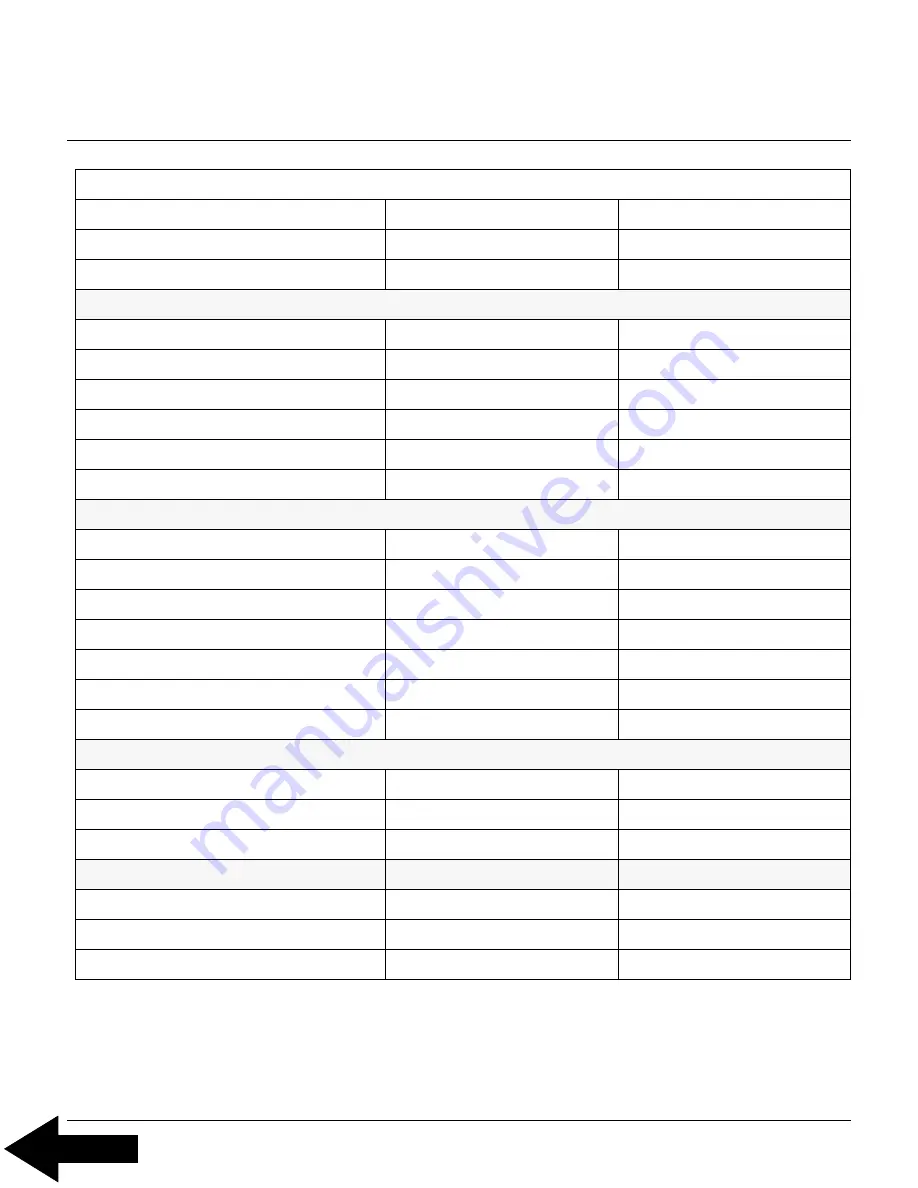
PS
M2.0
000
OE35
Version no
T-code
F-code
Section
C-code
Technical Service Data
34
Service Manual
1997-10-21
Minimum brush spring tension
40-65 oz
40-65 oz
Part number
300282-000
300281-000
HYDRAULIC STEERING PUMP
Revolutions/min at work pressure
Duty factor
Minimum brush length
0.625 in.
0.45 in.
Minimum commutator diameter
2.155 in.
1.80 in.
Minimum brush spring tension
26-28 oz
12-30 oz
Part number
200075
301492-000
HYDRAULIC SETTING
Lifting pressure at rated load
2400 psi
2400 psi
Steering relief valve setting
850 psi
850 psi
Brake relief valve setting
180 psi
180 psi
Pump flow
Tank volume
7.3 gal.
7.3 gal.
Normal temperature
Sunoco TH
Sunoco TH
< -10°F - 23°C
Texaco 15
Texaco 15
FUSES
Pump circuit fuse
400 Amp
400 Amp
Drive circuit fuse
300 Amp
300 Amp
Control fuse
15 Amp
15 Amp
BATTERIES
Dimension W x L x 13
f
in. x 36
3
in. x 31
3
in. 13
f
in. x 38
3
in. x 31
3
in.
Capacity (Min./Max. Amp-hrs.)
750/1000
400/750
Weight (Minimum)
1100 lb
1100 lb
MODEL
24 Volt
36 Volt
Return
Содержание OE35
Страница 2: ...Return ...
Страница 4: ...000 Version no T code F code Section C code BT Standard Codes 2 Service Manual 1997 07 15 Return ...
Страница 10: ... BT Products 8 Table of Contents Return ...
Страница 14: ...M 000 Version no T code F code Section C code Introduction Service Manual 12 Service Manual 1997 07 15 Return ...
Страница 16: ...M 001 Version no T code F code Section C code Contents Section M 14 Service Manual 1997 07 15 Return ...
Страница 40: ...PS M3 0 000 Version no T code F code Section C code Ordering Spare Parts 38 Service Manual 1997 07 15 Return ...
Страница 56: ...PS P3 0 000 OE35 Version no T code F code Section C code Lubrication Chart 54 Service Manual 1997 10 21 Return ...
Страница 60: ...PS S 000 Version no T code F code Section C code Contents Section S 58 Service Manual 1997 04 15 Return ...
Страница 124: ...PS S4 0 4130 001 OE35 Version no T code F code Section C code Torque Generator 122 Service Manual 1997 10 27 Return ...
Страница 132: ...PS S4 0 4150 001 OE35 Version no T code F code Section C code Steering System Pump 130 Service Manual 1997 10 29 Return ...
Страница 134: ...PS S4 0 4170 001 OE35 Version no T code F code Section C code Steering System 132 Service Manual 1997 10 29 Return ...
Страница 162: ...PS S5 3 5230 001 OE35 Version no T code F code Section C code Dash Display 160 Service Manual 1997 12 15 Return ...
Страница 200: ...PS S5 7 5450 000 OE35 Version no T code F code Section C code 1A Speed Contactor 198 Service Manual 1997 10 29 Return ...
Страница 222: ...PS S5 7 5610 000 OE35 Version no T code F code Section C code Pump Contactor 220 Service Manual 1997 10 29 Return ...
Страница 242: ...PS S5 5 5710 000 Version no T code F code Section C code EV100 Handset Operation 240 Service Manual 1997 09 15 Return ...
Страница 260: ...PS M6 1 6140 001 OE35 Version no T code F code Section C code Lift Pump Assembly 258 Service Manual 1997 12 15 Return ...
Страница 331: ...Return ...
Страница 332: ...BT Prime Mover Inc 3305 N Highway 38 Muscatine Iowa 52761 8800 U S A Tel 319 262 7700 Fax 319 262 7600 Return ...