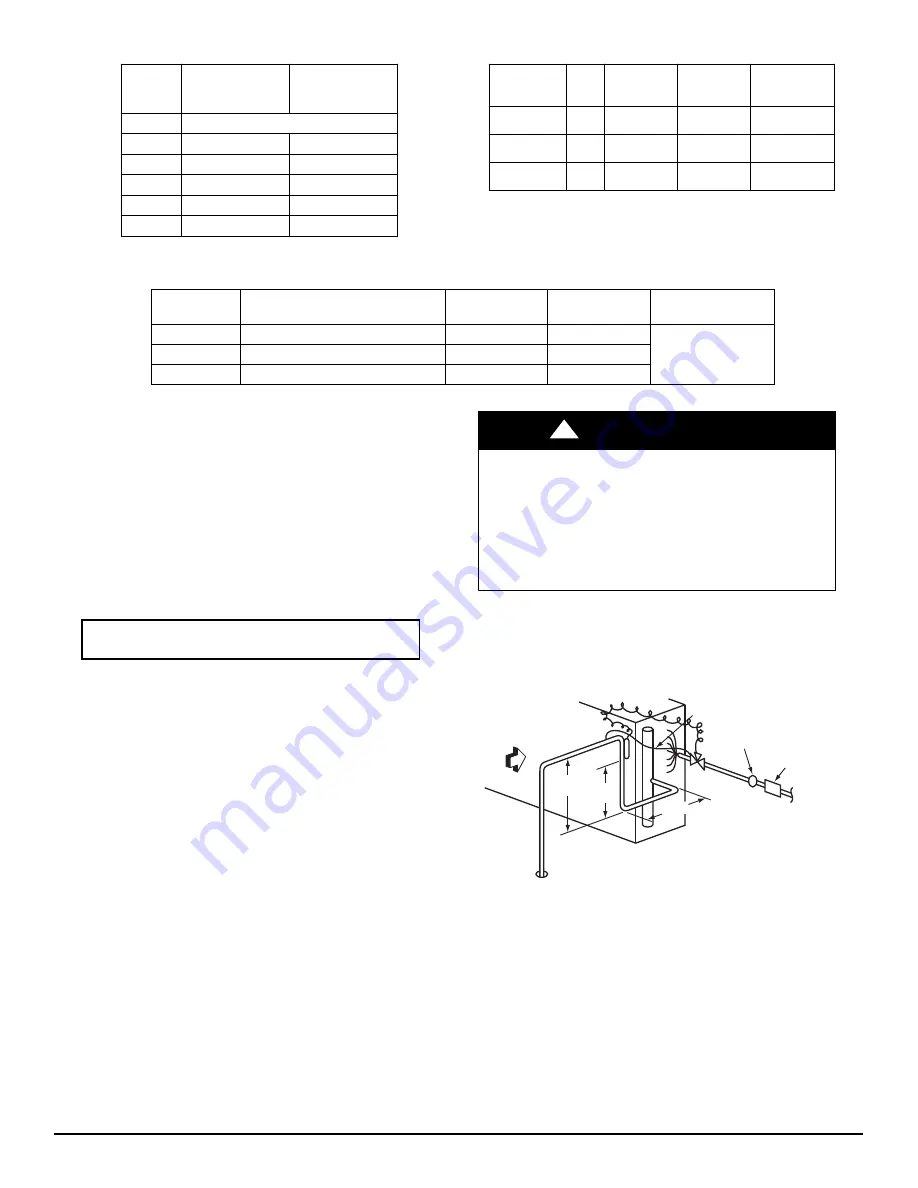
10
506 01 2303 01
Specifications are subject to change without notice.
Table 3 – Maximum Vapor Line Sizes
CHS
Size
CHS Unit
BELOW
ID Unit
CHS Unit
ABOVE
ID Unit
Max Diameter, Single Pipe (in.)
072*A/B
1-
1
/
8
1-
5
/
8
072*G/H
1-
1
/
8
1-
1
/
8
091*A/B
1-
3
/
8
1-
5
/
8
121*A/B
1-
5
/
8
1-
5
/
8
121*G/H
1-
3
/
8
1-
3
/
8
Table 4 – R--410A-duty Filter Drier(s)
Model-Size
Qty
Liquid
Line OD
Desiccant
Volume
Part
Number Ref
CHS072
1
3
/
8
-in
8 cu. in.
KH43LS088
CHS091
1
1
/
2
-in
16 cu. in.
KH43LS102
CHS121
1
1
/
2
-in
16 cu. in.
KH43LS102
Table 5 – Refrigerant Specialties Part Numbers
LIQUID LINE
SIZE (in.)
LIQUID LINE
SOLENOID VALVE (LLSV)
SOLENOID
COIL
SIGHT
GLASS
FILTER
DRIER
3
/
8
EF680033 plus EF680039 biflow kit
EF680037
KM680008
Provided with unit
See Table 4
1
/
2
EF680035 plus EF680039 biflow kit
EF680037
KM680004
5
/
8
EF680036 plus EF680039 biflow kit
EF680037
KM680005
Install Filter Drier and Moisture Indicator
—
Every unit MUST have a bi-directional filter drier in the
liquid line. Locate the filter drier(s) at the indoor unit, close
to the indoor coil’s thermal expansion valve (TXV) inlets.
CHS units include one R--410A-duty filter drier, shipped
in cartons attached to the unit basepan. Remove the filter
drier and prepare to install in the liquid line at the indoor
coil. Do not remove connection fitting plugs until ready to
connect and braze the filter drier into the liquid line
position. See Table 4.
IMPORTANT
: A refrigerant receiver is not
provided with the unit. Do not install a receiver.
Installation of liquid line moisture indicating sightglass in
each circuit is recommended. Locate the sightglass(es)
between the outlet of the filter drier and the TXV inlet.
Refer to Table 5 for recommendations on refrigeration
specialties.
Select the filter drier for maximum unit capacity and
minimum pressure drop. Complete the refrigerant piping
from the indoor unit to the outdoor unit before opening
the liquid and vapor service valves at the outdoor unit.
Install Liquid Line Solenoid Valves
—
It is recommended that a bi-directional solenoid valve be
placed in the main liquid line (see Figs. 5 & 6) between
the outdoor unit and the indoor coil. Locate the solenoid
valve at the end of the liquid line, near the outdoor unit
connections, with flow direction arrow pointed at the
outdoor unit. Refer to Table 5. (A liquid line solenoid
valve is required when the liquid line length exceeds 75 ft
[23 m].) This valve prevents refrigerant migration (which
causes oil dilution) to the compressor during the off cycle,
at low outdoor ambient temperatures. Wire the solenoid
according to the unit label diagram.
UNIT DAMAGE HAZARD
Failure to follow this caution may result in equipment
damage.
Failure to use a solenoid valve relay (SVR) PNO
HN61PC005 may cause overload of Comfort Alert
Diagnostic Module (CADM) and compressor alarm
lock out.
CAUTION
!
CAPACITY CONTROL LIQUID LINE SOLENOID
VALVE -- CHS units are single--stage only designs. DO
NOT USE a capacity control liquid line solenoid valve on
the indoor coil.
15 DIAMS
MIN
10
DIAMS
8 DIAMS
MIN
INDOOR
COIL CKT
AIRFLOW
TXV
SENSING
BULB
EQUALIZER LINE
SIGHT GLASS
A LOCATION
TXV
FILTER DRIER
A LOCATION
LEGEND
TXV —
Thermostatic Expansion Valve
C11036
Fig. 5 -- Location of Sight Glass(es) and Filter Driers
(typical CHS size 072 & 091)