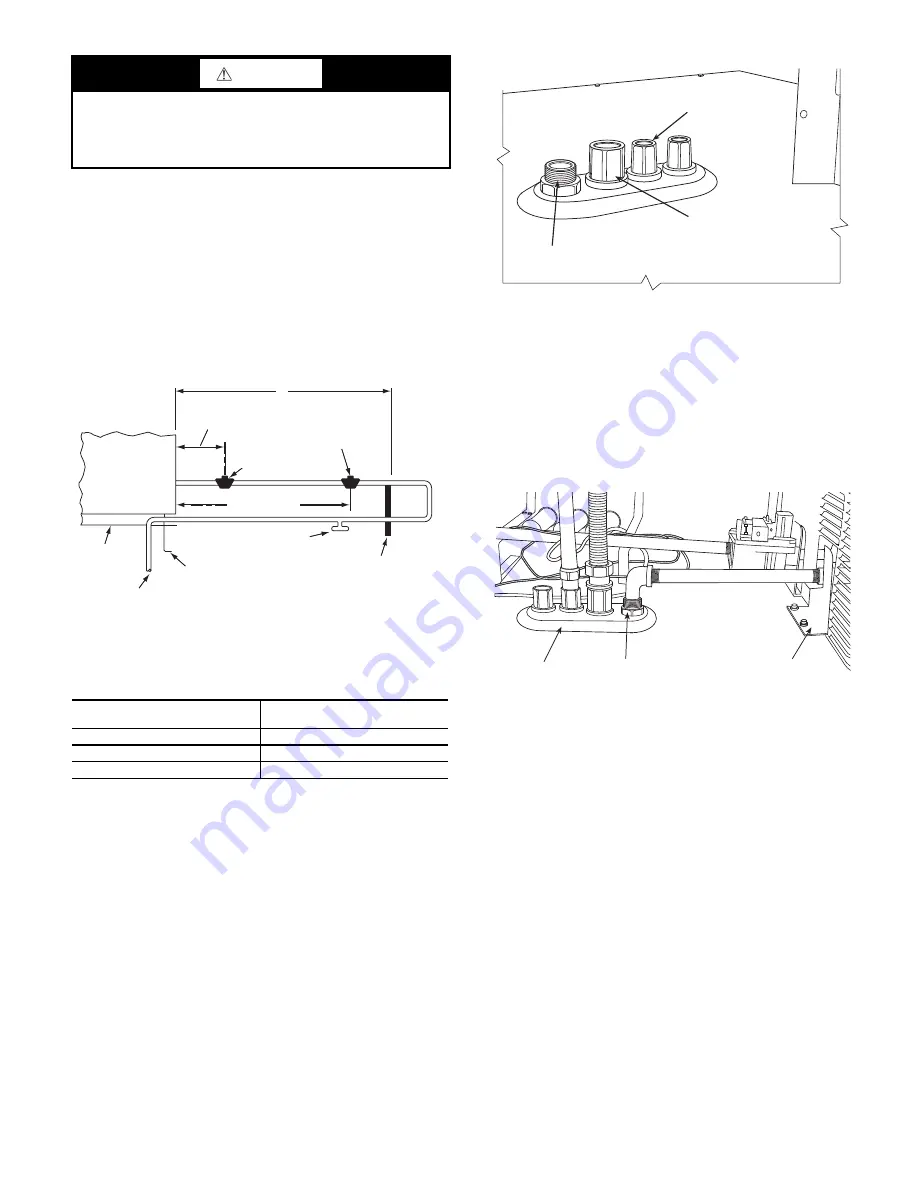
13
Install a gas supply line that runs to the unit heating section. Refer
to the NFPA 54/NFGC or equivalent code for gas pipe sizing data.
Do not use a pipe size smaller than
1
/
2
-in. Size the gas supply line
to allow for a maximum pressure drop of 0.5-in. wg (124 Pa) be-
tween gas regulator source and unit gas valve connection when
unit is operating at high-fire flow rate.
The gas supply line can approach the unit in three ways: horizon-
tally from outside the unit (across the roof), thru-curb/under unit
basepan (accessory kit required), or through unit basepan (factory
option or accessory kit required). Consult accessory kit installation
instructions for details on these installation methods. Observe
clearance to gas line components per Fig. 17.
Fig. 17 — Gas Piping Guide
(with Accessory Thru-the-Curb Service Connections)
FACTORY-OPTION THRU-BASE CONNECTIONS (GAS
CONNECTIONS)
This service connection kit consists of a
1
/
2
-in. NPT gas adapter
fitting (brass), a
1
/
2
-in. electrical bulkhead connector and a
3
/
4
-in.
electrical bulkhead connector, all factory-installed in the embossed
(raised) section of the unit basepan in the condenser section. See
Fig. 18 — Thru-Base Gas Connection Fittings
The thru-base gas connector has male and female threads. The
male threads protrude above the basepan of the unit; the female
threads protrude below the basepan.
Check tightness of connector lock nuts before connecting gas
piping.
Install a
1
/
2
-in. NPT street elbow on the thru-base gas fitting. At-
tach a
1
/
2
-in. pipe nipple with minimum length of 16-in. (406 mm)
(field-supplied) to the street elbow and extend it through the ac-
cess panel at the gas support bracket. See Fig. 19.
Fig. 19 — Gas Line Piping for 3 to 5 Ton Units Only
Other hardware required to complete the installation of the gas
supply line includes a manual shutoff valve, a sediment trap (drip
leg) and a ground-joint union. A pressure regulator valve may also
be required (to convert gas pressure from pounds to inches of pres-
sure). The manual shutoff valve must be located within 6 ft (1.83
m) of the unit. The union, located in the final leg entering the unit,
must be located at least 9 in. (230 mm) away from the access panel
to permit the panel to be removed for service. If a regulator valve
is installed, it must be located a minimum of 4 ft (1220 mm) away
from the unit’s flue outlet. Some municipal codes require that the
manual shutoff valve be located upstream of the sediment trap.
See Fig. 20 and 21 for typical piping arrangements for gas piping
that has been routed through the sidewall of the curb. See Fig. 22
for typical piping arrangement when thru-base is used. Ensure that
all piping does not block access to the unit’s main control box or
limit the required working space in front of the control box.
CAUTION
Failure to follow this caution may result in equipment damage.
When connecting the gas line to the unit gas valve, the in-
staller MUST use a backup wrench to prevent damage to
the valve.
X
BASE UNIT
BASE RAIL
ROOF
CURB
9” MINIMUM CLEARANCE
FOR PANEL REMOVAL
MANUAL GAS
SHUTOFF VALVE
*
GAS
REGULATOR
*
48” MINIMUM
DRIP LEG
PER NFGC
*
FIELD-FABRICATED
SUPPORT
*
FROM
GAS
METER
LEGEND
*Field supplied.
NOTE: Follow all local codes.
NFGC
— National Fuel Gas
Code
STEEL PIPE NOMINAL
DIAMETERS (IN.)
SPACING OF SUPPORTS
X DIMENSION (FT.)
1
/
2
6
3
/
4
or 1
8
1-
1
/
4
or Larger
10
LOW VOLTAGE
CONDUIT
CONNECTOR
HIGH VOLTAGE
CONDUIT
CONNECTOR
BRASS FITTING FOR 3 TO 6 TON UNITS.
EMBOSSMENT
BRASS FITTING
FOR 3-6 TON UNITS
SUPPORT
BRACKET
Содержание 582J 04-06
Страница 4: ...4 Fig 2 Unit Dimensional Drawing ...
Страница 5: ...5 Fig 2 Unit Dimensional Drawing cont ...
Страница 21: ...21 Fig 38 Typical Perfect Humidity Adaptive Dehumidification System Humidistat Wiring ...
Страница 23: ...23 Fig 40 Typical Control Wiring Diagram Electro Mechanical with W7212 ...
Страница 25: ...25 Fig 43 Typical IGC Control Wiring Diagram ...