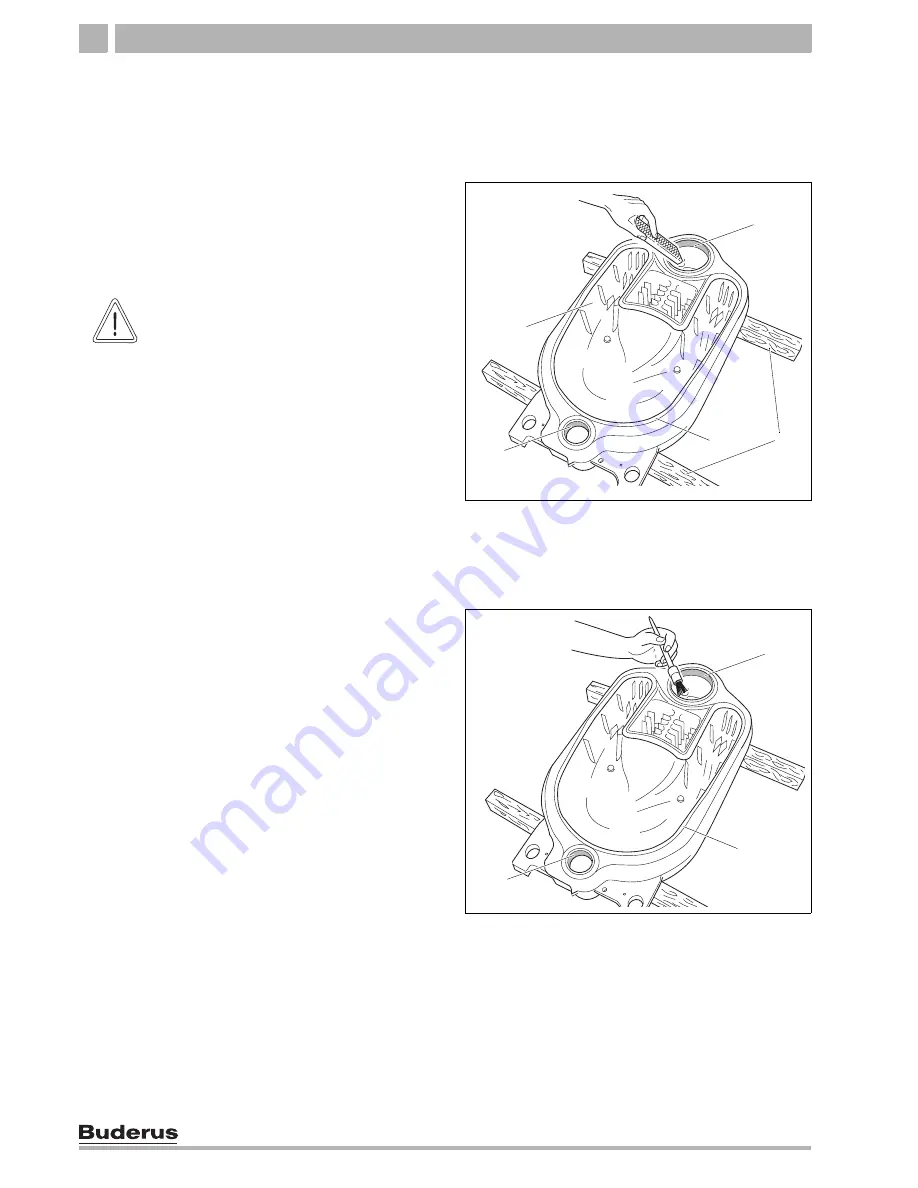
16
Installation and maintenance instructions Logano G215 US oil/gas-fired boilers • Issue 11/2004
We reserve the right to make any changes due to technical modifications.
Boiler block assembly
7
7.1
Assembly when delivered in sections
z
Assemble all boiler sections in accordance with the
following instructions and diagrams.
7.1.1 Preparing boiler sections
z
Position the rear section onto two wood blocks.
z
Clean the boiler hubs with sandpaper and a rag.
z
Remove any burrs with a file.
z
Clean the packing spring or packing groove with a
wire brush and rag.
z
Clean the hub sealing faces with a rag soaked in
cleaning agent.
z
Evenly coat the boiler hub sealing faces with red lead
putty.
z
Coat the packing spring or packing groove with
adhesive (adhesive base).
Fig. 5
Remove burrs
1
Boiler hubs
2
Back section
3
Wood blocks
4
Sealing spring
3
1
2
1
4
CAUTION!
RISK TO HEALTH and
DANGER OF BURNS
due to released vapors and easily
flammable cleaning agents.
z
When using red lead putty, adhesives
and solvents ensure adequate
ventilation inside the installation room.
z
When using solvents, avoid
open
flames, incandescence and sparks.
z
Please observe the manufacturer's
handling and safety instructions.
Fig. 6
Coat boiler hubs with red lead putty
1
Boiler hub sealing face
2
Sealing spring
1
1
2