parts Diagram for ISOMET 2000 Precision Saw 15 MA112480 20 03 06 00 ...
Страница 18: ...Figure 12 Parts Diagram for ISOMET 2000 Precision Saw 16 MA112480 20 03 06 00 ...
Страница 19: ...Figure 13 Parts Diagram for ISOMET 2000 Precision Saw 17 MA112480 20 03 06 00 ...
Страница 20: ...Figure 14 Parts Diagram for ISOMET 2000 Precision Saw 18 MA112480 20 03 06 00 ...
Страница 21: ...Figure 15 Parts Diagram for ISOMET 2000 Precision Saw 19 MA112480 20 03 06 00 ...
Страница 22: ...Figure 16 Parts Diagram for ISOMET 2000 Precision Saw 20 MA112480 20 03 06 00 ...
Страница 23: ...Figure 17 Parts Diagram for ISOMET 2000 Precision Saw 21 MA112480 20 03 06 00 ...
Страница 24: ...Figure 18 Parts Diagram for ISOMET 2000 Precision Saw 22 MA112480 20 03 06 00 ...
Страница 25: ...Figure 19 Parts Diagram for ISOMET 2000 Precision Saw 23 MA112480 20 03 06 00 ...
Страница 27: ...Figure 21 Parts Diagram for ISOMET 2000 Precision Saw 25 MA112480 20 03 06 00 ...
Страница 36: ...NOTES 34 MA112480 20 03 06 00 ...